Device Overview
The 3 Channel Production Counter is a device specifically designed to track production counts and machine uptime events in industrial settings. It is a flexible device that can be configured to observe one or more events via different input types – break beam sensor, photo eye sensor, reflector sensor, dry contact closure, and wet contact closure.
It has long range wireless capabilities utilizing robust Mesh networking protocols with high level of security and network reliability. It is compact, durable, and powered by long-lasting batteries.
Features
- Industrial Grade Production Count Monitoring
- Measure Production Uptime
- Measure Number of Cycles
- Dry Contact Closure Input
- Wet Contact Closure Input
- Beam Break and Photo Eye Sensor Input-Based Event Detection
- Encrypted Communication with 2 Mile Wireless Range
- Operating Temperature Range -40 to +60 °C
- Humidity Range 0–90%
- Wall-Mounted or Magnet Mounted IP65 Rated Enclosure
- For Indoor and Outdoor Use
- Many Gateway and Modem Options Available
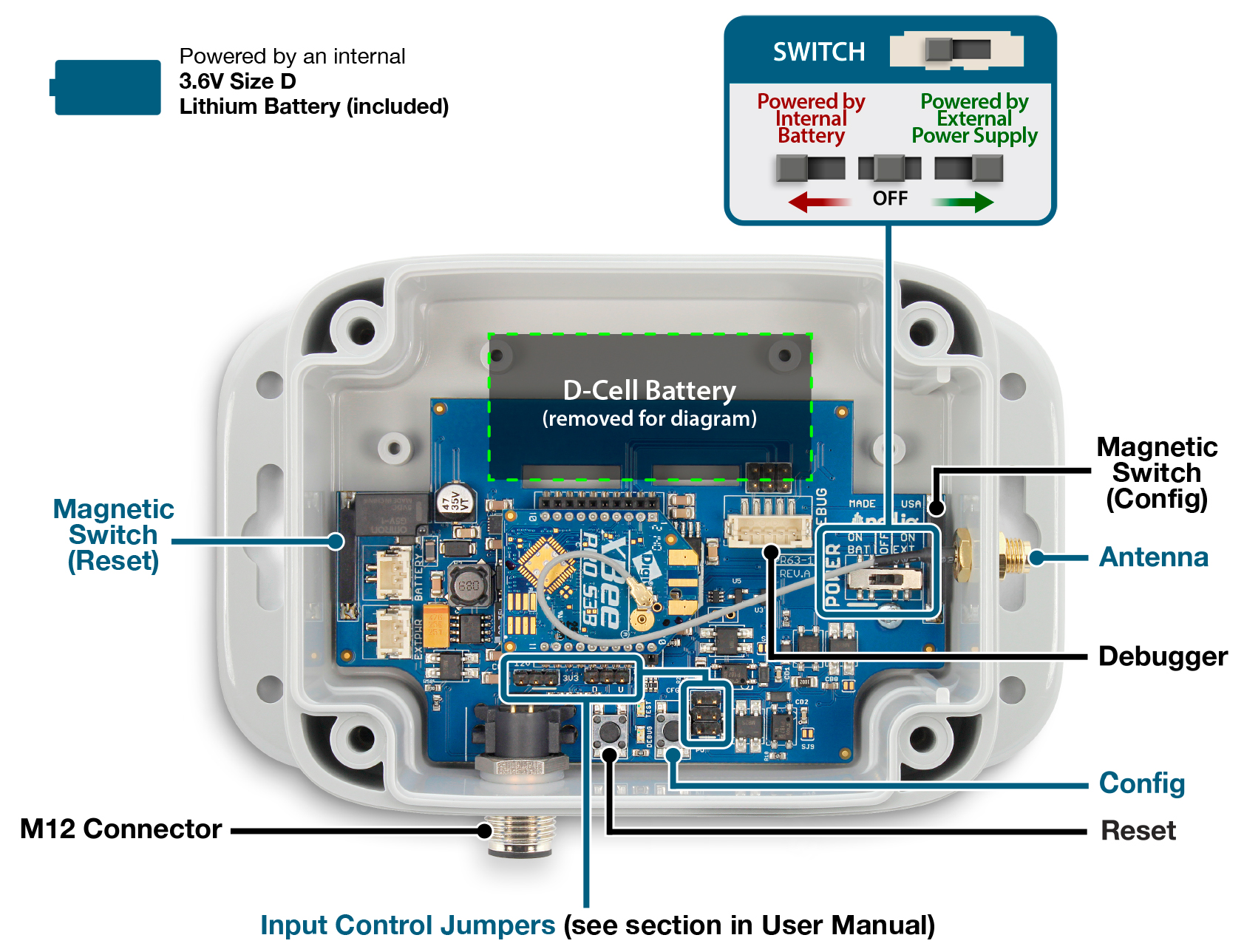
Wireless Technology
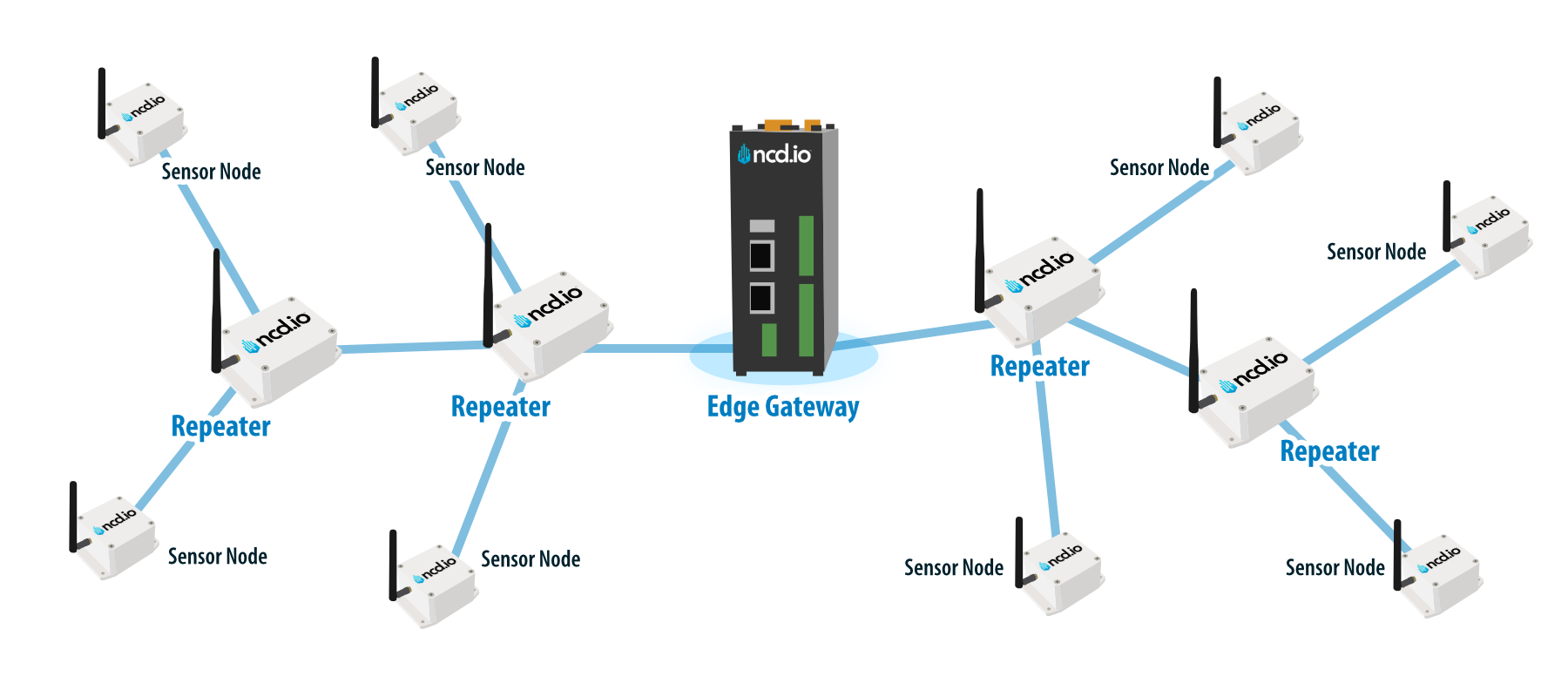
The NCD Industrial range of sensors utilizes DigiMesh, a proprietary networking technology designed by Digi® International. It is especially suitable for IIoT applications as it provides a number of benefits over conventional wireless stacks:
- Long range – up to 1000 feet in urban environments and 2 miles+ in open areas with the included antennas
- Mesh networking topology – no single point of failure, self healing network with high redundancy.
