Device Overview
The Machine Uptime Monitor is a device specifically designed to track machine and production uptime in industrial settings. It is a flexible device that can be configure to observe one or more events via different input types – accelerometer, magnetometer, current sensor, break beam sensor, photo eye sensor, reflector sensor, current sensor.
It has long range wireless capabilities utilizing robust Mesh networking protocols with high level of security and network reliability. It is compact, durable and powered by long lasting batteries.
Features
- Industrial Grade Machine Uptime Monitoring
- Measure Production Uptime
- Measure Number of Cycles
- Dry Contact Closure Input
- Wet Contact Closure Input
- Acceleration Motion Detection based Uptime calculator
- Magnetic Field Detection based Uptime calculator
- Current-based Uptime calculator
- Encrypted Communication with 2 Mile Wireless Range
- Operating Temperature Range -40 to +60 °C
- Humidity Range 0-90%
- Wall-Mounted or Magnet Mounted IP65 Rated Enclosure
- For Indoor and Outdoor Use
- Many Gateway and Modem Options Available
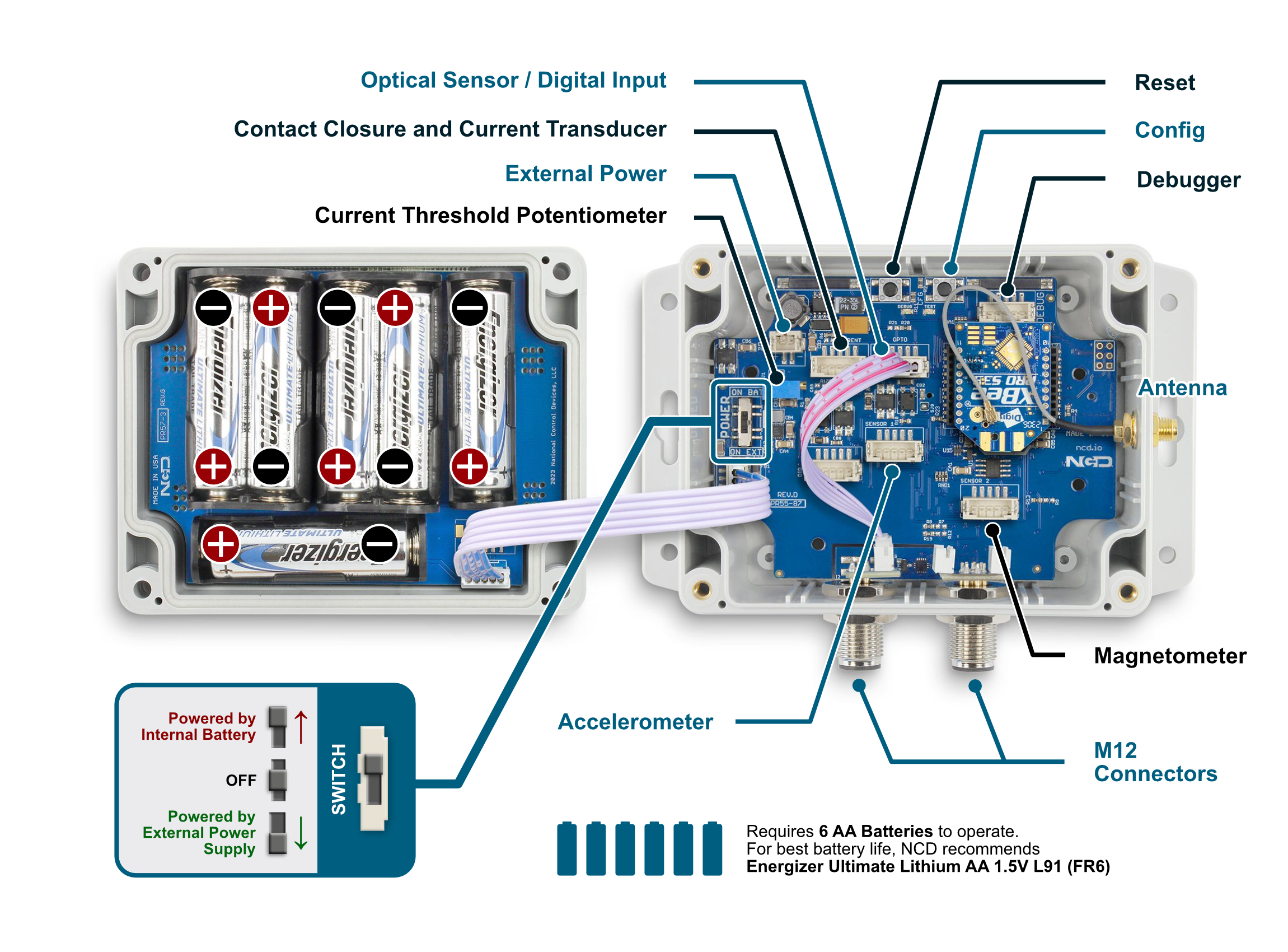
Wireless Technology
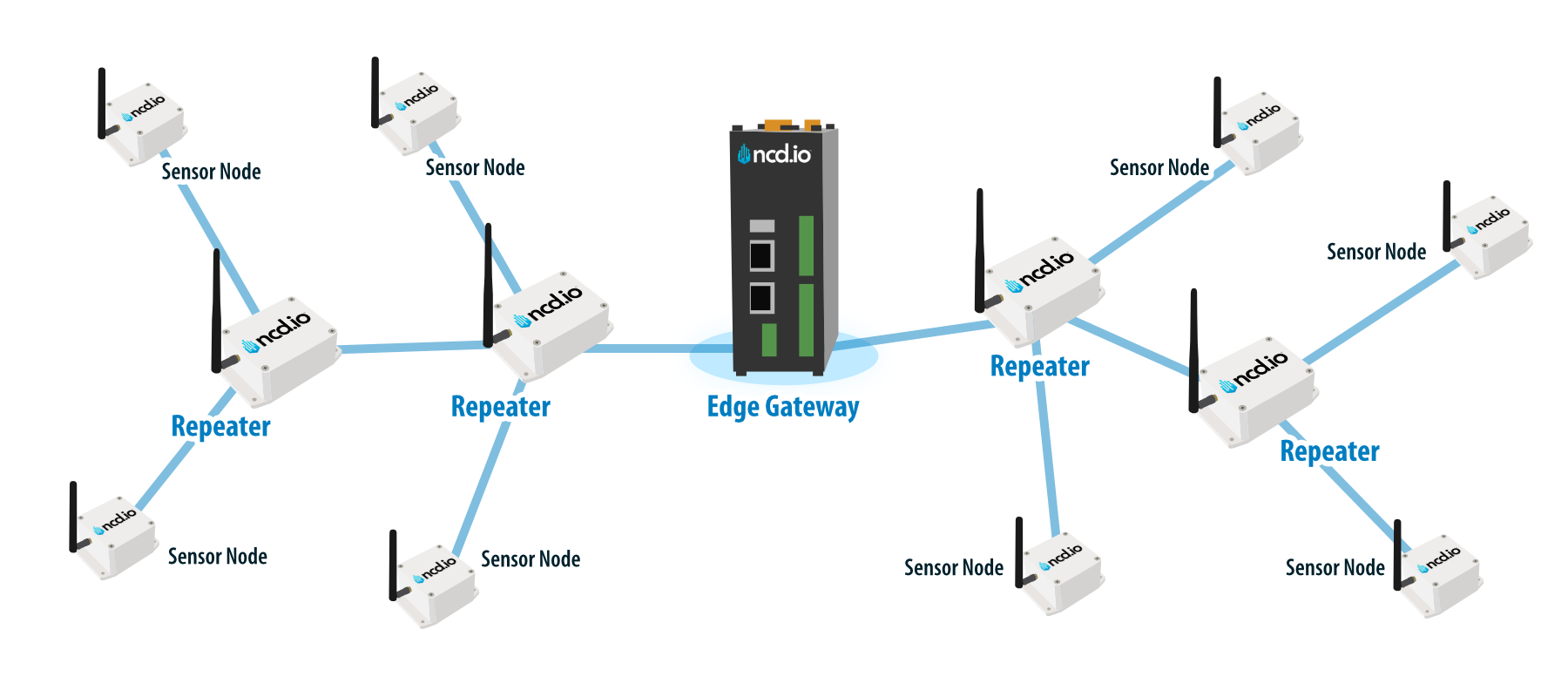
The NCD Industrial range of sensors utilizes DigiMesh, a proprietary networking technology designed by Digi® International. It is especially suitable for IIoT applications as it provides a number of benefits over conventional wireless stacks:
- Long range – up to 1000 feet in urban environments and 2 miles+ in open areas with the included antennas
- Mesh networking topology – no single point of failure, self healing network with high redundancy.
- Long battery life due to low power consumption – up to 10 years
- Simplified provisioning – extending the mesh network via repeater at no additional configuration complexity
- Works in the 868MHz, 900MHz and 2.4GHz bands – worldwide region interoperability.
