- Introduction
- Applications
- Hardware
- Software API Structure
- Machine Uptime Monitoring Sensor Payload Structure
- Sensor Configuration Structure
- Enter Configuration Mode
- Read Sleep Duration
- Set Sensor Node ID and Sleep Duration
- Read Sensor Network ID
- Set Wireless Sensor Network ID
- Read Sensor Destination Address
- Set Sensor Destination Address
- Set Sensor Destination to Broadcast
- Read Wireless Sensor Transmission Power Level
- Read Wireless Sensor Retries
- Set Wireless Sensor number of Retries
- Set Wireless Sensor Encryption Key
- Configuration Commands Table
- Sensor App Specific Configuration Commands Table
- Device Inputs and Working Principle
- Installation Guidelines
- Troubleshooting Guide
Introduction
1
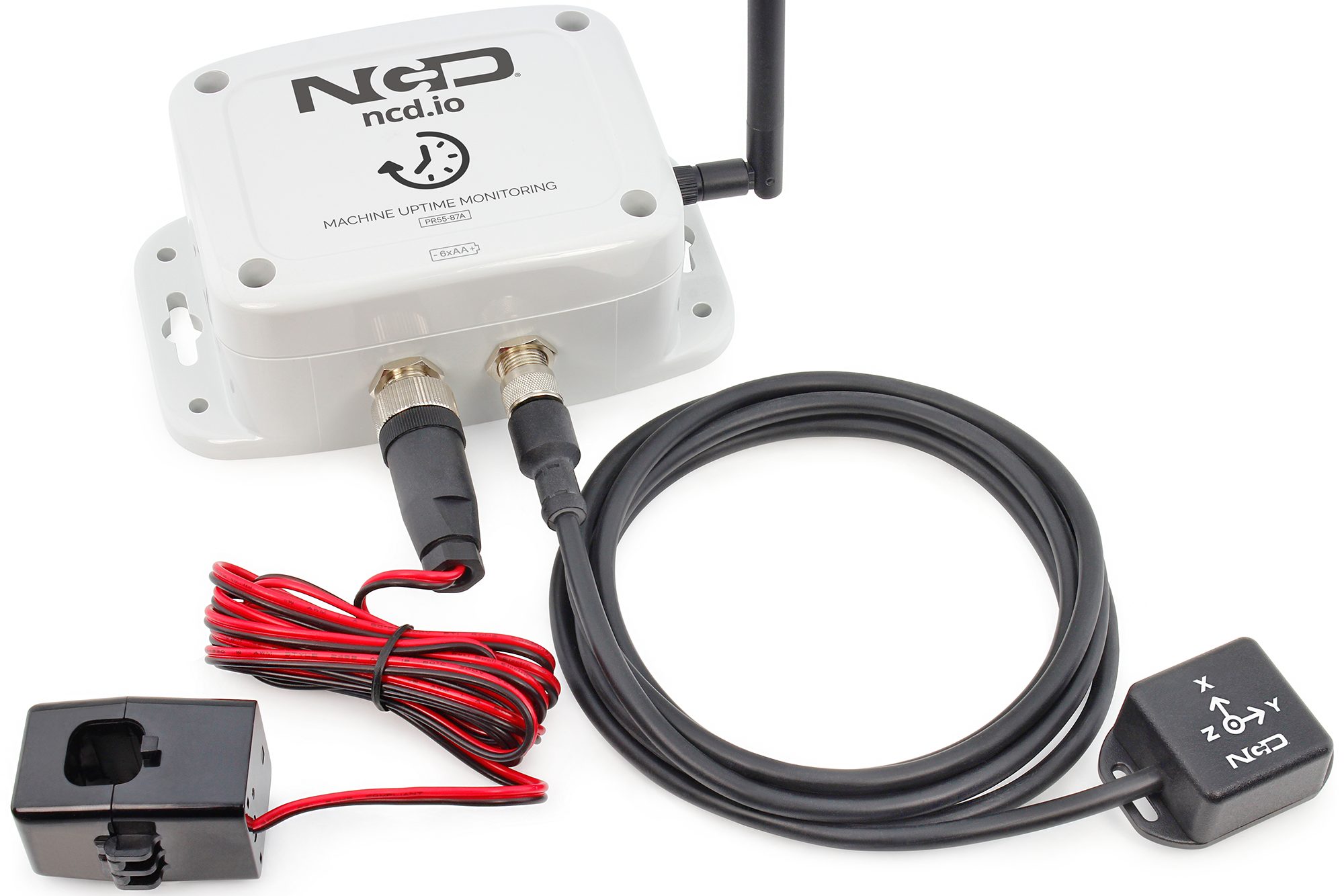
- Industrial Grade Machine Uptime Monitoring
- Measure Production Uptime
- Measure Number of Cycles
- Dry Contact Closure Input
- Wet Contact Closure Input
- Acceleration Motion Detection based Uptime calculator
- Magnetic Field Detection based Uptime calculator
- Current-based Uptime calculator
- Encrypted Communication with 2 Mile Wireless Range
- Operating Temperature Range -40 to +60 °C
- Humidity Range 0-90%
- Wall-Mounted or Magnet Mounted IP65 Rated Enclosure
- For Indoor and Outdoor Use
- Many Gateway and Modem Options Available
The Machine Up-Time Monitoring Sensor is an innovative solution designed to track and analyze the operational efficiency of industrial machinery. Leveraging advanced digital inputs, current sensing technology, acceleration detection, and magnetic field measurement capabilities, this sensor provides comprehensive insights into machine performance. With its robust IP65 rating, battery-powered operation, and long-distance communication capabilities through Digimesh Sub GHz radio, the sensor ensures reliable data collection in diverse industrial environments. Moreover, its versatile compatibility allows seamless integration with any cloud platform, local PC, or server for centralized monitoring and analysis.
Key Features:
Multi-Sensor Functionality: Integrates digital inputs, current sensor, acceleration detection, and magnetic field measurement capabilities for comprehensive machine performance monitoring.
IP65 Rating: Designed to withstand harsh industrial environments, ensuring durability and reliability in challenging conditions such as dust, moisture, and vibration.
Battery-Powered Operation: Enables easy installation without the need for external power sources, facilitating flexibility in sensor placement and minimizing downtime during setup.
