Device Overview
The Industrial IoT Ultrasound Vibration Sensor from NCD – a high-performance solution engineered explicitly for industry-leading predictive maintenance applications. Integrated with a wireless mesh networking architecture, it delivers an impressive range of up to 2 miles. The sensor employs a high-precision, dual-channel 15-bit ADC, capturing vibration data at user-specified intervals and wirelessly transmitting the recorded data to remote modems and gateways.
Designed with a focus on energy efficiency, the sensor seamlessly transitions into an ultra-low power sleep mode between data sampling periods. Its integrated 16V buck-boost power supply negates the requirement for an external power source, enhancing its versatility.
Powering the sensor are six AA batteries that, coupled with an operational capacity of up to 500,000 wireless transmissions, afford an estimated battery lifespan of 10 years. This lifespan depends on environmental conditions and the frequency of data transmissions. The sensor also supports optional external power from a 6-18VDC supply for added flexibility.
Its superior range, high precision, extended battery life, cost-effectiveness, and fortified security features position this sensor as an exceptional tool for predictive maintenance tasks in various industrial contexts, exceeding the standards set by traditional devices.
Features
- Industrial Grade 1-Channel Ultrasound Vibration Sensor
- Resonant frequency Fres = 37 [kHz] +/- 1 [kHz]
- Measuring range 20 to 100 [dBµVRMS]
- Resolution 0.5 [dB𝜇𝑉RMS]
- Ideal For Motors, Pumps, and Gear Box Predictive Maintenance