If you want to learn more about DigiMesh and how it compares with another popular IoT stack (LoRaWAN) head to the article below:
IoT Wireless Sensor Networks: Digi®Mesh vs LoRaWAN®
Battery Life
Lorem ipsum dolor sit amet, consectetur adipiscing elit. Ut elit tellus, luctus nec ullamcorper mattis, pulvinar dapibus leo.
Specifications | Minimum | Nominal | Maximum | Notes |
---|---|---|---|---|
Batteries | 2 | 6 | 6 | May be Powered by 2 or 4 AA Batteries |
Battery Life 1 TPD (Transmissions per Day) | 10 Years | Estimation is based on a 30 minute interval | ||
Battery Life 12 TPD (Transmissions per Day) | 8 Years | Estimation is based on a 30 minute interval | ||
Battery Life 24 TPD (Transmissions per Day) | 5 Year | Estimation is based on a 30 minute interval | ||
Battery Life 96 TPD (Transmissions per Day) | 3 Year | Estimation is based on a 30 minute interval |
The Truth About Battery Life
Under the best of circumstances, the best non-rechargeable batteries commonly available today are limited to a 10 year non-working shelf life in a room temperature environment. Factors such as actual usage, temperature, and humidity will impact the working life. Be wary of any battery claims in excess of 10 years, as this would only apply to the most exotic and expensive batteries that are not commonly available. Also note that most battery chemistries are not rated for use in extreme temperatures. NCD only uses the best Non-Rechargeable Lithium batteries available today, which are also rated for use in extreme temperatures and have been tested by our customers in light radioactive environments. Lithium batteries offer a 10 year maximum expected shelf life due to limitations of battery technology. NCD will never rate sensor life beyond the rated shelf life of the best batteries available today, which is currently 10 years.
Applications & Use-cases
This sensor is a versatile device that brings a new level of precision and reliability to uptime monitoring across a wide range of industrial applications. Its unique combination of digital and analog sensing technologies, coupled with robust wireless communication and a durable enclosure, makes it an ideal choice for diverse environments and challenging operational conditions.
Machine Uptime Applications
Manufacturing Plants
In manufacturing settings, the ability to monitor machine uptime accurately is crucial for minimizing downtime and maximizing productivity. The sensor’s multi-sensor functionality enables detailed tracking of production uptime and cycle counts. Its dry and wet contact closure inputs, along with current-based, acceleration motion detection, and magnetic field detection-based uptime calculators, provide a comprehensive view of machine performance. This ensures manufacturing plants can swiftly identify and address issues, maintain high operational standards, and optimize production schedules.
Automotive Production Lines
Automotive manufacturing demands high precision and efficiency, where any interruption can lead to significant financial losses. The Machine Uptime sensor’s IP65 rating and ability to operate in extreme temperatures (-40 to +60 °C) and humidity (0-90%) conditions make it suitable for the rigorous demands of automotive production lines. Its real-time monitoring capabilities allow for immediate detection of performance deviations, facilitating rapid response to prevent downtime and ensure continuous production flow.
Food Processing Facilities
In the food processing industry, hygiene and safety are paramount. The sensor’s wall-mounted or magnet-mounted IP65 rated enclosure ensures it can withstand the wet and variable temperature environments typical in food processing plants without compromising performance. Moreover, its versatile connectivity options support adherence to strict quality and safety standards by enabling seamless data integration with existing quality management systems.
Chemical and Pharmaceutical Industries
For chemical and pharmaceutical manufacturing, maintaining consistent operational conditions is critical to product quality and compliance with regulatory standards. The Machine Uptime sensor’s encrypted communication and its ability to monitor machinery in real-time provide an extra layer of security and compliance assurance. The sensor’s accurate detection capabilities, including current-based and magnetic field-based measurements, ensure precise monitoring of sensitive production processes, aiding in the early identification of equipment malfunctions that could affect product quality or worker safety.
Mining and Heavy Machinery Operation
The rugged design of the Machine Uptime sensor, combined with its long-range wireless communication capabilities (up to 2 miles), makes it exceptionally well-suited for the harsh and remote environments of mining and heavy machinery operations. Its battery-powered operation allows for easy installation in locations where power sources are not readily available, ensuring continuous monitoring of equipment uptime. This is critical for identifying potential equipment failures before they occur, reducing costly unplanned downtime and enhancing operational efficiency in these industries.
Machine Uptime Use-cases
Overall Equipment Effectiveness (OEE)
OEE is a critical metric in manufacturing that evaluates equipment performance by combining availability, performance, and quality factors. In IoT-enabled environments, OEE is enhanced through real-time data collection and analysis, facilitating predictive maintenance and process optimization. IoT devices monitor equipment to automatically calculate OEE scores, predict failures, and identify inefficiencies, enabling proactive adjustments and informed decision-making.