Digimesh Sub GHz Radio: Utilizes advanced radio technology for long-range communication, allowing seamless transmission of data over extended distances within industrial facilities.
Versatile Connectivity: Compatible with a wide range of cloud platforms, local PCs, and servers, offering flexibility in data management and analysis based on user preferences and existing infrastructure.
Real-Time Monitoring: Provides real-time updates on machine up-time, downtime, and performance metrics, enabling prompt identification of issues and proactive maintenance strategies.
User-Friendly Interface: Offers intuitive dashboards and analytics tools for easy visualization and interpretation of machine performance data, empowering users to make informed decisions.
Scalable Solution: Suitable for deployment in small-scale operations as well as large industrial facilities, with scalability to accommodate varying needs and requirements.
Specifications
Specifications | Minimum | Nominal | Maximum | Notes |
---|---|---|---|---|
Transmission Rating | 500,000 | Total Number of Wireless Transmissions When Using 4 AA Batteries | ||
Batteries | 2 | 6 | 6 | May be Powered by 2 or 4 AA Batteries |
Battery Life 1 TPD | 10 Years | TPD Transmissions per Day | ||
Battery Life 3 TPD | 8 Years | TPD Transmissions per Day | ||
Battery Life 6 TPD | 4 Years | TPD Transmissions per Day | ||
Battery Life 12 TPD | 2 Years | TPD Transmissions per Day | ||
Battery Life 24 TPD | 1 Year | TPD Transmissions per Day | ||
Width | 3.54" | |||
Length | 4.52" | |||
Height | 2.16" | |||
Enclosure Rating | IP65, NEMA 1,2,4,4X,12,13, UL-508 | |||
Temperature Rating | -40° C | 23° C | 85° C | Component Rating |
Tested Temperature | 0° C | 23° C | 40° C | As Tested by NCD Staff |
Probe Temperature | -40° C | 23° C | 105° C | As Tested by NCD Staff |
Inputs | Digital, Acceleration, Magnetic, Current |
Use Energizer Ultimate Lithium ONLY for Extreme Temperatures
All Ratings are for 6 Batteries
Actual Battery Life is Dependent On Transmission Interval
Battery Shelf Life Does Not Exceed 10 Years Therefore NCD Does Not Rate Battery Life Beyond the Shelf Life of Available Batteries
** Battery life will significantly reduce when time domain mode is enabled
Applications
3
- Manufacturing plants
- Automotive production lines
- Food processing facilities
- Chemical and pharmaceutical industries
- Mining and heavy machinery operations
Hardware
4
Sensor Hardware
The Machine Uptime Sensor hardware can be divided into two parts.