- Long battery life due to low power consumption – up to 10 years
- Simplified provisioning – extending the mesh network via repeater at no additional configuration complexity
- Works in the 868MHz, 900MHz and 2.4GHz bands – worldwide region interoperability.
If you want to learn more about DigiMesh and how it compares with another popular IoT stack (LoRaWAN) head to the article below:
IoT Wireless Sensor Networks: Digi®Mesh vs LoRaWAN®
Battery Life
Specifications | Minimum | Nominal | Maximum | Notes |
---|---|---|---|---|
Batteries size | 16000mAh | This device has a single D-Cell (LR20) battery | ||
Battery Life 1 TPD | 10 Years | TPD Transmissions per Day | ||
Battery Life 12 TPD | 8 Years | TPD Transmissions per Day | ||
Battery Life 24 TPD | 5 Year | TPD Transmissions per Day | ||
Battery Life 96 TPD | 3 Year | TPD Transmissions per Day |
The Truth About Battery Life
Under the best of circumstances, the best non-rechargeable batteries commonly available today are limited to a 10 year non-working shelf life in a room temperature environment. Factors such as actual usage, temperature, and humidity will impact the working life. Be wary of any battery claims in excess of 10 years, as this would only apply to the most exotic and expensive batteries that are not commonly available. Also note that most battery chemistries are not rated for use in extreme temperatures. NCD only uses the best Non-Rechargeable Lithium batteries available today, which are also rated for use in extreme temperatures and have been tested by our customers in light radioactive environments. Lithium batteries offer a 10 year maximum expected shelf life due to limitations of battery technology. NCD will never rate sensor life beyond the rated shelf life of the best batteries available today, which is currently 10 years.
Applications & Use-cases
This sensor is a versatile device that brings a new level of precision and reliability to uptime monitoring across a wide range of industrial applications. Its unique combination of digital and analog sensing technologies, coupled with robust wireless communication and a durable enclosure, makes it an ideal choice for diverse environments and challenging operational conditions.
3 Channel Production Counter Uptime Applications
Multi-Point Production Tracking
The 3 Channel Production Counter can monitor up to three independent machines, stations, or production processes simultaneously, making it a powerful tool for small to mid-sized manufacturing operations that need to maximize resource efficiency. Instead of deploying multiple single-channel devices, one unit can capture activity from multiple sensors—such as break beam or photo eye sensors—strategically placed at different points along a production line. This enables comprehensive monitoring of throughput across multiple product types or process stages, helping managers identify inefficiencies, balance workloads, and make informed decisions to improve overall output.
Redundancy and Accuracy Verification
In environments where production speed is high or where precision is critical—such as pharmaceutical packaging or electronics assembly—the risk of missed or duplicate counts can significantly impact quality and compliance. By connecting different types of sensors (e.g., both a photo eye and a break beam sensor) to the device’s input channels for the same event stream, the 3 Channel Production Counter enables redundancy and cross-verification. This dual-sensor setup allows the system to validate count events from two independent sources, improving reliability and reducing the likelihood of errors. It’s especially useful for audits, quality assurance protocols, or where regulatory compliance demands accurate event logging.
