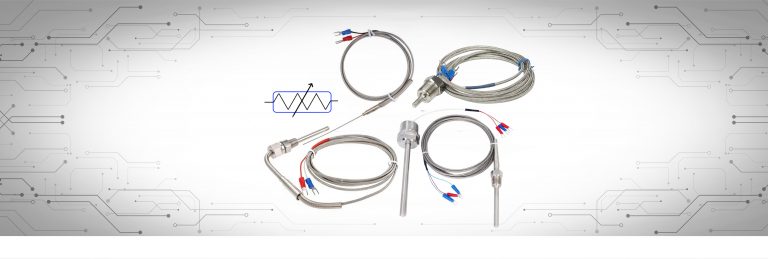
How to Choose a RTD Probe for your Wireless Temperature Sensor
Types of RTD Sensor RTDs (Resistance Temperature Detectors) come in various types based on their construction, resistance values, and the material used. Here are the
These two types of sensors might seen very similar on the surface, however they are in fact quite different. They have different operational mechanics, mainly one relies on current measurement, the other on voltage. Additionally, they find application in very different use-case scenarios and more often than not one is a lot better suited than the other for solving a particular problem.
An RTD (Resistance Temperature Detector) temperature sensor is a type of sensor used to measure temperature by correlating the change in resistance of the RTD element with the change in temperature. The basic principle behind its operation is the predictable increase in the resistance of certain materials, particularly metals, as their temperature rises. Current is run through the element and its change (based on the variation of the resistance) is measured and converted into a temperature measurement.
Industrial IoT Wireless RTD Temperature Sensor
$262.95 - $283.95A thermocouple is a temperature sensor consisting of two different metals joined at one end. When there is a temperature difference between the joined end (known as the “hot junction” or “measuring junction”) and the other end (known as the “cold junction” or “reference junction”), a small voltage is generated. This voltage, known as the Setback voltage, is proportional to the temperature difference between the two ends. By measuring this voltage, the temperature can be determined.
Types of RTD Sensor RTDs (Resistance Temperature Detectors) come in various types based on their construction, resistance values, and the material used. Here are the
An RTD temperature sensor is known for its accuracy, stability, and repeatability across a wide range of temperatures. Given these characteristics, RTDs are suited for a variety of applications where precise temperature measurement is critical. Here are some scenarios and applications where an RTD temperature sensor would be beneficial:
Industrial Process Control:
Food & Beverage Processing:
Pharmaceutical Manufacturing:
Laboratory Environments:
Heating, Ventilation, and Air Conditioning (HVAC):
Aerospace and Defense:
Cryogenics:
Semiconductor Manufacturing:
Renewable Energy Systems:
While these are just a few examples, it’s evident that RTDs are versatile and can be employed in any application requiring accurate and consistent temperature measurement. The choice between an RTD and another type of sensor, like a thermocouple, will often depend on the specific requirements of the application, such as the desired temperature range, accuracy, and environmental conditions.
As RTDs provide a higher degree of accuracy, stability and linearity they are more suitable for Industrial applications where precision of measurements is more important than being cost efficient.
Thermocouples are temperature sensors that are robust, versatile, and capable of measuring a wide range of temperatures. Their simplicity, broad temperature capabilities, and relative cost-effectiveness make them suitable for many applications. Here are some scenarios and applications where thermocouple sensor are commonly used:
Industrial Process Control:
Food & Beverage Processing:
Combustion Systems:
Laboratory Environments:
Power Generation:
Healthcare:
Automotive:
Semiconductor Manufacturing:
Environmental Monitoring:
RTD: An Introduction Resistance Temperature Detectors (RTDs) have emerged as a precise and prevalent method for measuring temperature. While numerous RTD configurations exist, they predominantly
Both RTDs and thermocouples are widely used for temperature measurement, each with its own set of advantages and disadvantages. Here’s a comparison:
Advantages:
Disadvantages:
Advantages:
Disadvantages:
The choice between an RTD and a thermocouple depends on the specific requirements of the application, such as the desired temperature range, accuracy, environment, response time, and budget.
Both RTDs and Thermocouples find use in a wide-range of applications, some of which overlap. This does not mean they are interchangeable as their main characteristics are quite different. As a rule of thumb:
RTDs are more expensive and better suited for IIoT applications that cost is not a limiting factor and very precise, accurate and stable readings in a narrow temperature range are required. They are best suited for controlled environments where environmental protection level and robustness of the sensor itself is not essential.
Thermocouples are cheaper, easier to provision in large quantities and overall more versatile. They are suitable for measurements in a wide temperature range, they have higher response time and are more robust. However, they have lower accuracy, stability and precision, making them more suitable for applications with a wider-range of temperature range for example outdoor scenarios where environmental conditions are a playing factor (Thermocouples are more robust than RTDs).
RTD: An Introduction Resistance Temperature Detectors (RTDs) have emerged as a precise and prevalent method for measuring temperature. While numerous RTD configurations exist, they predominantly adopt either a two-wire, three-wire, or four-wire system. Further variations stem from differences in resistance, typically seen between Pt100 and Pt1000 RTDs. These types of sensors as the name implies work based on the fact that when the temperature of the metal in the sensor
Principles of Operation and Types of RTDs Resistance Temperature Detectors (RTDs) are a type of temperature measurement device that relies on the ability of certain metal materials (most notably Platinum) to increase their resistance with the increase in temperature. These are utilized together with a current source, where as the temperature changes so does the current (as a result of the changing resistance) in order to produce temperature measurements. Depending
What are Thermocouples / RTDs These two types of sensors might seen very similar on the surface, however they are in fact quite different. They have different operational mechanics, mainly one relies on current measurement, the other on voltage. Additionally, they find application in very different use-case scenarios and more often than not one is a lot better suited than the other for solving a particular problem. RTD Temperature Sensors