A. Main Electronics Box
This box ( White Box) contains Electronics such as MCU, Radio Module, Power Circuitry, Power Control unit, Status LED, on/off Switch, Configuration Button etc.
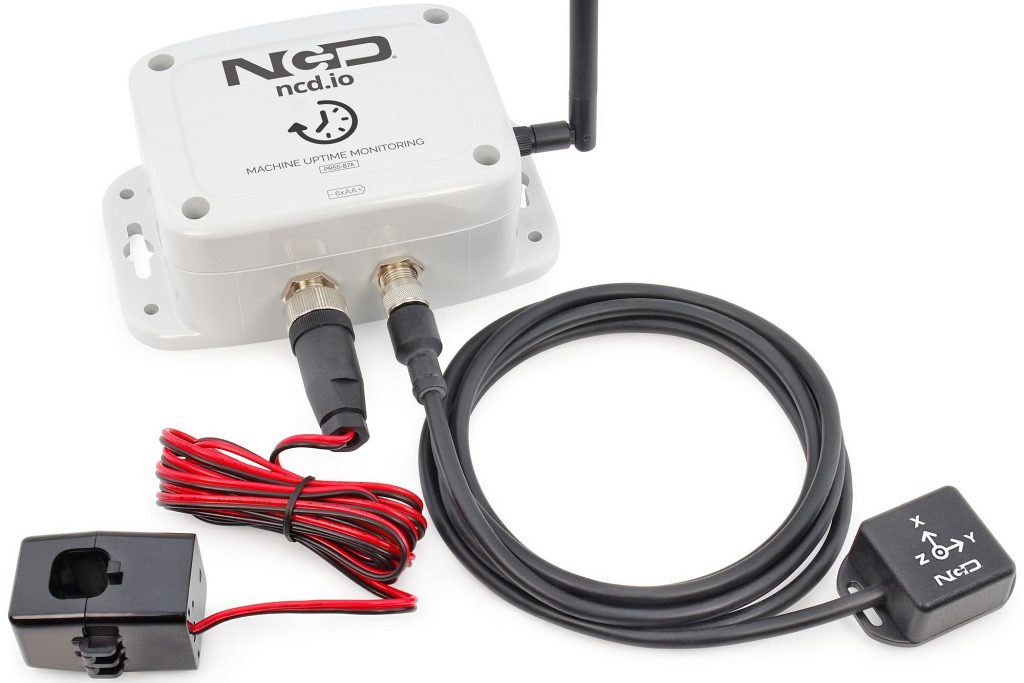
B. The Probe
There are 4 Types of probes.
