A real-time dashboard for monitoring Machine Health can help business owners and operators keep track of their machines to ensure they are running smoothly. By installing NCD Predictive Maintenance Vibration sensors, you can create a dashboard that sends alerts when it detects a problem with the machine. This will allow you to fix problems before they become bigger issues. Machine health is important to monitor because it can help you avoid costly downtime and repairs. By using a real-time dashboard, you can be proactive about maintaining your machines.
Installing NCD Predictive Maintenance Vibration sensors is easy and they come with instructions. Once the sensors are installed, you will need to create a dashboard. Node-Red is a free and open-source programming tool that can be used to create the dashboard. Node-Red is easy to use and has a wide range of community support. Once you have created the dashboard, you can add Machine Health as a data source. The Machine Health data source will send alerts to the dashboard when it detects a problem with the machine.
The Machine Health data source is just one of many that can be used with Node-Red. By adding other data sources, you can create a dashboard that is tailored to your specific needs. For example, you could add a weather data source to the dashboard. This would allow you to see if the weather is affecting the Machine Health. You could also add a data source for the manufacturer’s recommended maintenance schedule. This would allow you to see if the machine is due for any maintenance.
There are many ways to customize the dashboard to your needs. By adding different data sources, you can create a dashboard that is tailored to your specific needs.
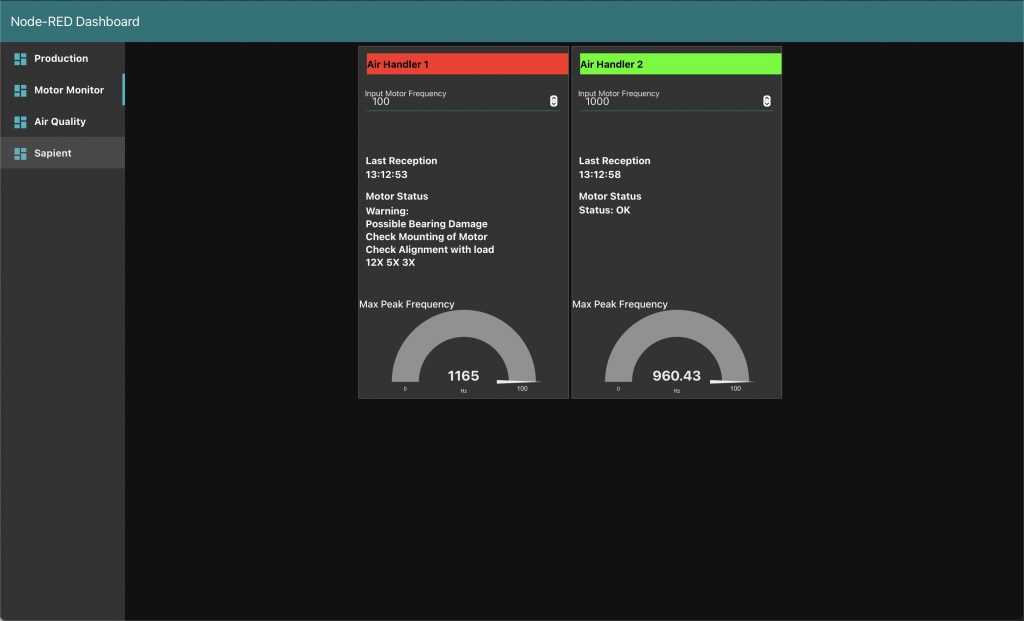
What is Predictive Maintenance
Predictive maintenance is a method of maintaining machines by predicting when maintenance is needed. This is done by monitoring the machine’s health and using that data to create a prediction model. The prediction model can then be used to forecast when the machine will need maintenance. Predictive maintenance can help business owners avoid costly downtime and repairs.
NCD Predictive Maintenance Vibration sensors can be used to monitor the Machine Health. The Machine Health data source will send alerts to the dashboard when it detects a problem with the machine. By using predictive maintenance, you can be proactive about maintaining your machines.
