Device Overview
Introducing NCD’s Long Range Industrial IoT Wireless 3 Channel AC Current Sensor, boasting up to a 2 Mile range using a wireless mesh networking architecture. This 3 Channel Industrial IoT Wireless AC Current Monitor Sensor transmitter works together with three split core current sensors (included). It samples current at a high data rate and calculates the RMS Current value and sends a wireless transmission. This process is repeated at user defined timing interval while sleeping in between to minimize power consumption. The sensor comes with three 1.25 meter long split core current sensors which makes installation easy.
This 3 Channel Industrial IoT Wireless AC Current Monitor Sensor is capable of detecting change in current at user defined detection time intervals and sending out data if the current change is greater than user defined detection change percentage. This change detection feature can be enabled or disabled as needed. To minimize power consumption, the current sensor sleeps to preserve battery life. Both of these features work together to support multiple application areas in one package.
Features
- Industrial Grade Wireless 3-Channel Current Monitor
- AC Current Range 0-100/200/600/1000A RMS Measurement (depending on the chosen probe)
- Auto Time Delay Based Data Sample Transmission
- Current Change Detection and Transmission
- Ideal for 3-Phase Motor Current Monitoring
- Configurable Current Sensor Calibration Over Wireless
- Wall-Mounted or Magnet Mounted IP65 Rated Enclosure
- Up to 2 Mile Line-of-Sight Range with On-Board Antenna
- Wireless Mesh Networking using DigiMesh®
- Open Communication Protocol for Easy Software Integration
- Fully configurable via Node-RED
- Power-Efficient Sleep Mode, Up to 10 Year Battery Life
- User Configurable Sleep Duration
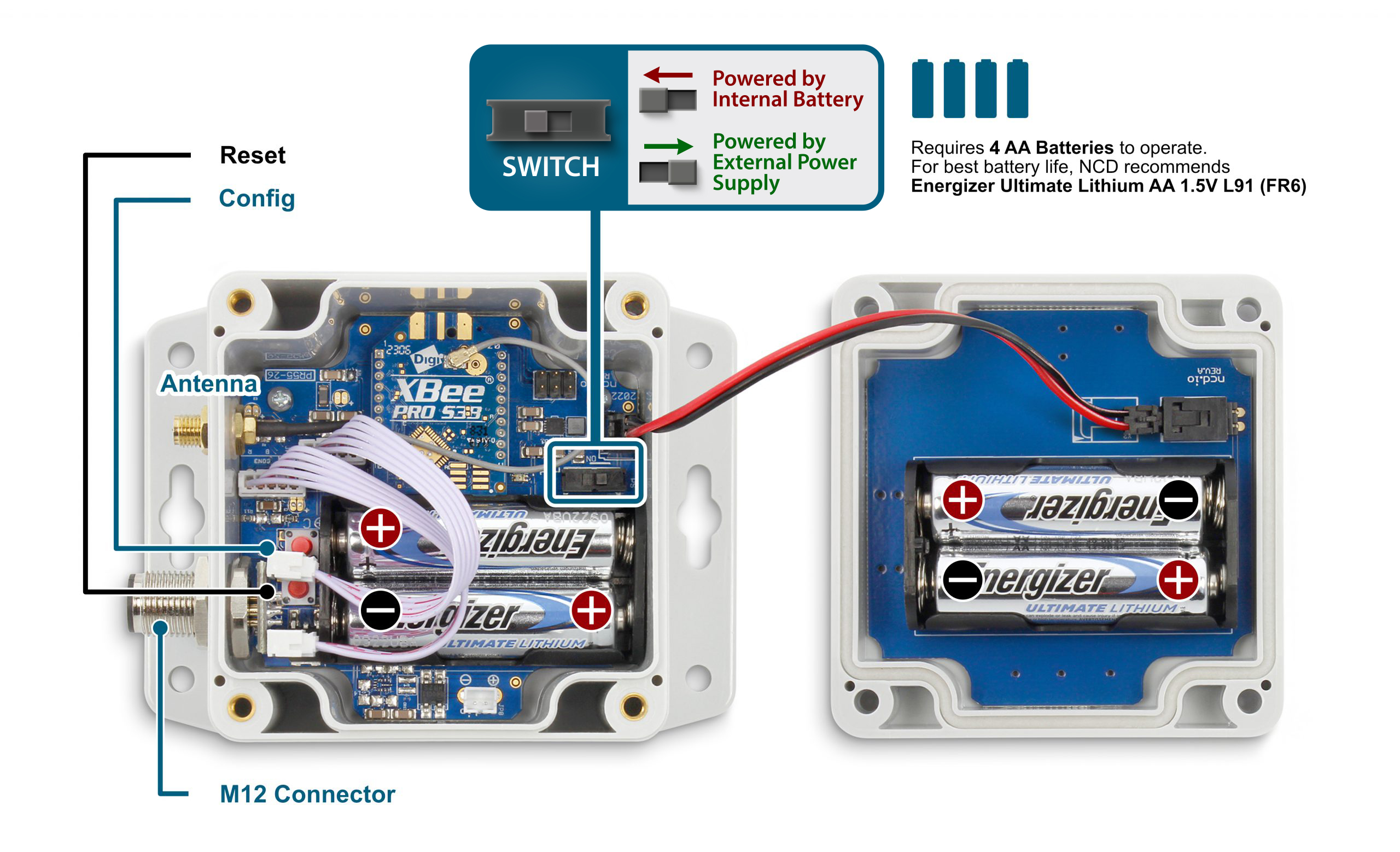
Wireless Technology
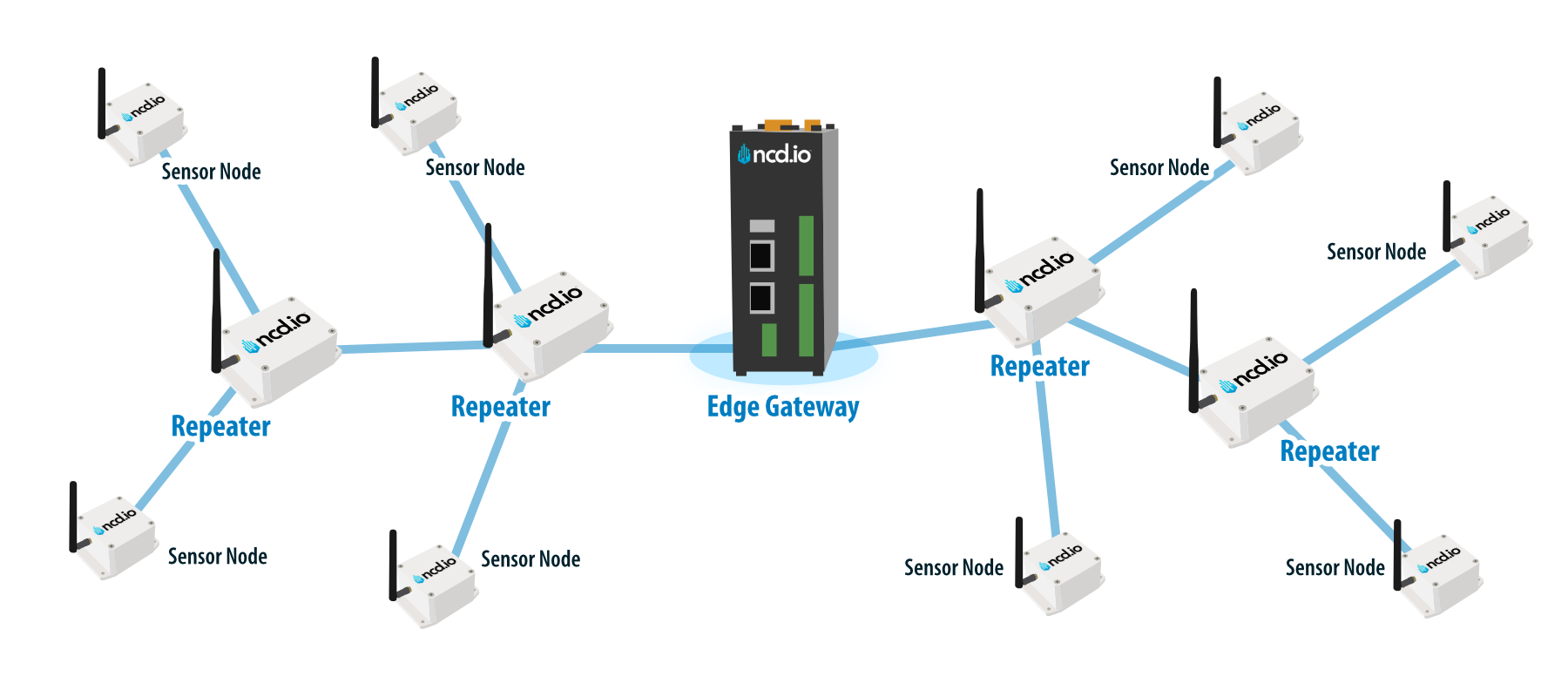
The NCD Industrial range of sensors utilizes DigiMesh, a proprietary networking technology designed by Digi® International. It is especially suitable for IIoT applications as it provides a number of benefits over conventional wireless stacks:
- Long range – up to 1200 feet in urban environments and 2 miles+ in open areas with the included antennas
- Mesh networking topology – no single point of failure, self healing network with high redundancy.