- Bare Wire for Digital Inputs
- Current Sensor
- Accelerometer
- Magnetometer
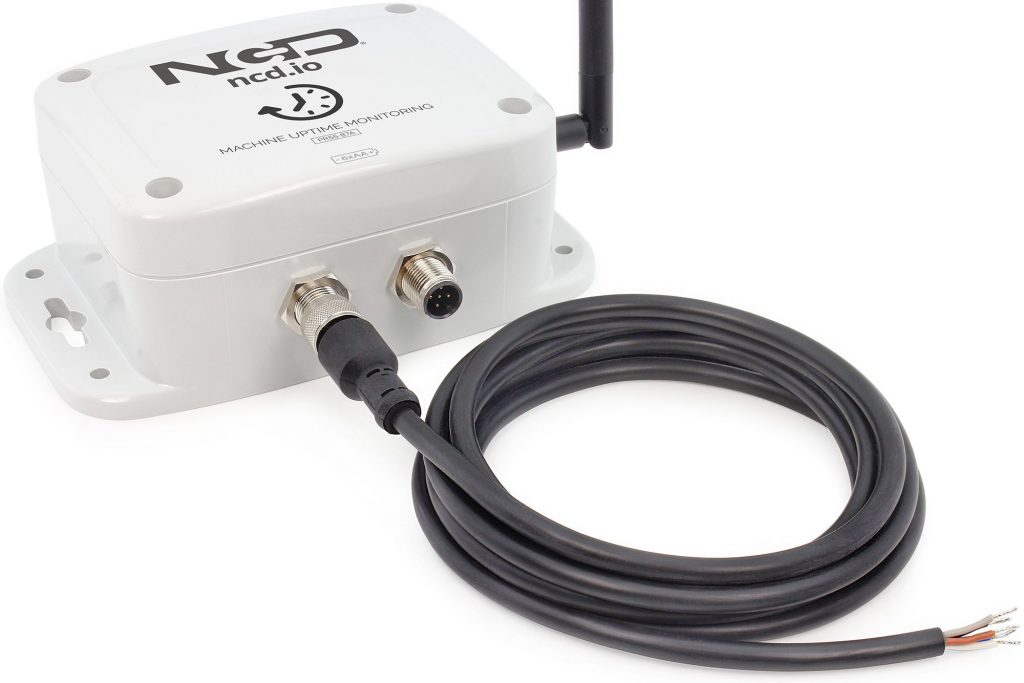
Mechanical Drawing
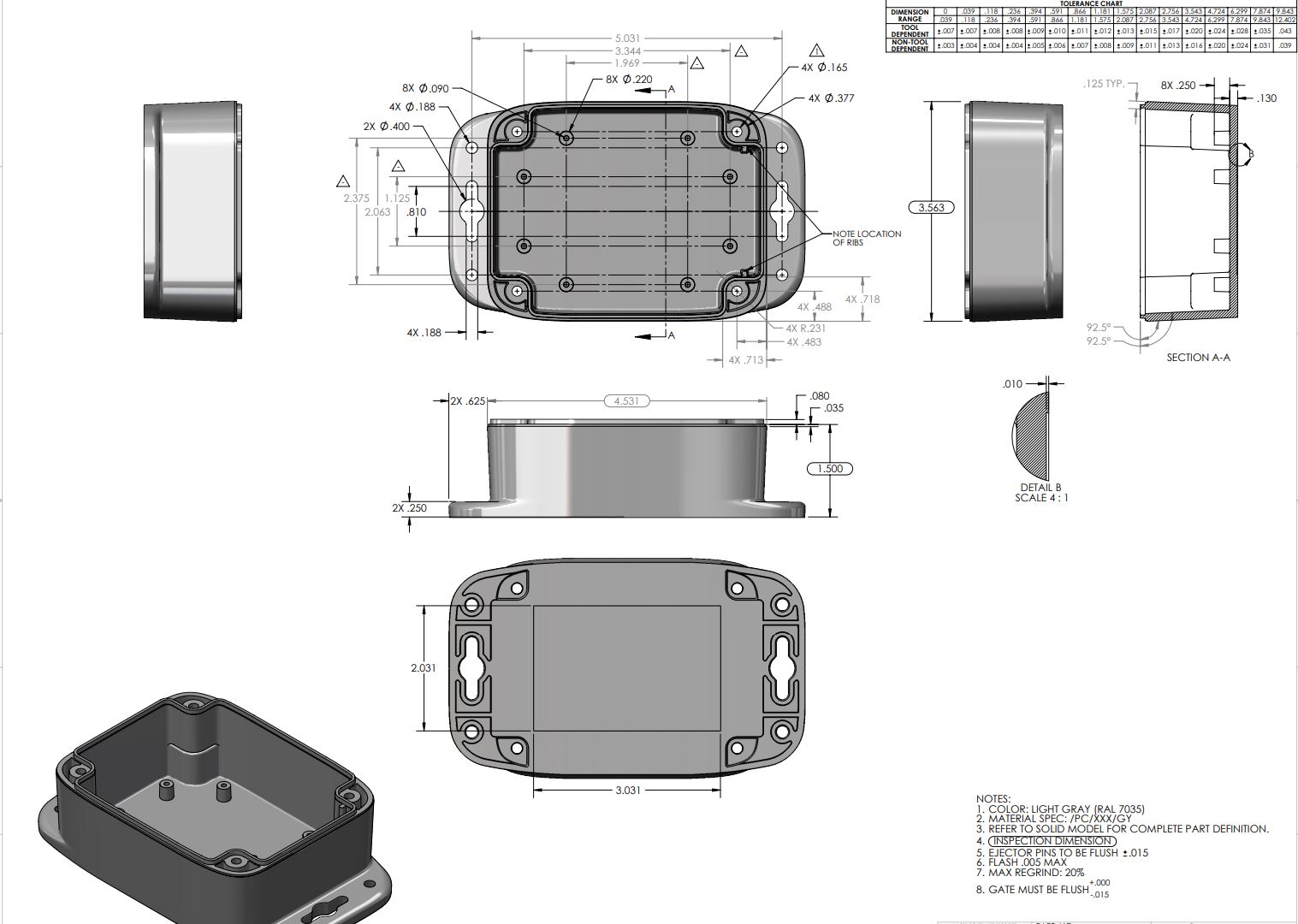
Internal Components
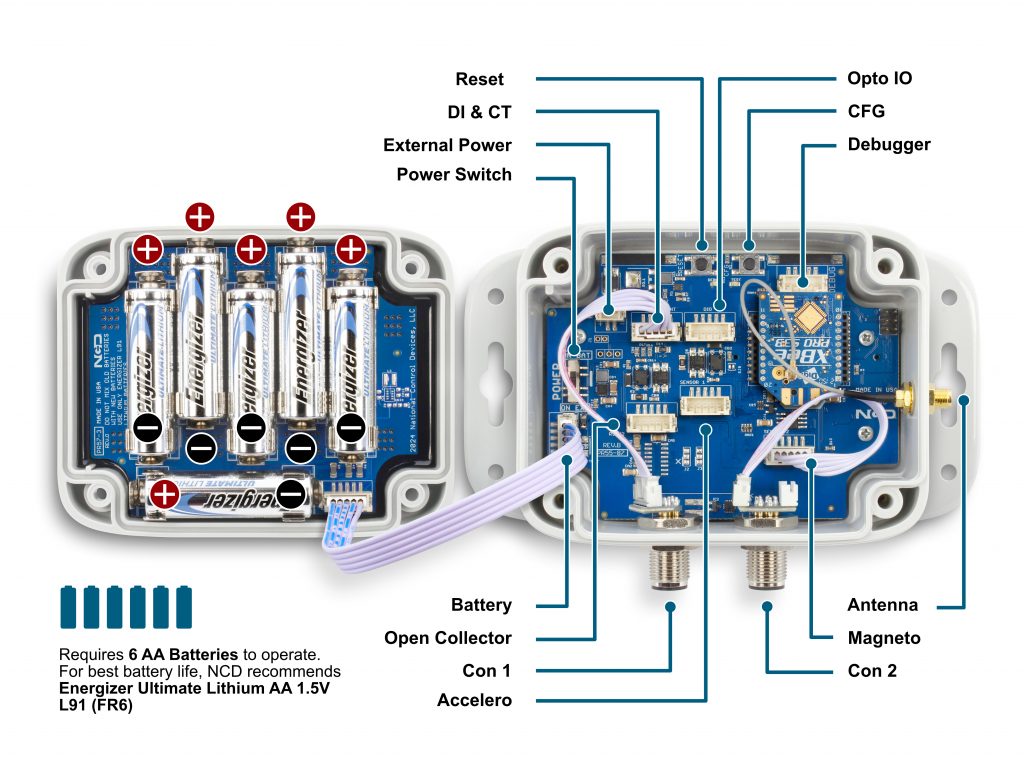
- Inside NCD sensors, you will find a high-power radio communications module, 6-AA batteries (included when possible), a sensor element (if applicable) or a connector (for external functionality).
- NCD sensors consume less than 20µA in standby with an operational life estimated at 500,000 transmissions using 6-AA batteries.