- 2 Mile Line-of-Sight Range with On-Board Antenna
- Superior LOS Range of up to 28 Miles with High-Gain Antennas
- Wireless Mesh Networking using DigiMesh®
- Open Communication Protocol for Easy Software Integration
- Validates and Retries Lost Communication Packets
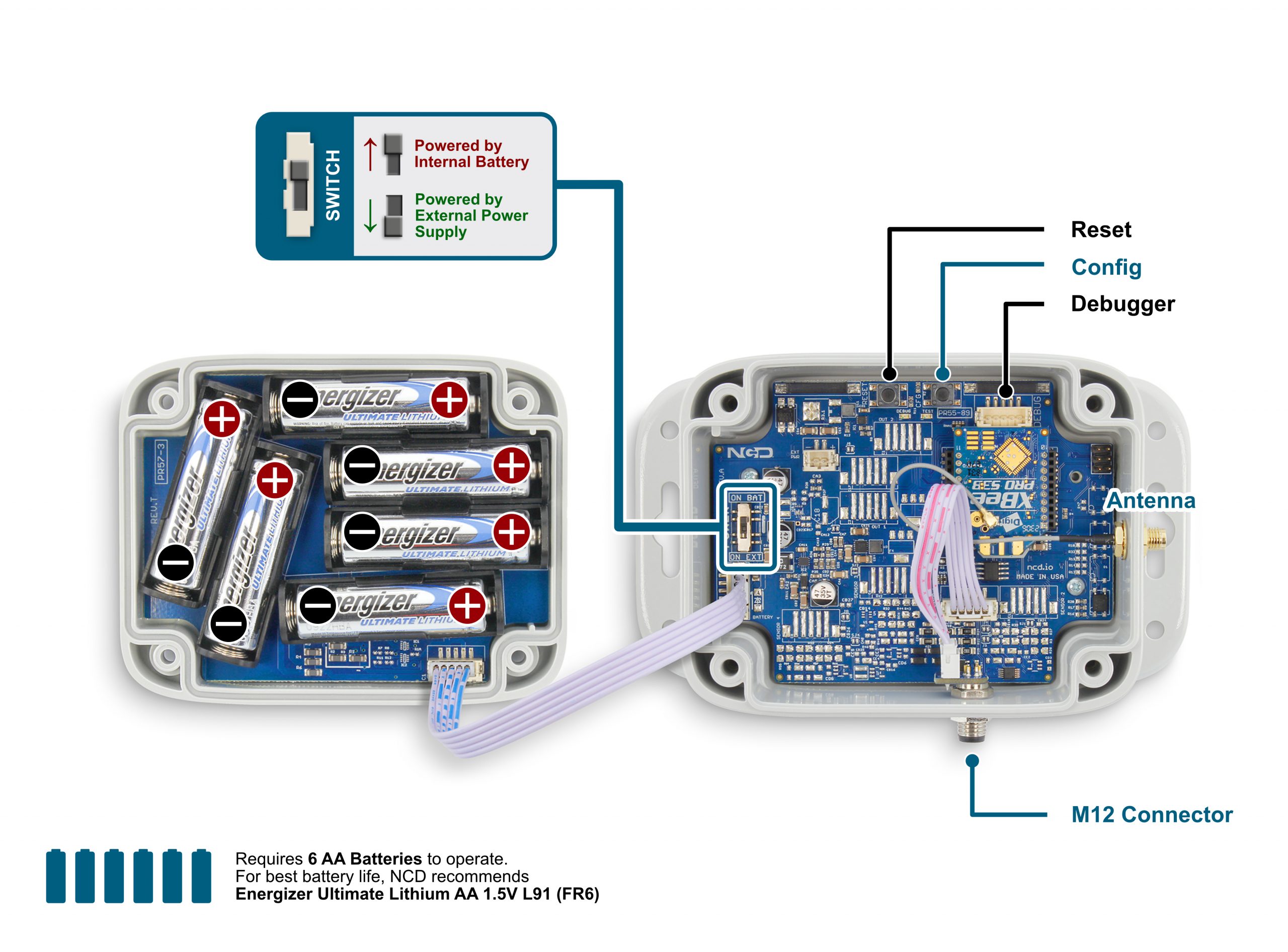
Wireless Technology
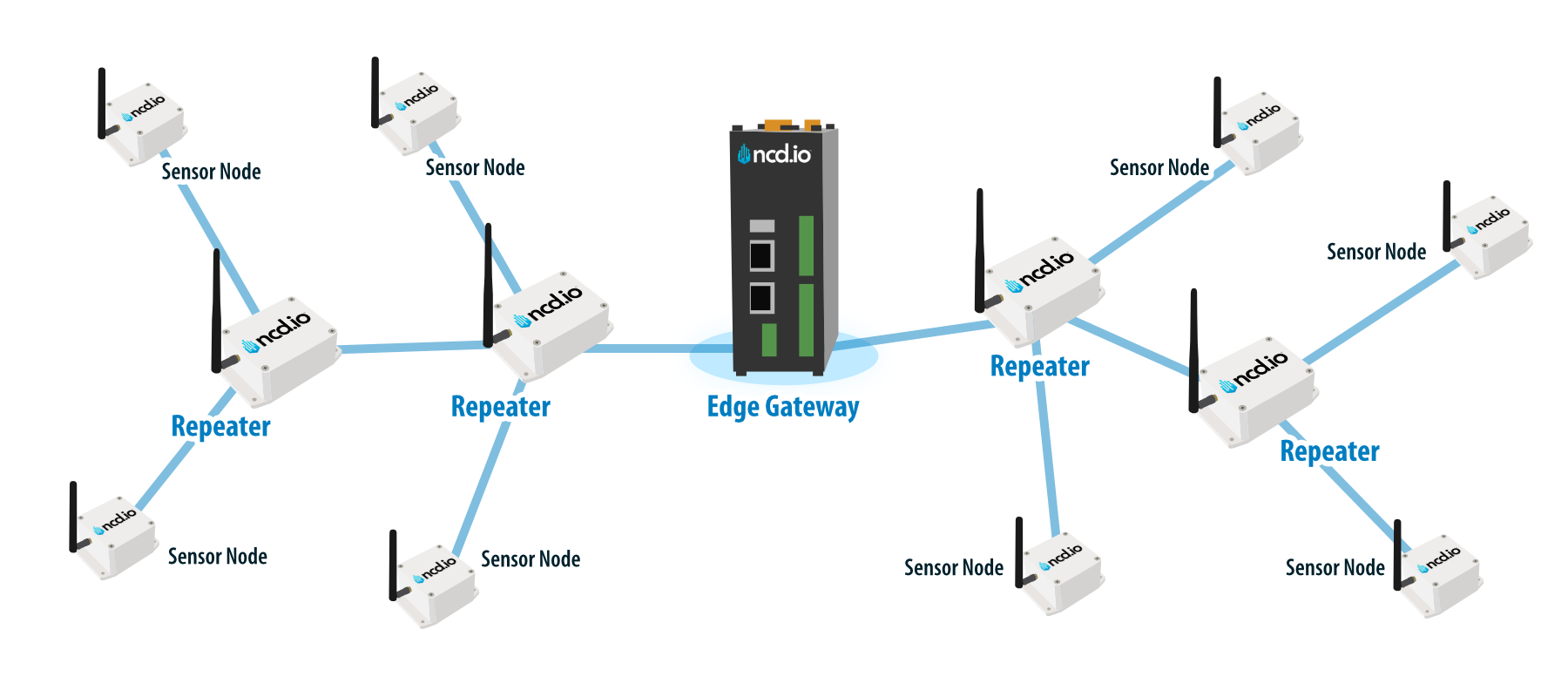
The NCD Industrial range of sensors utilizes DigiMesh, a proprietary networking technology designed by Digi® International. It is especially suitable for IIoT applications as it provides a number of benefits over conventional wireless stacks:
- Long range – estimated 1000 feet in urban environments and 2 miles+ in open areas with the included antennas
- Mesh networking topology – no single point of failure, self healing network with high redundancy.
- Long battery life due to low power consumption – up to 10 years
- Simplified provisioning – extending the mesh network via repeater with no additional configuration complexity
- Works in the 868MHz, 900MHz and 2.4GHz bands – worldwide region interoperability.
If you want to learn more about DigiMesh and how it compares with another popular IoT stack (LoRaWAN) head to the article below:
IoT Wireless Sensor Networks: Digi®Mesh vs LoRaWAN®
Battery Life
The battery life is also influenced by the boot time and power consumption of the external sensor.
Specifications | Minimum | Nominal | Maximum | Notes |
---|---|---|---|---|
Batteries | 2 | 6 | 6 | May be Powered by 2 or 4 AA Batteries |
Battery Life 1 TPD (Transmissions per Day) | 10 Years | Estimation is based on a 30 minute interval | ||
