Device Overview
Introducing NCD’s Explore the Standalone Smart Vibration Sensor Gen4 Capabilities. Lightweight rugged and reliable for accurate asset monitoring and boasting up to a 2-mile range using a wireless mesh networking architecture & Incorporating a 16-bit Vibration and integrated Temperature sensor.
This sensor combines these data with temperature data in a data packet, and transmits the result to modems and gateways within wireless range. Once transmission is complete, the vibration sensor goes back to sleep, thus minimizing power consumption.
Features:
- Small & lightweight for ease of installation.
- IP67 rated sealed enclosure for dust &
moisture protection. - Metal housing for durability in harsh industrial environments.
- D-cell battery for long-lasting operation.
- A versatile user-configurable sample rate for slow or fast-running machines
- Integrated temperature sensor in base.
- In-Built Machine Learning optimizes power consumption.
- Asset On-Time Calculator automatically tracks operational status.
- Hardware Accelerator enhances vibration sampling accuracy.
- Configurable Sample Rate – 100Hz to 25.6KHz
- Available Frequencies – 900Mhz, 868Mhz, and 2.4Ghz
- Supports MESH networking via DigiMesh
- Fully open Node-RED library for configuration and data ingestion
Wireless Technology
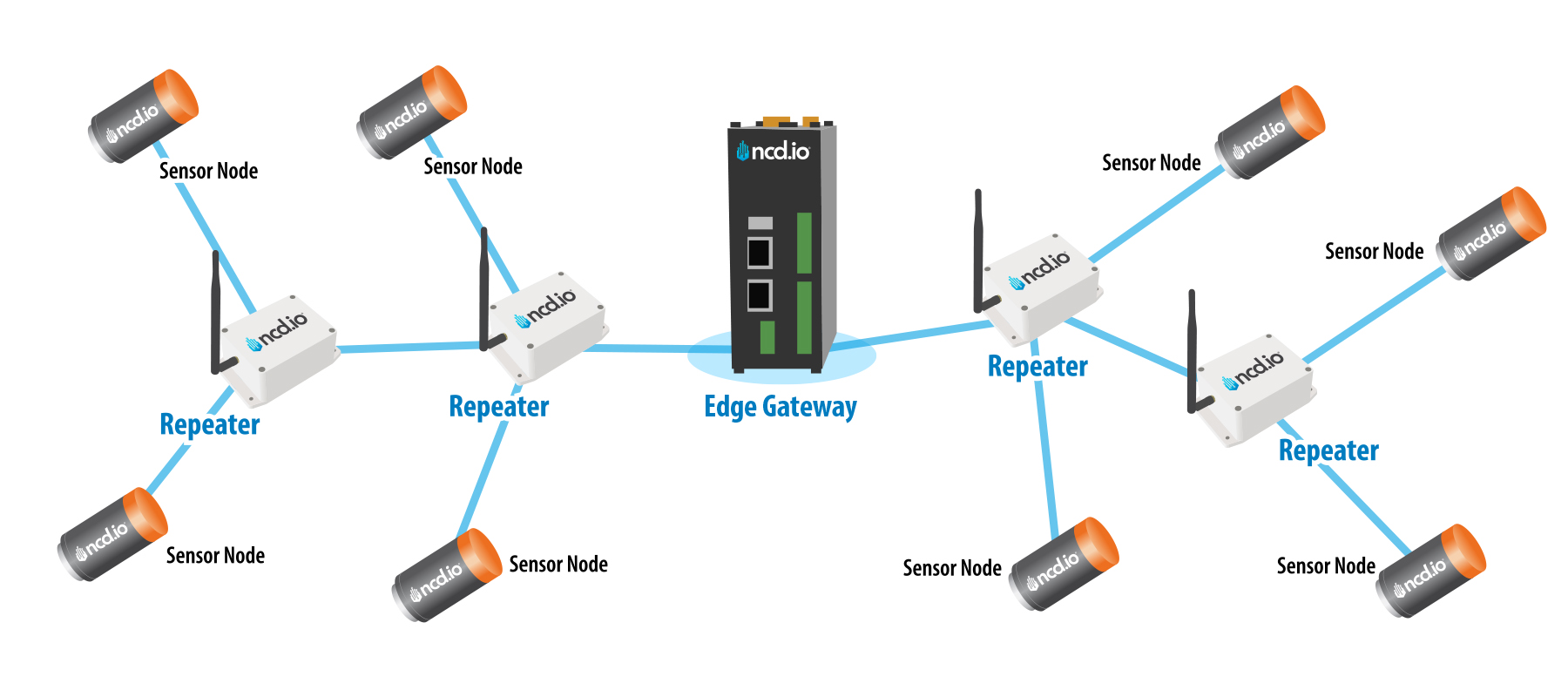
The NCD Industrial range of sensors utilizes DigiMesh, a proprietary networking technology designed by Digi® International. It is especially suitable for IIoT applications as it provides a number of benefits over conventional wireless stacks:
- Long range – up to 1000 feet in urban environments and 2 miles+ in open areas with the included antennas
- Mesh networking topology – no single point of failure, self healing network with high redundancy.