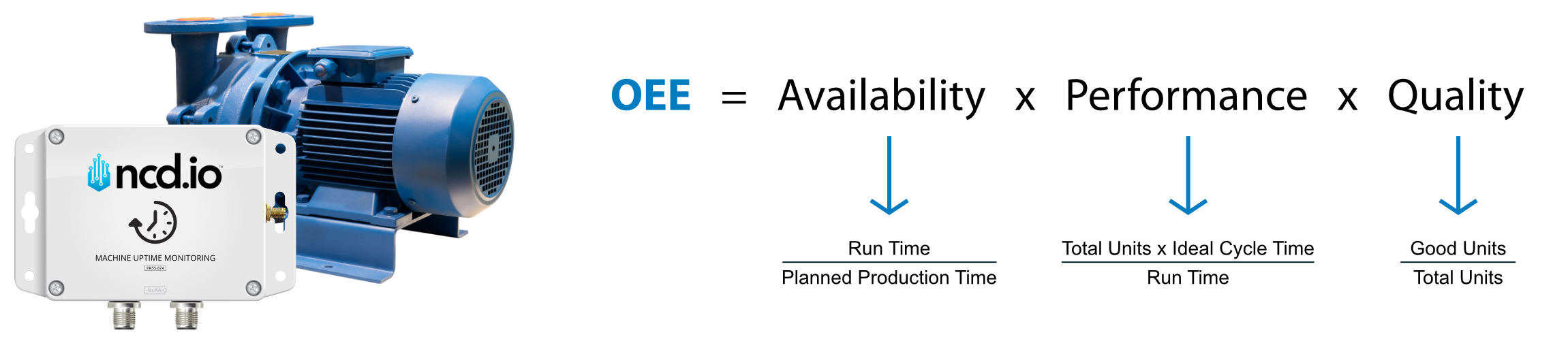
Machine Utilization
Machine utilization measures the effectiveness of industrial equipment by tracking the proportion of time a machine is actively operating against its available time. Enhanced by IoT technology, machine utilization monitoring allows for real-time data collection, enabling more accurate and dynamic assessments of machine performance. IoT sensors gather operational data, helping to pinpoint underutilization issues, streamline production processes, and reduce downtime through timely interventions.
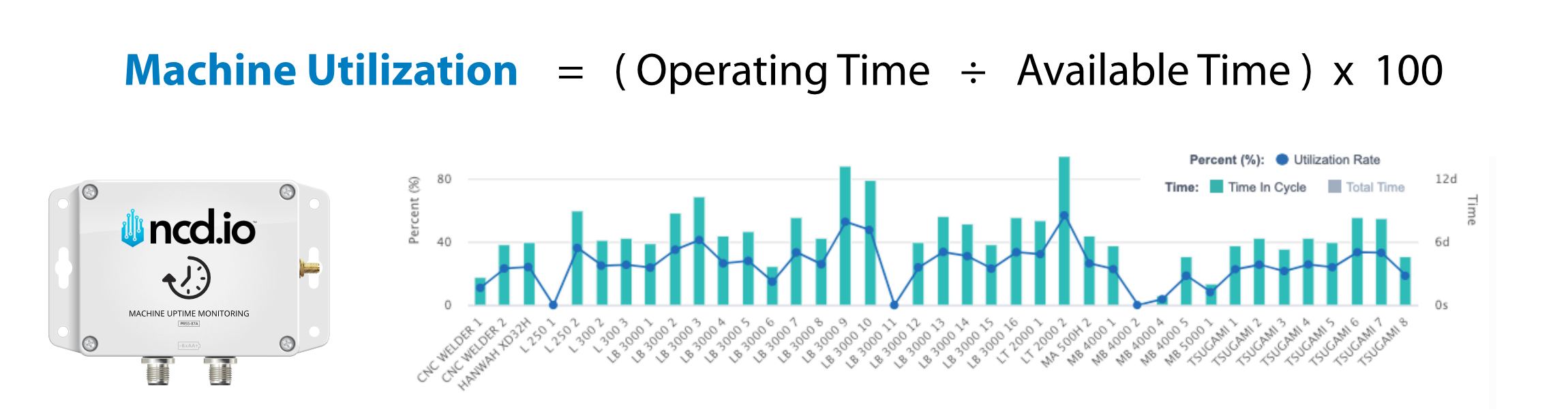
Productivity Measurement
Productivity measurement in industrial settings quantifies the efficiency and output of manufacturing processes. Integrating IoT technology enables real-time tracking and analytics, improving the accuracy and responsiveness of productivity assessments. By collecting data directly from production lines through IoT sensors, companies can immediately detect productivity fluctuations, analyze performance trends, and identify areas needing improvement.