Sensor Diagram
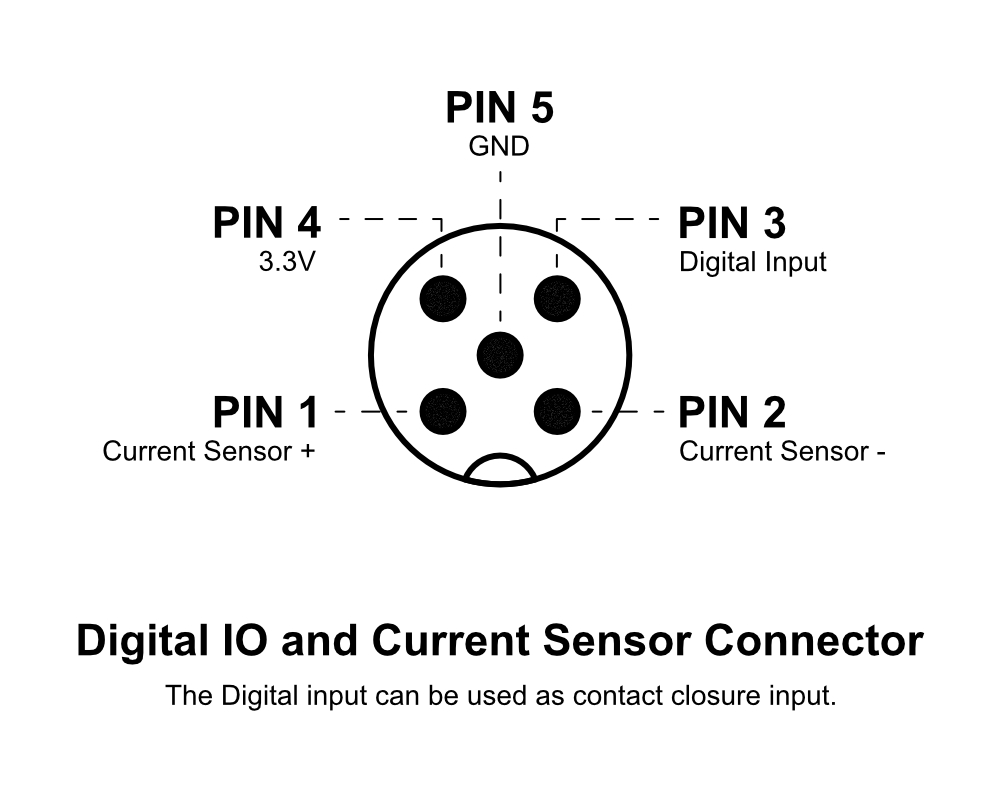
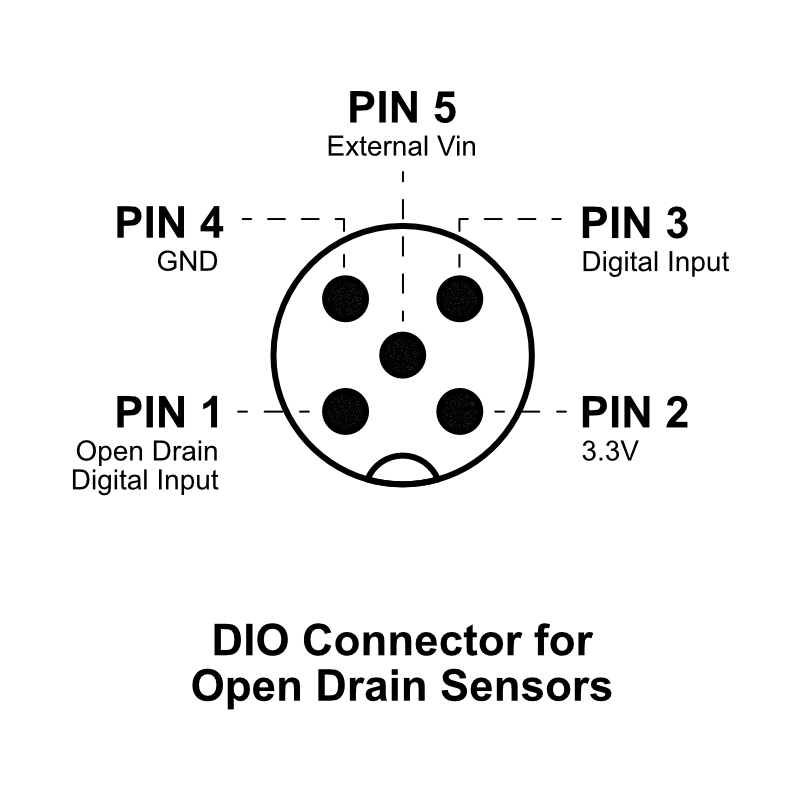
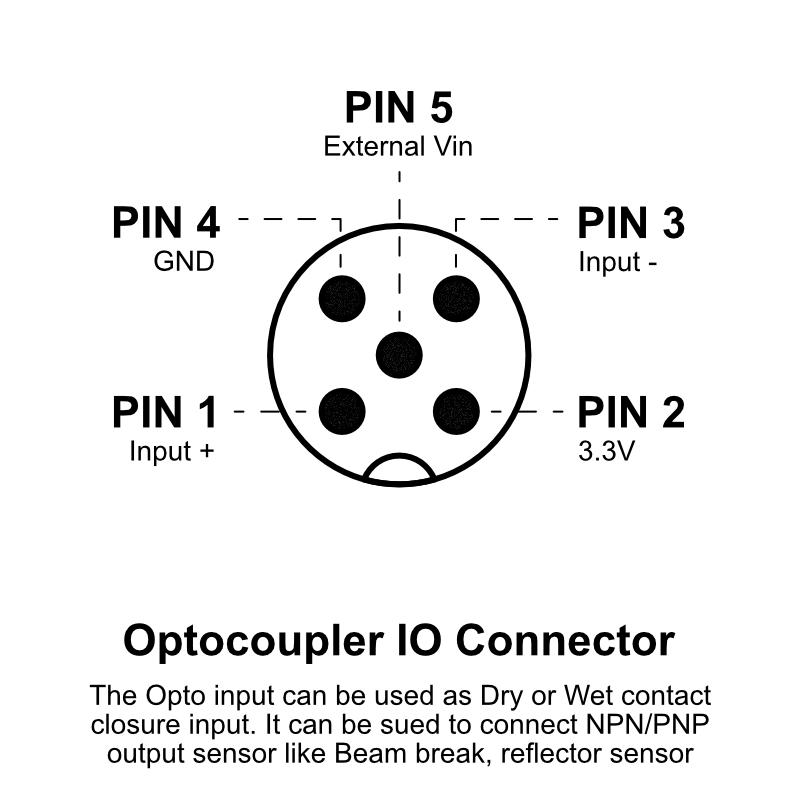
Digital Inputs
The Industrial Digital Input and Sensor Reader is a compact and robust device tailored to interpret signals from various digital inputs and sensors prevalent in industrial settings, including brake sensors, photo reflectors, and on/off signals. With high accuracy and reliability, it offers real-time data acquisition and monitoring, seamlessly integrating into existing industrial automation systems. Its user-friendly interface and flexible configuration options ensure easy setup and compatibility with diverse applications, enhancing operational efficiency, equipment reliability, and production optimization. Ideal for conveyor systems, packaging machinery, and robotic systems, it empowers industrial operators with streamlined data interpretation and control capabilities, minimizing downtime and maximizing productivity.
Accelerometer Sensor
The Cycle and Uptime Tracker is an innovative device engineered to monitor and record the number of cycles and total uptime of machinery or equipment in industrial environments. Leveraging advanced acceleration sensing technology, users can set customizable acceleration thresholds to precisely detect cycle initiations. This allows for accurate tracking of machine activity while minimizing false readings. The device captures and stores data, providing insights into equipment usage patterns and overall uptime. With its user-friendly interface and customizable settings, operators can easily configure acceleration thresholds to suit specific machinery requirements. Ideal for diverse industrial applications, the Cycle and Uptime Tracker enhances maintenance planning, optimizes production scheduling, and improves operational efficiency.
Magnetometer Sensor