Event-Based Maintenance Triggers
By monitoring the number of production cycles or units processed on specific machines, the 3 Channel Production Counter can serve as an effective tool for predictive or preventive maintenance. Each channel can be assigned a threshold count that, once reached, signals the need for routine inspection, lubrication, or component replacement. This approach allows maintenance teams to intervene before equipment failure occurs, reducing unplanned downtime and avoiding costly repairs. Especially in high-volume operations where machinery is constantly running, using event counts to drive maintenance scheduling ensures equipment reliability and extends asset lifespan while minimizing disruption to production schedules.
3 Channel Production Counter Use-cases
Warehouse Order Fulfillment Tracking
In a logistics center, the device is mounted at three packaging lanes. Each lane uses a reflector sensor to detect when a parcel enters the packing zone. By tracking counts per lane, the facility can optimize labor distribution, identify underperforming stations, and ensure balanced order fulfillment.
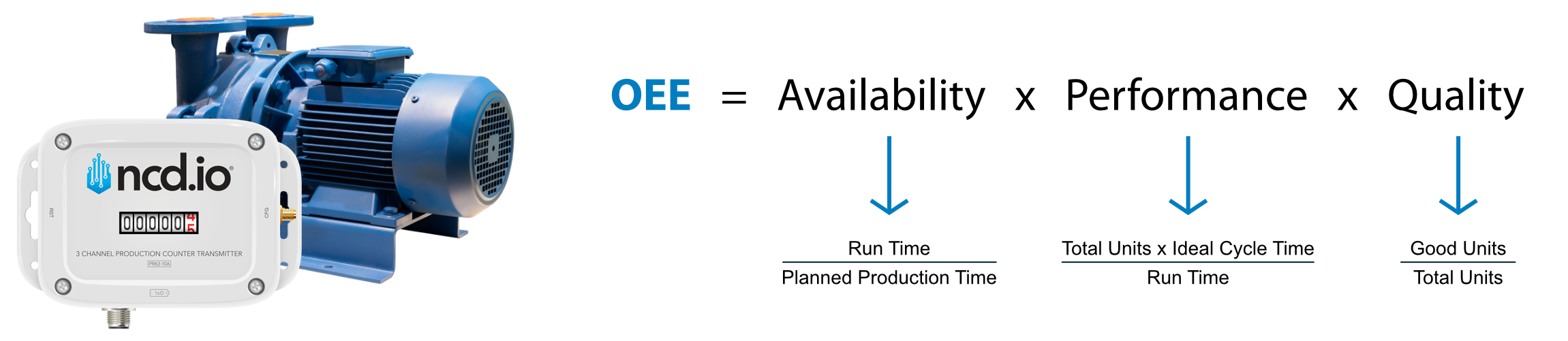
Automated Assembly Line Counting
A manufacturing facility uses the device to count the number of parts that pass through different stages of an automated assembly line. Each of the 3 input channels connects to photo eye sensors positioned at key points along the line, allowing operators to monitor throughput, detect bottlenecks, and calculate overall equipment effectiveness (OEE).