- Long battery life due to low power consumption – up to 10 years
- Simplified provisioning – extending the mesh network via repeater at no additional configuration complexity
- Works in the 868MHz, 900MHz and 2.4GHz bands – worldwide region interoperability.
If you want to learn more about DigiMesh and how it compares with another popular IoT stack (LoRaWAN) head to the article below:
IoT Wireless Sensor Networks: Digi®Mesh vs LoRaWAN®
Battery Life
Specifications | Minimum | Nominal | Maximum | Notes |
---|---|---|---|---|
Batteries | 2 | 4 | 4 | May be Powered by 2 or 4 AA Batteries |
Battery Life 6 TPD (TPD Transmissions per Day) | 8 Years | Battery estimation is based on a 30 min interval | ||
Battery Life 12 TPD (TPD Transmissions per Day) | 5 Years | Battery estimation is based on a 30 min interval | ||
Battery Life 24 TPD (TPD Transmissions per Day) | 3 Year | Battery estimation is based on a 30 min interval |
The Truth About Battery Life
Under the best of circumstances, the best non-rechargeable batteries commonly available today are limited to a 10 year non-working shelf life in a room temperature environment. Factors such as actual usage, temperature, and humidity will impact the working life. Be wary of any battery claims in excess of 10 years, as this would only apply to the most exotic and expensive batteries that are not commonly available. Also note that most battery chemistries are not rated for use in extreme temperatures. NCD only uses the best Non-Rechargeable Lithium batteries available today, which are also rated for use in extreme temperatures and have been tested by our customers in light radioactive environments. Lithium batteries offer a 10 year maximum expected shelf life due to limitations of battery technology. NCD will never rate sensor life beyond the rated shelf life of the best batteries available today, which is currently 10 years.
Applications & Use-cases
This sensor is a versatile that can measure AC currents up to 1000A RMS, making it suitable for heavy industrial applications. Additionally, its change detection capabilities make it suitable for predictive maintenance scenarios. This, coupled with robust wireless communication and a durable enclosure, makes it an ideal choice for diverse environments and challenging operational conditions, where real time monitoring with a high grade or reliability is required.
3 Channel AC Current Monitor Applications
Real-Time Power Consumption Analysis
The sensor can be used in industrial and commercial settings to provide real-time monitoring and analysis of power consumption across multiple electrical devices or systems. By deploying the sensor on key electrical circuits, facility managers can gain insights into energy usage patterns, identify areas where energy is being wasted, and implement strategies to reduce overall consumption. This application is particularly valuable in energy-intensive industries where managing and reducing energy costs is a critical priority.
Predictive Maintenance for Electrical Equipment
The sensor can be integrated into a predictive maintenance program to monitor the health of critical electrical equipment such as motors, pumps, compressors, and HVAC systems. By continuously tracking the AC current drawn by these devices, the sensor can detect early signs of electrical or mechanical issues, such as increased current draw due to bearing wear or insulation breakdown. This application allows maintenance teams to schedule repairs before a failure occurs, reducing downtime and extending the lifespan of the equipment.
Load Monitoring and Management in Industrial Facilities
The sensor can be used to monitor and manage electrical loads in industrial facilities where multiple high-power devices operate simultaneously. By installing the sensor on the power lines of different machines or production lines, facility managers can ensure that electrical loads are balanced and do not exceed the capacity of the electrical infrastructure. This application helps prevent overloading, reduces the risk of power outages, and optimizes the distribution of electrical power across the facility.
Energy Auditing and Compliance Reporting
The sensor can be employed as part of an energy auditing process to provide accurate data on the energy consumption of different systems within a building or industrial facility. This data can be used to generate reports for regulatory compliance, environmental certifications, or internal sustainability initiatives. The ability to monitor and record current usage across multiple channels makes this application ideal for organizations looking to improve their energy efficiency, reduce their carbon footprint, and meet regulatory requirements.