- Long battery life due to low power consumption – up to 10 years
- Simplified provisioning – extending the mesh network via repeater at no additional configuration complexity
- Works in the 868MHz, 900MHz and 2.4GHz bands – worldwide region interoperability.
Battery Life
Specifications | Minimum | Nominal | Maximum | Notes |
---|---|---|---|---|
Batteries size | 16000mAh | This device has a single D-Cell (LR20) battery | ||
Battery Life 1 TPD | 10 Years | TPD Transmissions per Day | ||
Battery Life 12 TPD | 8 Years | TPD Transmissions per Day | ||
Battery Life 24 TPD | 5 Year | TPD Transmissions per Day | ||
Battery Life 96 TPD | 3 Year | TPD Transmissions per Day |
The Truth About Battery Life
Under the best of circumstances, the best non-rechargeable batteries commonly available today are limited to a 10 year non-working shelf life in a room temperature environment. Factors such as actual usage, temperature, and humidity will impact the working life. Be wary of any battery claims in excess of 10 years, as this would only apply to the most exotic and expensive batteries that are not commonly available. Also note that most battery chemistries are not rated for use in extreme temperatures. NCD only uses the best Non-Rechargeable Lithium batteries available today, which are also rated for use in extreme temperatures and have been tested by our customers in light radioactive environments. Lithium batteries offer a 10 year maximum expected shelf life due to limitations of battery technology. NCD will never rate sensor life beyond the rated shelf life of the best batteries available today, which is currently 10 years.
Applications & Use-cases
This sensor is designed to monitor vibration, frequency, and temperature in industrial environments. It provides valuable data that can be used for predictive maintenance, equipment monitoring, and overall operational efficiency.
Standalone Smart Vibration Sensor Gen4 Applications
Advanced Predictive Maintenance for Rotating Equipment
The sensor can be strategically integrated into the maintenance programs for critical rotating machinery, including motors, pumps, compressors, and turbines. By continuously monitoring vibration, frequency, and temperature data, the sensor provides insights into the health of the equipment, detecting early signs of issues such as misalignment, imbalance, or bearing wear. This data-driven approach enables the scheduling of maintenance activities before the equipment fails, reducing unexpected downtime, minimizing repair costs, and extending the operational lifespan of machinery.
Comprehensive Structural Health Monitoring
The sensor can be deployed on infrastructure like bridges, buildings, towers, and dams to detect abnormal vibrations that may signal structural deficiencies or damage. For example, in a bridge, the sensor can track changes in vibration patterns caused by material fatigue, loose joints, or foundation shifts. With continuous monitoring, it is possible to identify and address potential risks well before they escalate into safety hazards, ensuring the long-term integrity and reliability of critical infrastructure.
Process Automation and Quality Control in Manufacturing
In manufacturing environments, the sensor can be installed on key equipment such as conveyors, CNC machines, or robotic arms. By monitoring vibration data in real-time, the sensor can detect when machinery is operating outside its optimal conditions, which may indicate tool wear, imbalance, or other mechanical issues. Integrating this data with a manufacturing execution system (MES) allows for automatic adjustments, immediate alerts, or even shutdowns to prevent defects in products, enhance process efficiency, and maintain consistent product quality.
Optimization of Energy Efficiency in Industrial Systems
The sensor can be applied to monitor vibration levels in energy-intensive equipment such as HVAC systems, large fans, generators, and industrial chillers. Abnormal vibration often correlates with inefficiencies like misalignment, unbalanced loads, or mechanical wear, leading to increased energy consumption and operational costs. By detecting these issues early, the sensor supports proactive maintenance that reduces energy waste, improves the performance of systems, and contributes to the overall sustainability goals of the organization.