Node-Red-Dashboard
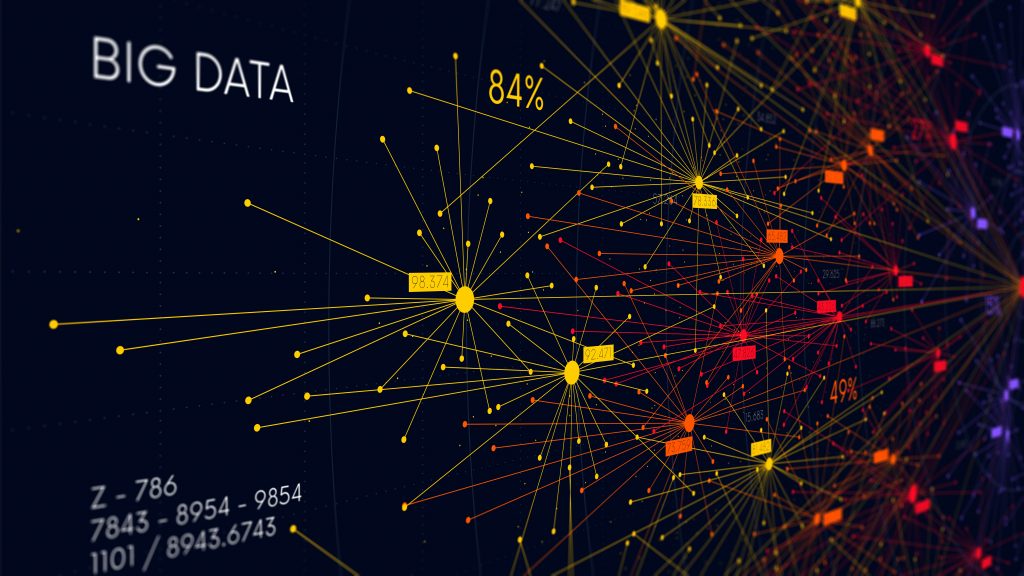
Node-Red-Dashboard is a free and open-source programming tool that can be used to create real-time dashboards for monitoring Machine Health. Node-Red is easy to use and has a wide range of community support. It can be used to create dashboards that are tailored to your specific needs.
NCD Predictive Maintenance Vibration Sensors
Machine health is an important aspect of running a business. By monitoring machine health through vibration, you can avoid costly downtime and repairs.
NCD Predictive Maintenance Vibration Sensors make it easy to monitor machine health through a real-time dashboard. The Vibration sensors stream data to Node-Red which can be parsed and displayed as user readable information on the dashboard.
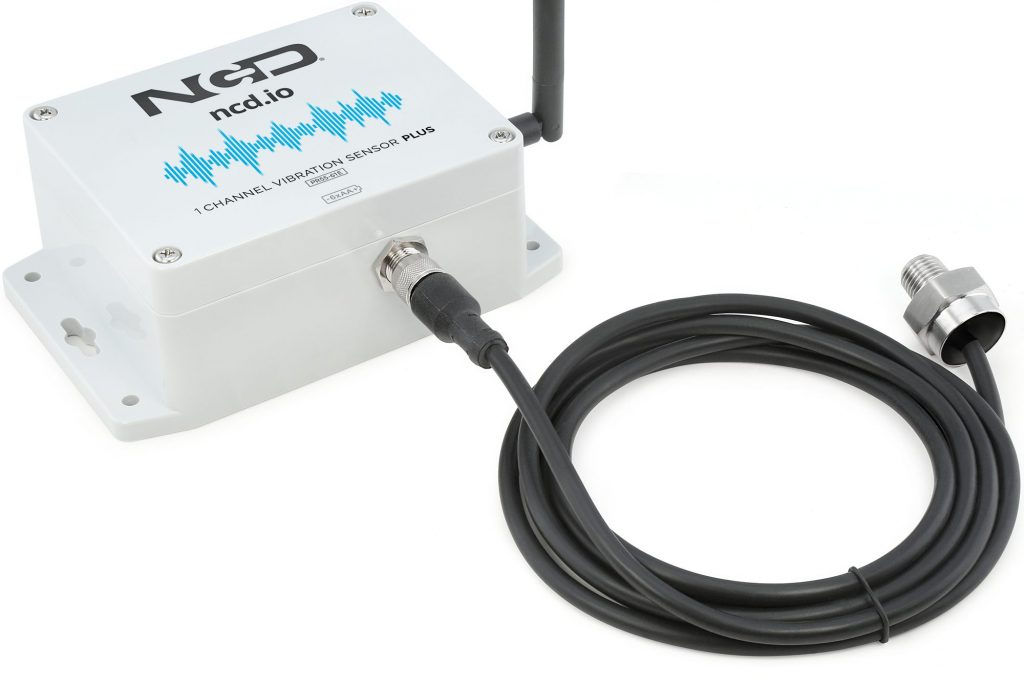
Computing Device
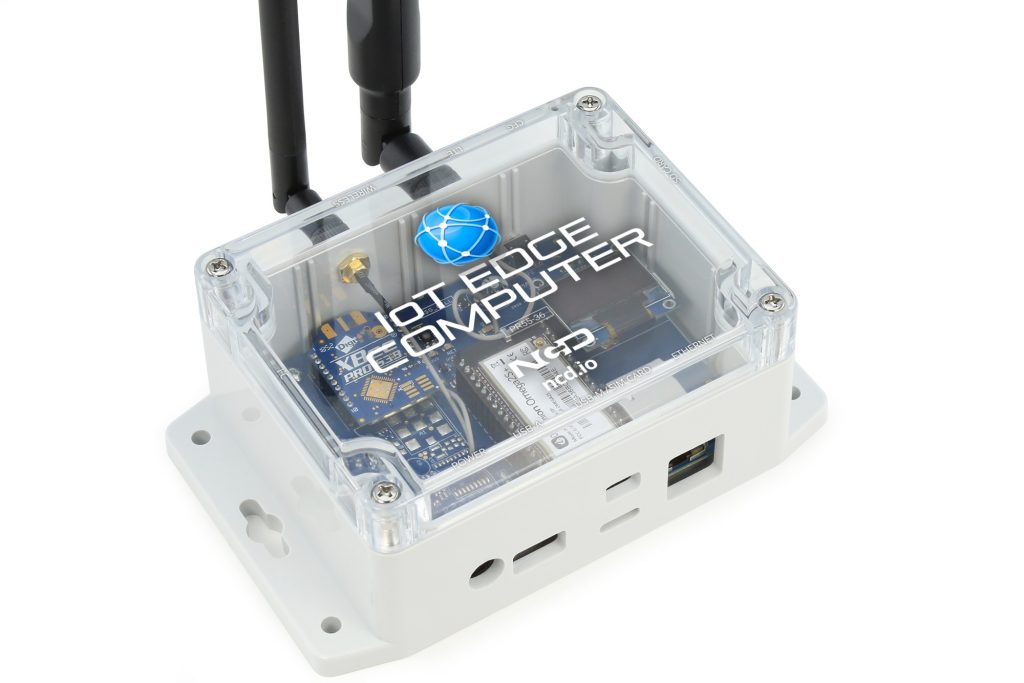
It is possible to use a regular Windows, Linux, or Mac computer as the dashboard/sensor server. This can get as complex as you wish, however it is recommended that you use NCD’s IoT Edge Computer which comes with Node-Red, Node-Red-Dashboard, and NCD’s ncd-red-wireless libraries pre installed so all you need to do is plug it into your Local Area Network, and then power up the sensors within range of the IoT Edge Computer.
If you plan to install Node-Red on another computer then you will need to check out some documentation on installing Node-Red on your specific Operating System. Once Node-Red is installed you will need to install node-red-dashboard and ncd-red-wireless into Node Red using the pallet manager in the Node-Red web UI editor. Lastly you will need a modem connected to the computer which will allow the computer to receive telemetry from NCD sensors.
Flow for a simple Real Time Dashboard in Node-Red tailored for Predictive Maintenance Work
Here we have created a simple node-red flow that works with a couple of NCD Vibration sensors. View on GitHub:
https://github.com/ncd-io/node-red-flow-real-time-vibration-dashboard
Flow walkthrough
- Wireless Gateway node. All data from all NCD sensors in range of this modem/iot edge computer will stream out of this node.
- Check Address. This node checks the address this sensor data originated from. This is how we distinguish which sensor sent the data and thus how we wish to display the data on the dashboard.
- Evaluate Readings. This function node evaluates the readings from the sensor against ISO20816-1:6016 standards for motor health based on the user input motor frequency. Through this function we determine if the motor is operating normally or if there is an issue, and if there is an issue what the likely issue(s) are.