Battery Life 12 TPD (Transmissions per Day) | 8 Years | Estimation is based on a 30 minute interval | ||
Battery Life 24 TPD (Transmissions per Day) | 5 Year | Estimation is based on a 30 minute interval | ||
Battery Life 96 TPD (Transmissions per Day) | 3 Year | Estimation is based on a 30 minute interval |
The Truth About Battery Life
Under the best of circumstances, the best non-rechargeable batteries commonly available today are limited to a 10 year non-working shelf life in a room temperature environment. Factors such as actual usage, temperature, and humidity will impact the working life. Be wary of any battery claims in excess of 10 years, as this would only apply to the most exotic and expensive batteries that are not commonly available. Also note that most battery chemistries are not rated for use in extreme temperatures. NCD only uses the best Non-Rechargeable Lithium batteries available today, which are also rated for use in extreme temperatures and have been tested by our customers in light radioactive environments. Lithium batteries offer a 10 year maximum expected shelf life due to limitations of battery technology. NCD will never rate sensor life beyond the rated shelf life of the best batteries available today, which is currently 10 years.
Wireless Ultrasound Vibration Sensor Use-cases
Predictive Maintenance
- Application: Monitoring the vibration patterns of critical machinery (e.g., motors, pumps, compressors) to detect anomalies that could indicate wear and tear or impending failure.
- Benefit: By identifying issues before they lead to breakdowns, companies can reduce downtime and maintenance costs, ensuring continuous operation.