3 Channel AC Current Monitor Use-cases
Energy Consumption Monitoring in a Manufacturing Plant
In a manufacturing facility, the sensor is installed on the main power lines feeding critical machines such as CNC machines, assembly lines, and large motors. By monitoring the AC current in real-time across these machines, the facility managers can track energy consumption patterns, identify peak usage periods, and detect inefficiencies. This data helps in optimizing energy usage, reducing operational costs, and ensuring that the machinery operates within its specified power range, preventing potential overloading and extending the life of the equipment.
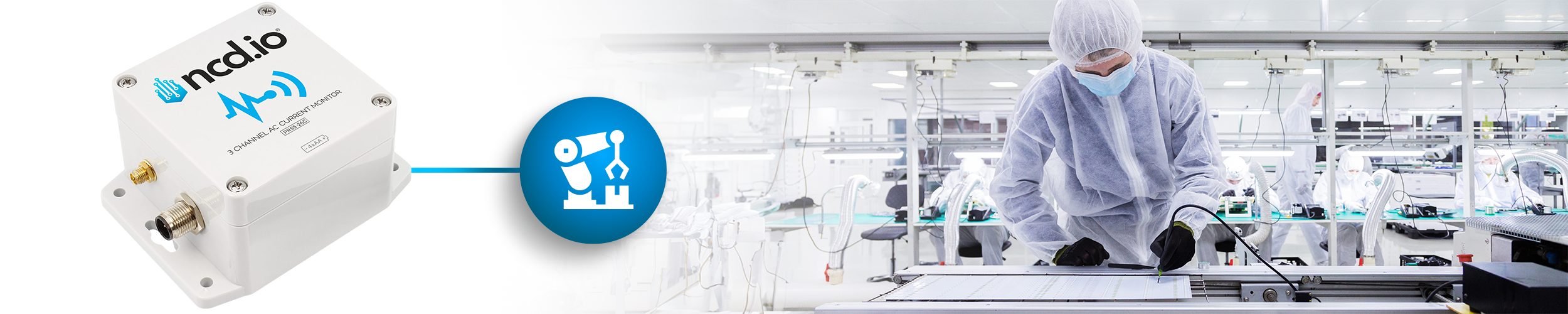
Preventive Maintenance in HVAC Systems
The sensor is used to monitor the current draw of the compressors, fans, and pumps in an industrial HVAC system. By continuously tracking the current across these components, the sensor can detect anomalies such as increased current draw, which may indicate issues like motor wear, bearing failure, or refrigerant leaks. Early detection of these issues allows maintenance teams to perform targeted interventions before a complete system failure occurs, thereby reducing downtime and maintenance costs while ensuring the HVAC system operates efficiently.
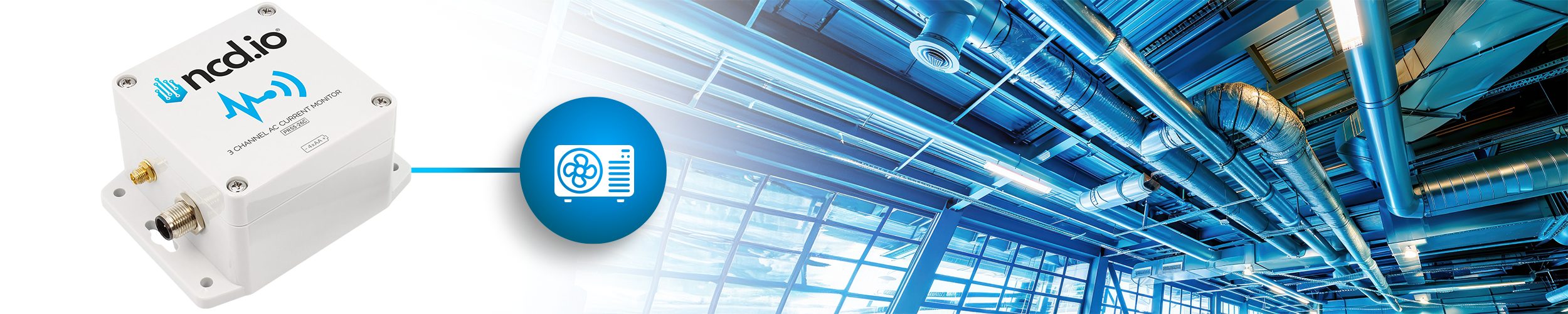
Electrical Load Balancing in a Data Center
In a data center, the sensor is deployed to monitor the AC current on the power lines feeding server racks. Data centers require precise load balancing to ensure that no single circuit is overloaded, which can lead to power outages or equipment damage. By using the sensor to monitor current levels across multiple racks, data center operators can distribute the electrical load more evenly, prevent overloading, and ensure a stable power supply to critical IT infrastructure. This also helps in planning for future expansions by providing accurate data on current electrical loads.