- AH1 Max Frequency. This is a dashboard gauge that will display the highest frequency peaks in all three axis. In a normal operational motor this is a good estimate of the actual run speed of the motor.
- AH1 Status Text. This is a dashboard text widget which displays the status of the motor. If the motor is running normally it will be Status: OK. If there is an issue then the possible failures will be displayed here along with the run time multipliers for user diagnostics.
- AH1 Set Red/Green. For quick reference every motor Widget Group has a title bar at the top with the name of the motor. This node sets the background color of that title bar to Green If the motor is operating normally, or red if there is an issue with the motor. This makes is simple to quickly glance at the dashboard to determine if there are any issues.
- AH1 User Frequency Input. This node outputs the Motor Frequency input by the user. In order to determine possible issues with the motor it is required that we know the estimated speed of the motor. The user simply inputs the speed of the motor in Hz and then it is output by this node.
- Set AH1 Motor Frequency Variable. This node takes the output from the AH1 User Frequency Input Node and stores that to a variable which can be referenced inside the Evaluate Readings function node in order to determine the status of the motor.
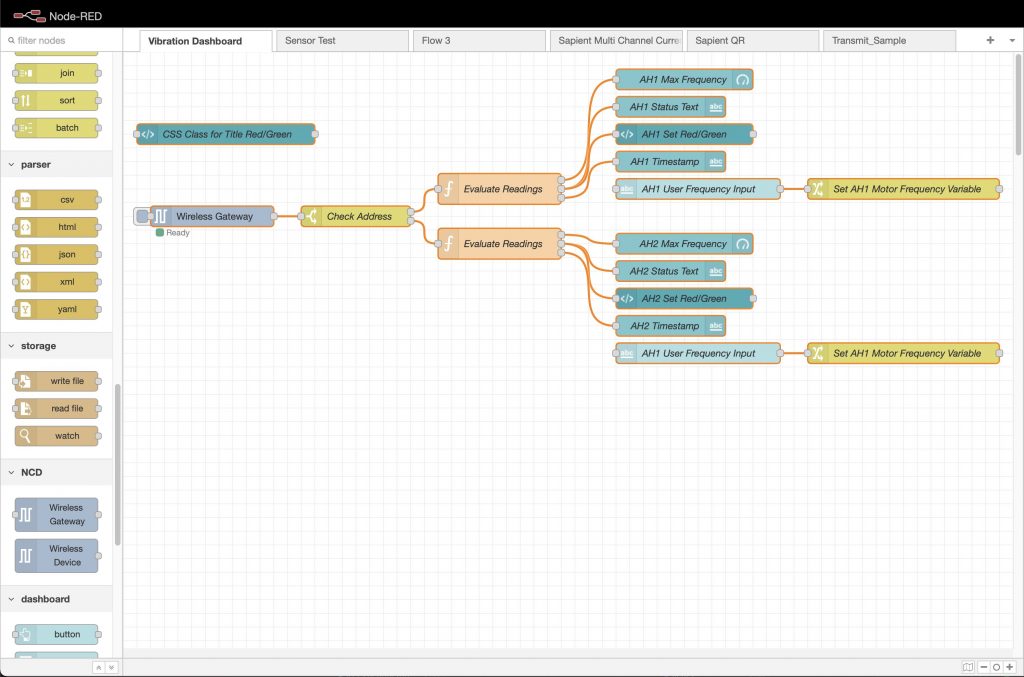
What is ISO20816-1:2016?