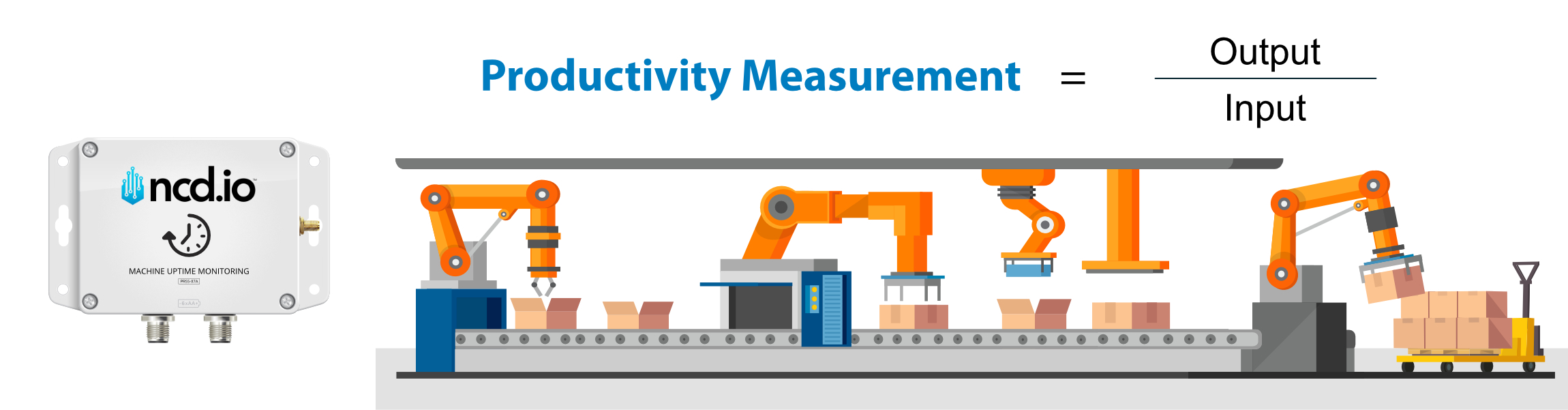
Downtime Tracking
Downtime tracking in manufacturing is crucial for identifying and minimizing periods when equipment is not operational. Enhanced by IoT technology, downtime tracking becomes more precise and automated, allowing for the continuous monitoring of equipment status. IoT sensors can immediately detect when machines halt production and diagnose potential causes, such as mechanical failures or software issues.
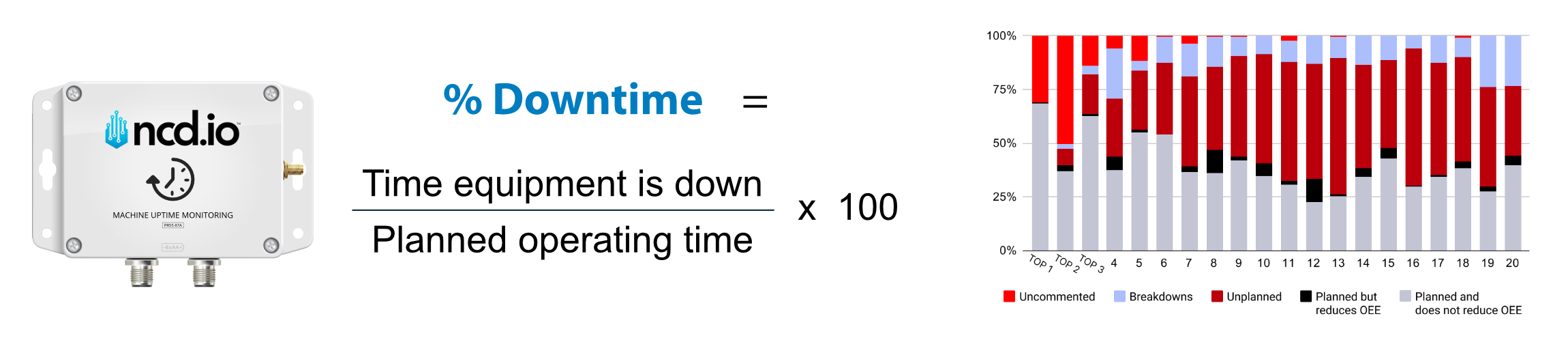