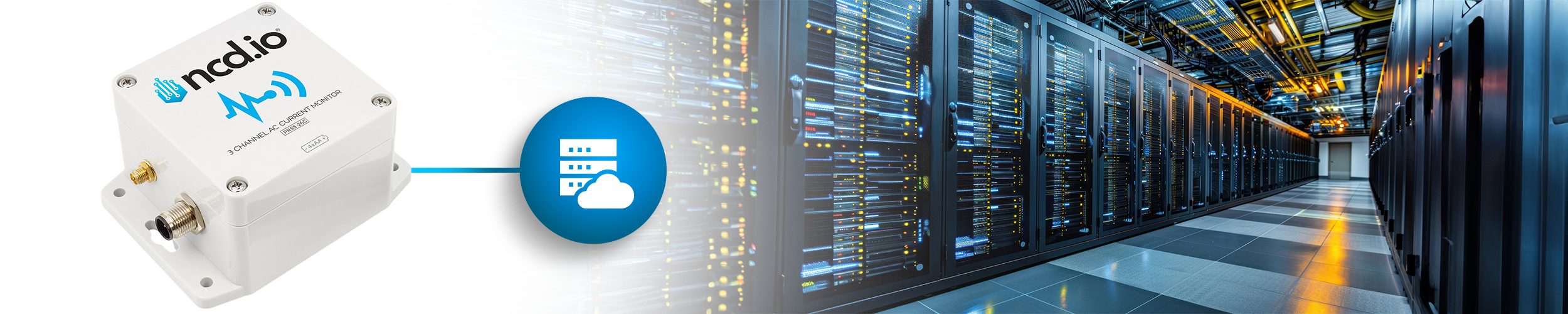
Monitoring Solar Power Systems in Commercial Buildings
the sensor is installed on the AC output lines of inverters in a commercial solar power installation. By monitoring the current produced by the solar inverters, building managers can track the performance of the solar panels in real-time. Any significant drop in current could indicate issues such as panel shading, dirt accumulation, or inverter malfunction. With this data, operators can schedule maintenance to optimize energy production, ensure the solar system is operating at peak efficiency, and maximize the return on investment from the solar installation.
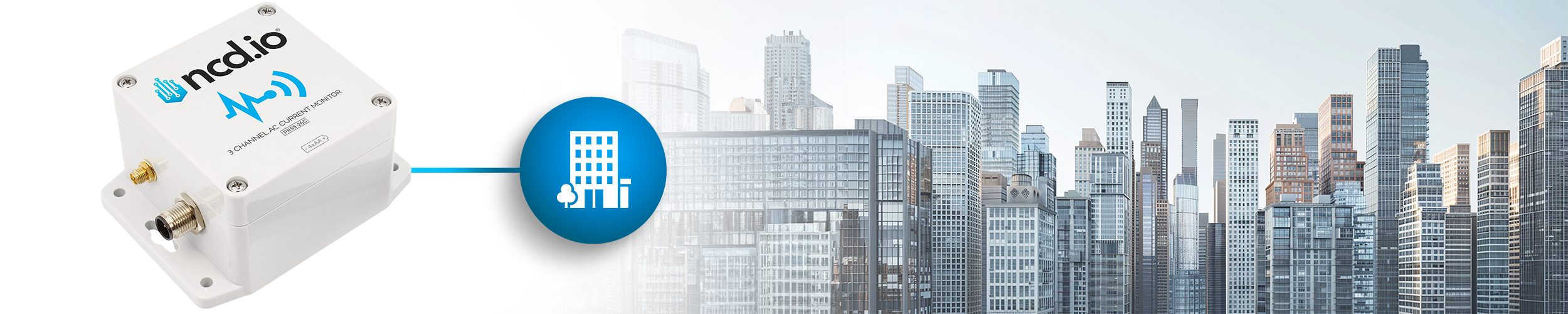