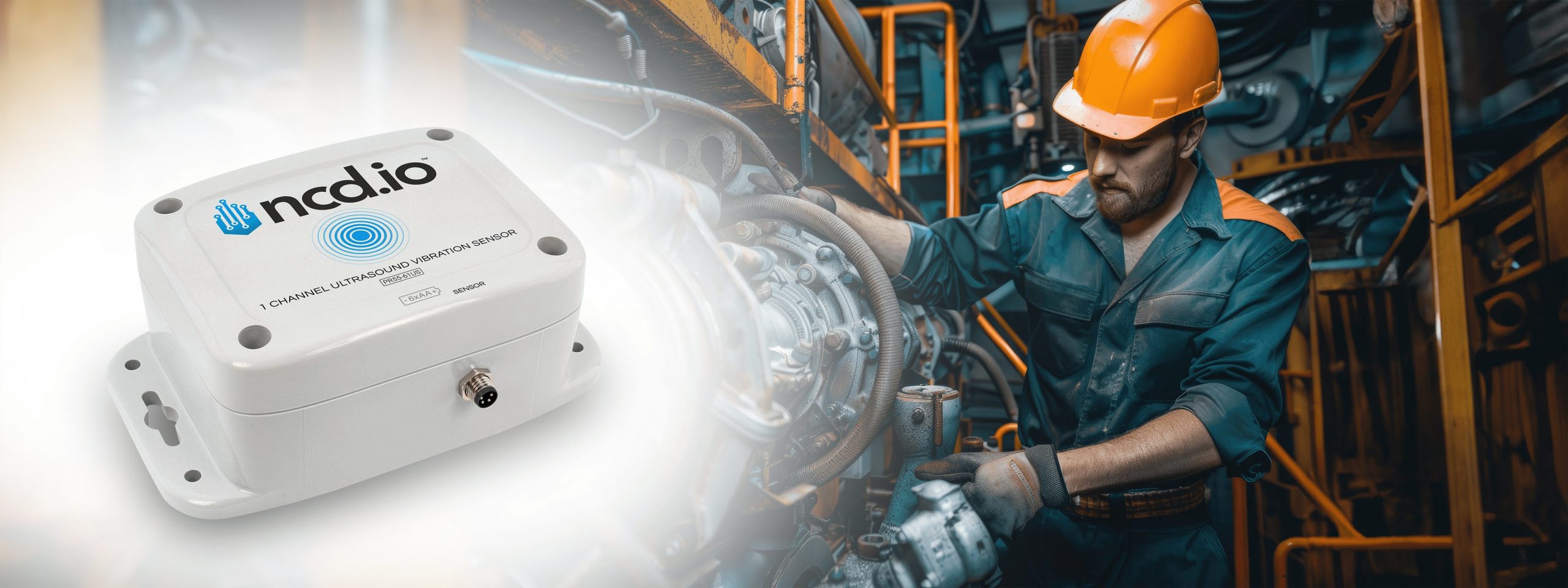
Rotating Equipment Monitoring
- Application: Continuously monitoring the condition of rotating equipment like fans, turbines, and gearboxes. Ultrasound sensors can detect changes in vibration that might indicate imbalances, misalignment, or bearing failures.
- Benefit: Helps in early detection of potential mechanical issues, thus preventing catastrophic failures.