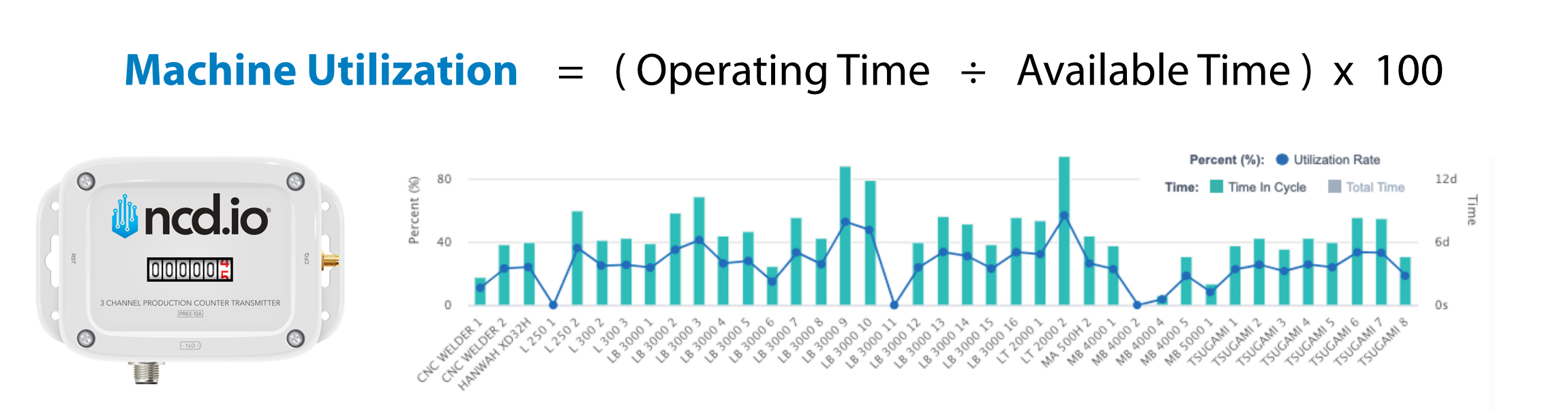
Packaging Line Output Monitoring
In a food or beverage packaging plant, the Production Counter tracks the number of packages sealed, labeled, and boxed. Break beam sensors at each stage provide individual counts, enabling the plant to compare production rates across multiple shifts and ensure daily output targets are met.
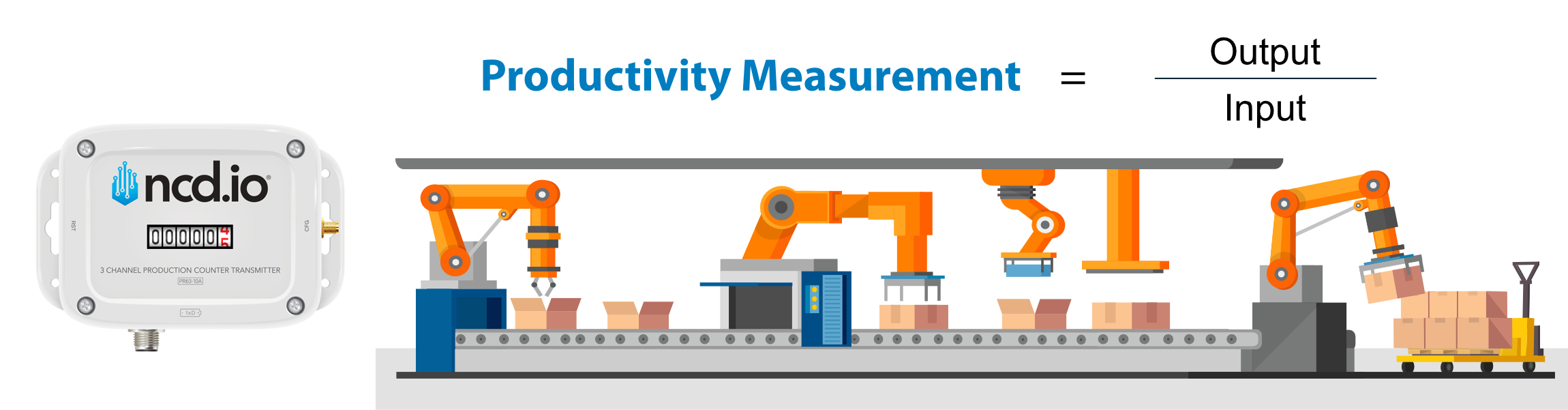