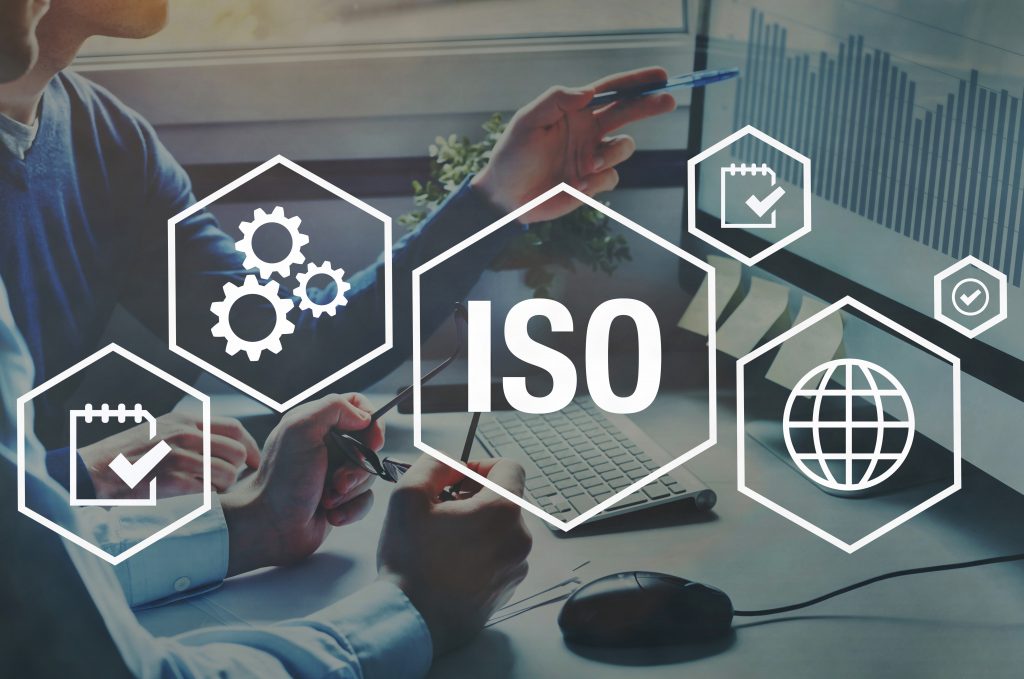
ISO 20816-1:2016(E) defines a procedure for the evaluation of condition indicators to diagnose the health status and remaining useful life of rotating electrical machines. The method described is primarily applicable to induction motors, synchronous motors and generators in the range 1 kw to 100 MW.
The standard provides the user with a consistent approach to the assessment of the health status of a machine, with the aim of reducing unplanned downtime.
In this standard is an outline which makes it possible to estimate the possible fault of a motor based on the frequencies of the peak accelerations in X,Y, and Z axis. These peaks are divided by the estimated speed frequency of the motor. For instance if there are X axis Peaks at 900 Hz but the run speed of the motor is 100Hz that would be a 9x peak frequency which would indicate a possible bad bearing. These frequency peak multipliers are:
- 1X — Normal ( if the peak is at 1 times of motor running frequency)
- 1X — if increase over time — unbalance
- 1X,2X,3X — 2X max — Misalignment
- 1X,2X,3X,4X,5X — Looseness
- 3X,6X,9X,12X — Bearing
- 1X — period will increase — resonance
Given this information our Evaluate Readings function node can estimate what may be at fault in the motor/assembly and notify staff what should be evaluated in diagnostics. This drastically simplifies the monitoring of motors via Vibration analysis.
Predictive Maintenance Program to reduce Maintenance Costs
Predictive maintenance systems are computer-aided systems that use historical data to predict when a machine component is likely to fail. This allows companies to schedule repairs and replacements before an actual failure occurs, preventing unexpected downtime and saving money.
Conventional time based maintenance schedules are typically based on time or usage intervals based on asset history. For example, a machine might be serviced every six months or after it has been used for 1000 hours. But these fixed intervals don’t take into account the actual condition of the machine, and so they may be too long (wasting money on unnecessary downtime) or too short(waisting money on maintenance).
Conversely, predictive maintenance interval is based on the actual condition of the rotating machinery. Machine components are monitored for signs of wear and tear in real time, and maintenance is performed only when necessary on critical assets. This allows companies to optimize their maintenance schedules, reducing both downtime and cost.
This creation of a predictive maintenance program reduces maintenance costs, operational costs, improves asset uptime, and reduces your maintenance team work load. Mechanical equipment failures can be reduced to a minimum by implementing predictive maintenance. This preventive maintenance program is sure to improve your manufacturing company’s bottom line by converting scheduled maintenance to reactive maintenance.