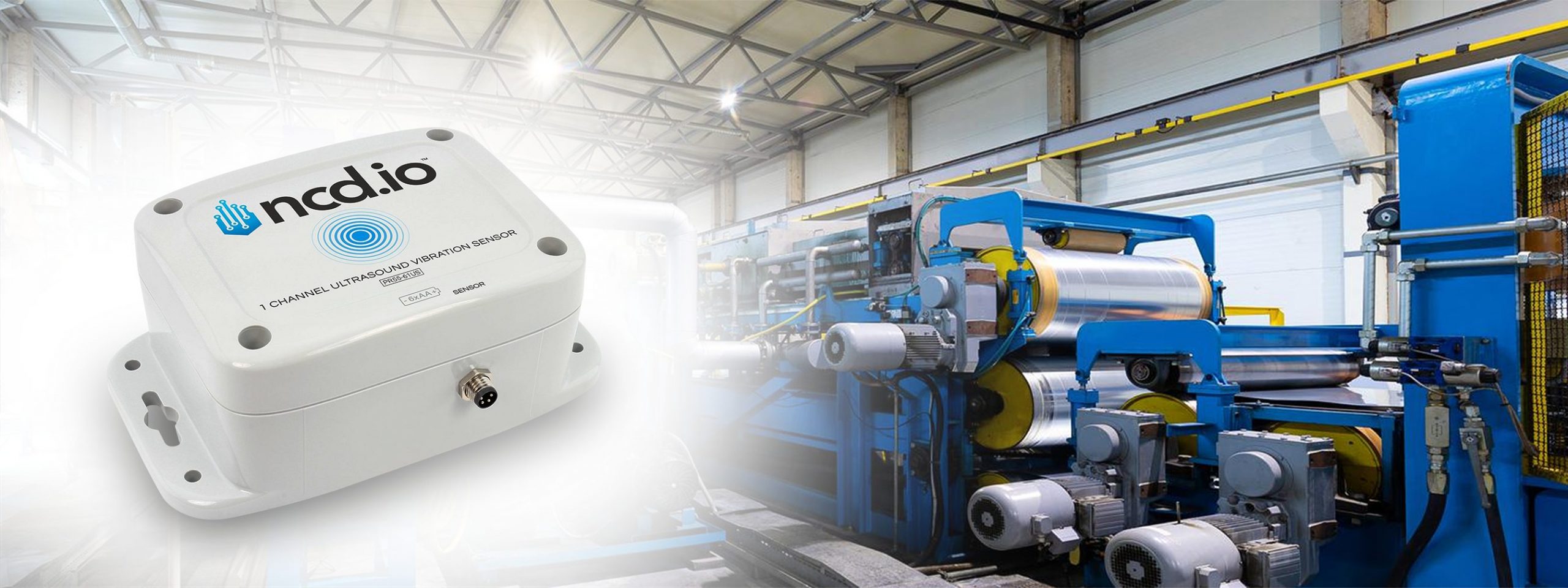
Pipeline and Fluid Flow Monitoring
- Application: Detecting cavitation or flow disruptions in pipelines by monitoring vibration levels. Sudden changes in vibration could indicate blockages, leaks, or other flow issues.
- Benefit: Ensures the smooth operation of fluid transport systems, minimizing losses and maintaining efficiency.
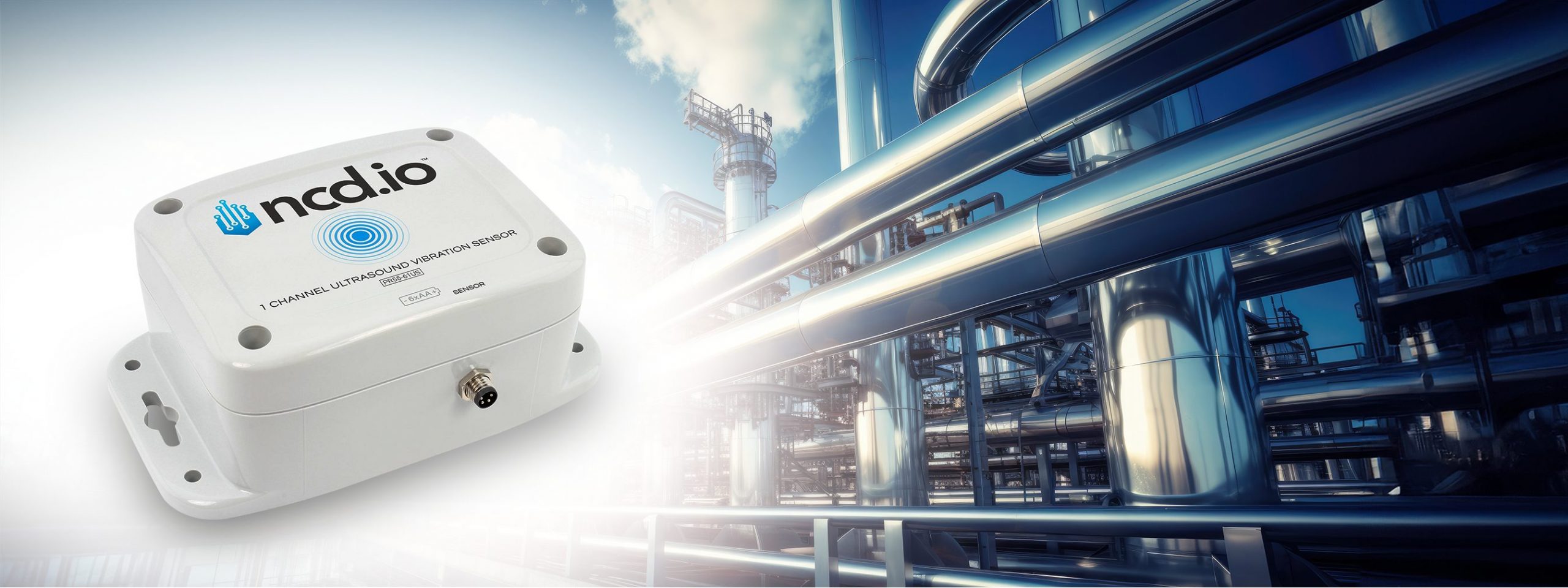
Building and Infrastructure Health Monitoring
- Application: Monitoring the structural integrity of buildings, bridges, and other infrastructure. Vibrations can indicate shifts or damage in the structure that require attention.
- Benefit: Enhances safety by providing real-time alerts on potential structural issues, allowing for timely repairs.
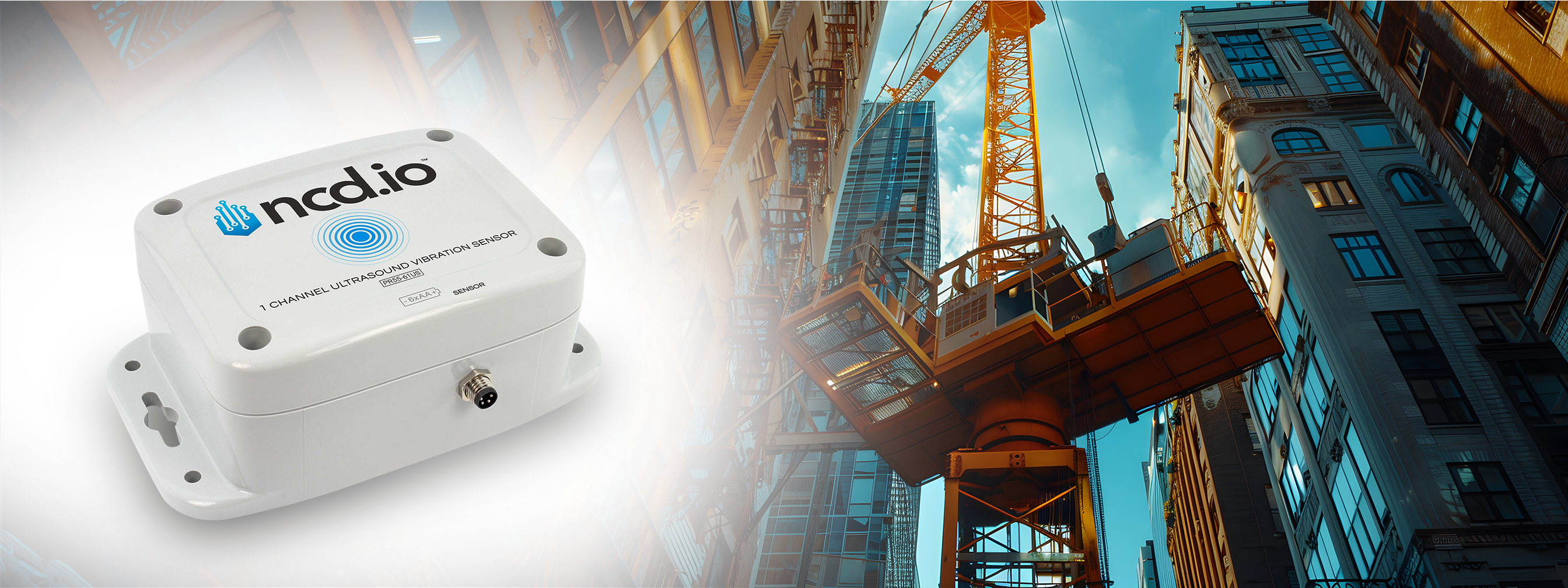
Applications & Use-cases
The sensor offers unprecedented insights into equipment health monitoring, it is perfect for predictive maintenance and condition monitoring. This coupled with its robust wireless communication and a durable enclosure, makes it an ideal choice for diverse environments and challenging operational conditions.
Wireless Ultrasound Vibration Sensor Applications
Rotating Machinery Health Monitoring
The sensor is ideal for continuously monitoring the health of rotating machinery such as motors, pumps, fans, and turbines. By capturing real-time vibration data, it can detect subtle changes in the machinery’s operating conditions that may indicate early signs of mechanical issues. For instance, the