Standalone Smart Vibration Sensor Gen4 Use-cases
Air Compressor Motor Monitoring
Installed on the motors powering air compressors, the vibration sensors continuously track motor performance to detect issues such as bearing wear, rotor imbalance, or misalignment. When abnormal vibration patterns are identified, the system automatically triggers alerts to the maintenance team, allowing them to address potential failures before they disrupt operations. This proactive approach ensures a steady supply of compressed air, which is vital for powering pneumatic tools and automated machinery, thereby minimizing downtime, reducing repair costs, and maintaining peak production efficiency.
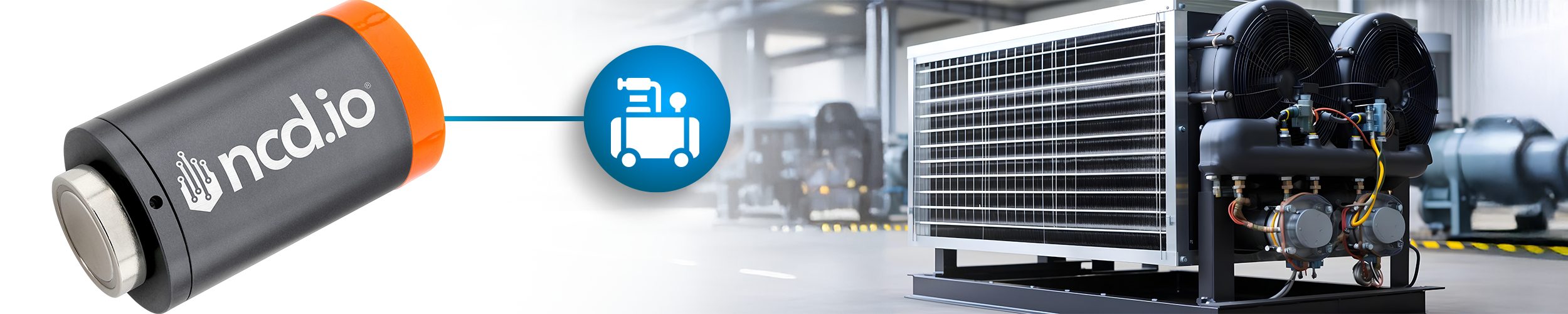
Industrial Pumps Monitoring
In a large-scale manufacturing plant, industrial pumps play a critical role in circulating cooling fluids and transferring raw materials. To ensure continuous operation, vibration sensors are installed on pump motors to monitor their performance in real-time. These sensors track vibration patterns and detect early signs of issues such as bearing wear, shaft misalignment, or pump cavitation.
When abnormal patterns are identified, the system automatically sends alerts to the maintenance team, allowing them to schedule repairs before a breakdown occurs. This predictive approach prevents costly downtime, reduces maintenance expenses, and extends the lifespan of the equipment. Additionally, the collected vibration data is analyzed over time to identify trends, helping the plant optimize maintenance schedules and improve overall system reliability.
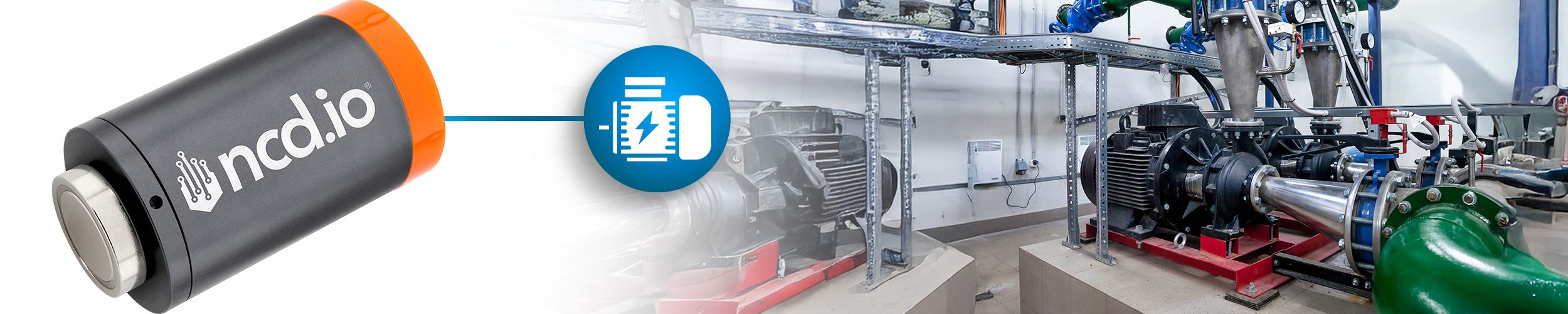
Industrial Fan and Blower Performance Monitoring
In a large-scale industrial facility, the sensor is used to monitor the vibration of high-capacity fans, blowers, and ventilation systems. By detecting early indicators of imbalance, misalignment, or bearing failure, the sensor allows maintenance teams to intervene before minor issues escalate into major problems. Ensuring the optimal performance of these systems is crucial for maintaining air quality, temperature control, and overall operational efficiency in the facility, preventing costly downtime and ensuring regulatory compliance.