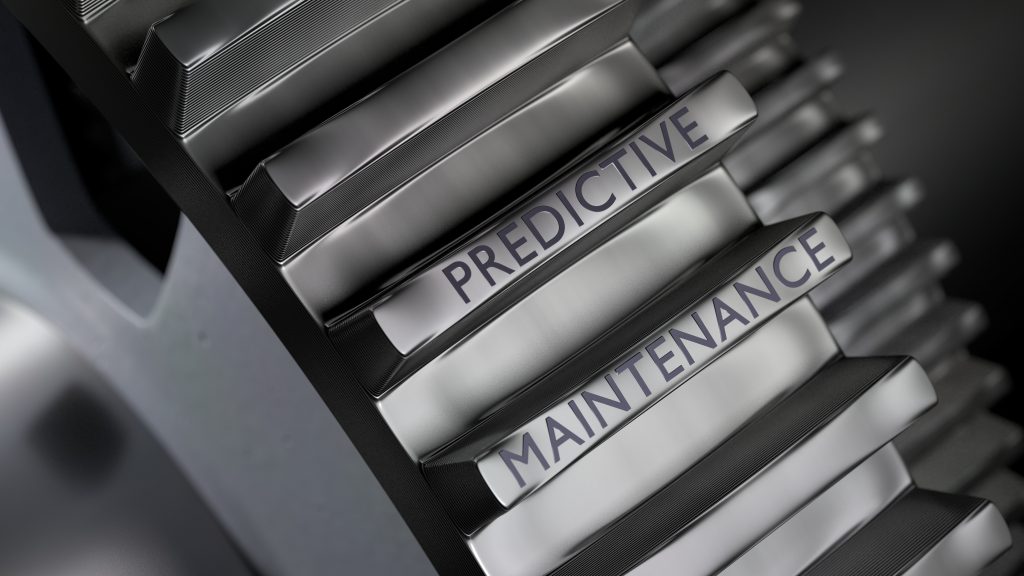
Condition Monitoring Telemetry for Preventive Maintenance
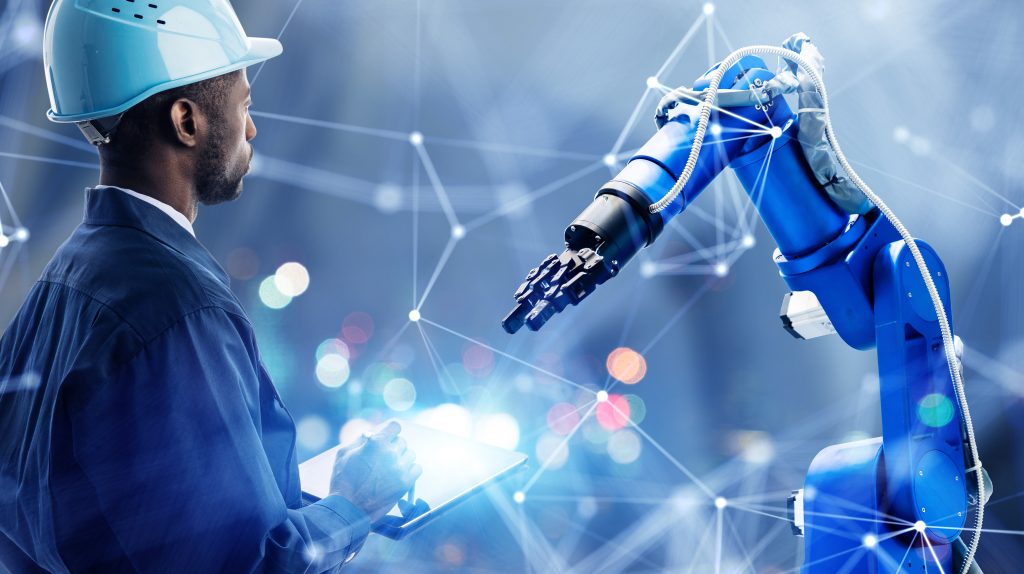
Condition monitoring for condition based maintenance can be implemented in any maintenance strategy. But the question is “What to monitor”? Vibration is one of the simplest condition monitoring indicators there is to monitor equipment condition or motor stress. This can be done with simple sensors available from NCD which mount to the surface of any motor, pump, etc. Data scientists will tell you that machine downtime can be reduced by regular maintenance activities based on asset history and the asset’s current behavior but the upfront costs of many tools used in conventional predictive maintenance are quite high and require trained staff which is not obtainable on every budget. This is why simple vibration analysis via off the shelf predictive algorithms in conjunction with NCD’s asset condition monitoring sensors may be a good solution for your company.