sensor can identify bearing wear, shaft misalignment, or imbalances in the rotor, all of which are common precursors to more severe equipment failures. By addressing these issues early, facilities can avoid costly unplanned downtime, extend the lifespan of their machinery, and improve overall operational efficiency.
Gearbox Condition Monitoring
Gearboxes are critical components in many industrial systems, and their failure can lead to significant operational disruptions. The sensor can detect variations in vibration patterns that often signify problems within the gearbox, such as gear wear, misalignment, or insufficient lubrication. By continuously monitoring these vibration signals, the sensor can provide early warnings of potential gearbox failures. This allows maintenance teams to schedule repairs or replacements during planned maintenance windows, reducing the risk of unexpected breakdowns and ensuring the smooth operation of the entire system.
Conveyor System Monitoring
Conveyor systems are vital for the efficient movement of materials in various industrial settings, such as manufacturing plants, mining operations, and distribution centers. The sensor can be deployed to monitor the condition of key components in these systems, including rollers, bearings, and drive mechanisms. By analyzing the vibration data, the sensor can predict when these components are likely to fail, enabling proactive maintenance. This helps prevent costly interruptions in the production process and ensures that the conveyor system operates reliably and efficiently, minimizing the risk of production bottlenecks.
HVAC System Monitoring
Heating, Ventilation, and Air Conditioning (HVAC) systems are crucial for maintaining comfortable and safe environments in buildings, whether they are commercial, residential, or industrial. The sensor can be used to monitor the condition of rotating components within HVAC systems, such as fans and compressors. By detecting abnormal vibrations, the sensor can alert maintenance teams to issues like bearing degradation, belt wear, or imbalances that could lead to inefficient operation or system failure. Early detection of these issues helps maintain optimal indoor air quality, energy efficiency, and system longevity, reducing the likelihood of costly emergency repairs.
Wind Turbine Monitoring
Wind turbines are complex machines with many rotating parts, including the rotor, gearbox, and generator. These components are subject to significant stresses, making them prone to wear and failure over time. The sensor can be installed on these critical components to monitor their vibration levels continuously. By analyzing the vibration data, the sensor can detect early signs of wear, misalignment, or imbalance, allowing operators to schedule maintenance before these issues lead to more severe problems. This predictive maintenance approach not only extends the lifespan of the turbines but also ensures that they operate at peak efficiency, maximizing energy production and reducing the cost of maintenance.