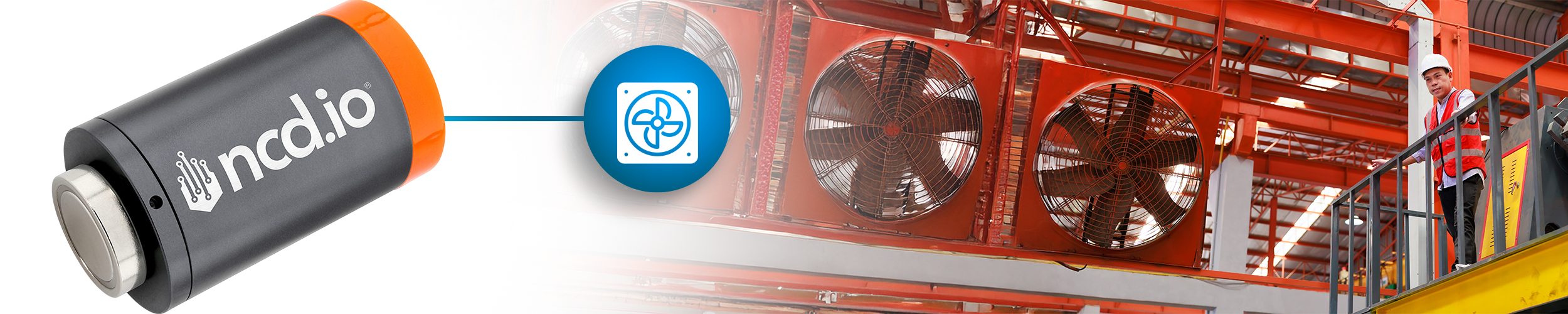
Conveyer Belt Monitoring
Industrial conveyer belt installation especially those of large size like for example at dig sites have multiple rotational components that are under a heavy load. Stress to these installation is high and so are vibrational levels. It is essential they are monitored in real time, as a fault could be very dangerous. Furthermore as these are often off-site from cities, it is difficult to perform maintenance if it is unexpected. Monitoring vibrations in real time for example at crucial bearings along the line or at the driver/gear box at multiple points could give insights on potential issues before they occur. This would essentially enable the implementation of a solid predictive maintenances strategy and increase reliability and operational efficiency (by reducing downtime).
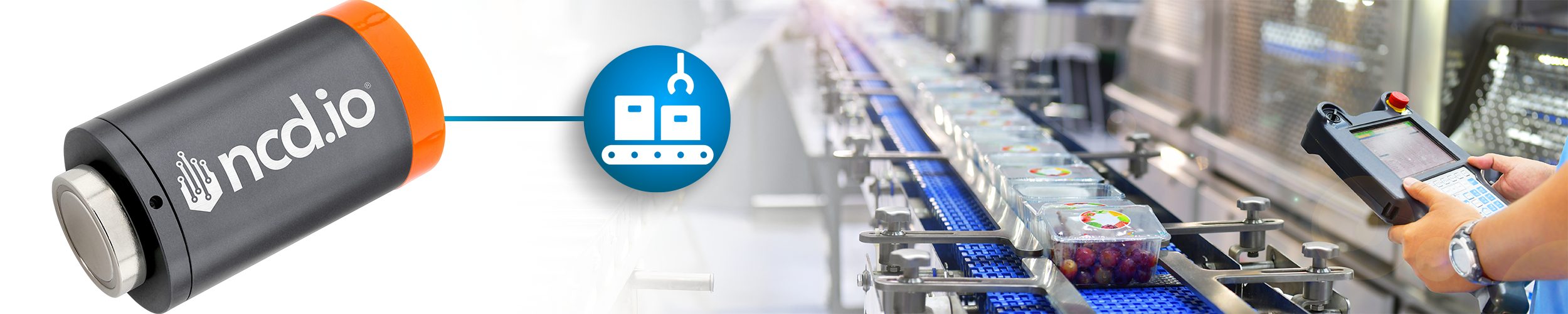