Another alternative for condition monitoring equipment may be our line of current monitoring sensors which can determine when the machine may be overloaded. The data generated by these sensors over time can help your maintenance managers predict machine failures before they happen. There are many condition monitoring techniques which can lead to prediction of equipment failure.
These sensors which do not require any subscription and can be monitored through local dashboards make predictive maintenance technology available to any company in the manufacturing industry looking for cost savings in their predictive maintenance programs.
Customization for your own Predictive Maintenance Program
The dashboard and flow demonstrated here is merely an example of how predictive maintenance aims to improve your asset reliability and reduce your inventory costs. However it can be customized in so many ways for your companies unique needs. Our staff will be happy to help you create a condition based maintenance strategy and and help you implement your own preventive maintenance program so please feel free to contact us with questions.
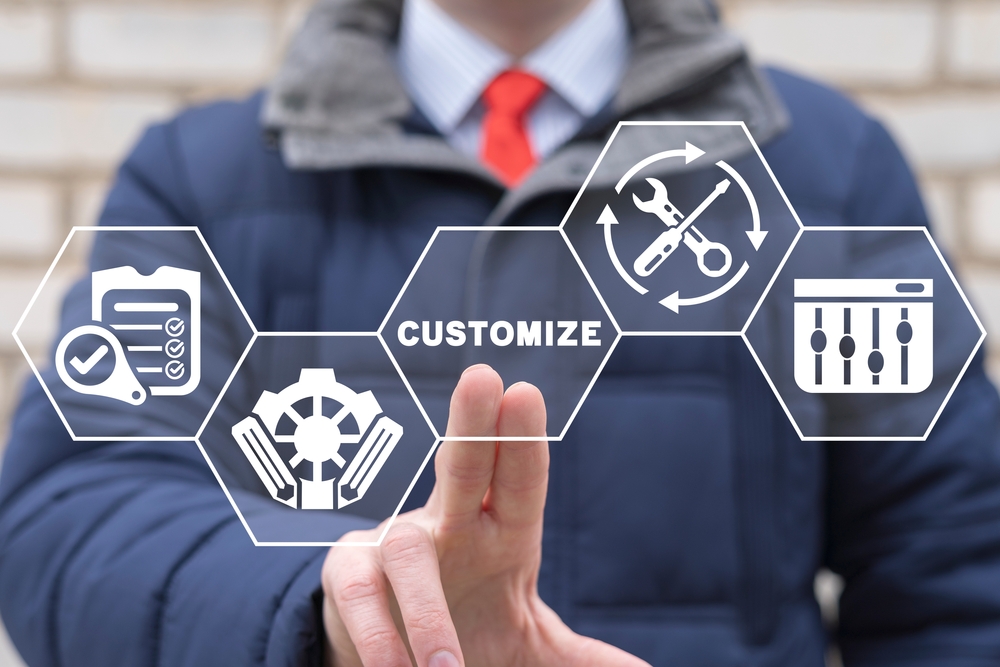
Conclusion
Vibration analysis is a simple, yet effective way of monitoring machine health. By analyzing the frequency peaks of vibrations in all three axis, it’s possible to estimate the health status and remaining useful life of a rotating electrical machine. This information can then be used to make informed decisions about maintenance and repair.
A dashboard makes vibration analysis simple by providing a quick and easy way to see the status of all machines at a glance. With color-coded tiles, it’s easy to tell at a glance if there are any issues with any of the machines. This allows operators to quickly and easily address any potential problems.
This solution is great if you don’t want to spend months learning the ins and outs of vibration analysis. You can quickly get an idea when a motor is not operating normally and what may be wrong with it so you have a great place to start diagnostics.
This solution is also very affordable, as you don’t need any expensive tools or software. All you need is a computer with an internet connection and our inexpensive vibration sensors. You can even use a Raspberry Pi!
If you’re interested in learning more about how this solution can benefit your company, please contact us. We would be happy to discuss your specific needs and help you create a custom solution.