Magnetic Field-Based Machine On/Off Detection System is meticulously engineered to precisely discern the operational status of machinery that emits magnetic fields during operation. Employing cutting-edge magnetic field sensors, this system offers unparalleled accuracy in identifying whether the machine is active or inactive. With its robust design and reliable performance, there’s no need for user adjustments, ensuring hassle-free operation. Real-time monitoring capabilities enable proactive maintenance planning and energy conservation, enhancing operational efficiency. Seamlessly integrating into various industrial setups, this system represents a pinnacle of reliability and professionalism in machine monitoring solutions.
Current Sensor
Industrial Machine Uptime and Cycle Counter, a cutting-edge solution that accurately measures total machine uptime and cycle counts using advanced current sensor technology. With real-time monitoring and seamless integration, our device enables proactive maintenance planning, enhances operational efficiency, and provides valuable insights for informed decision-making. Upgrade your industrial operations with precise tracking and analysis capabilities for optimized performance and cost savings.
Sensor Power
This Sensor has two power options.
- Powered by AA batteries ( NCD recommends Energizer L91 batteries)
- External Power Supply ( 5-12VDC) Current Requirement 250mA
The L91 Batteries are non-rechargeable Li-Ion batteries.
While changing the batteries
- Turn off The sensor
- Only use new L91 batteries
- Checkout the Polarity marking on the Battery Holder and Batteries
- Replace All six batteries with new L91 batteries. Do not mix old and new batteries
- Batteries should not be replaced in fire-risky areas
- Do NOT install rechargeable batteries
Note — If these Devices are being used with photo eye or any other sensors needing power, use an external power supply.
Gateway
In Order to receive the sensor data, A gateway or Modem is required. The receiver can receive data from multiple sensors.
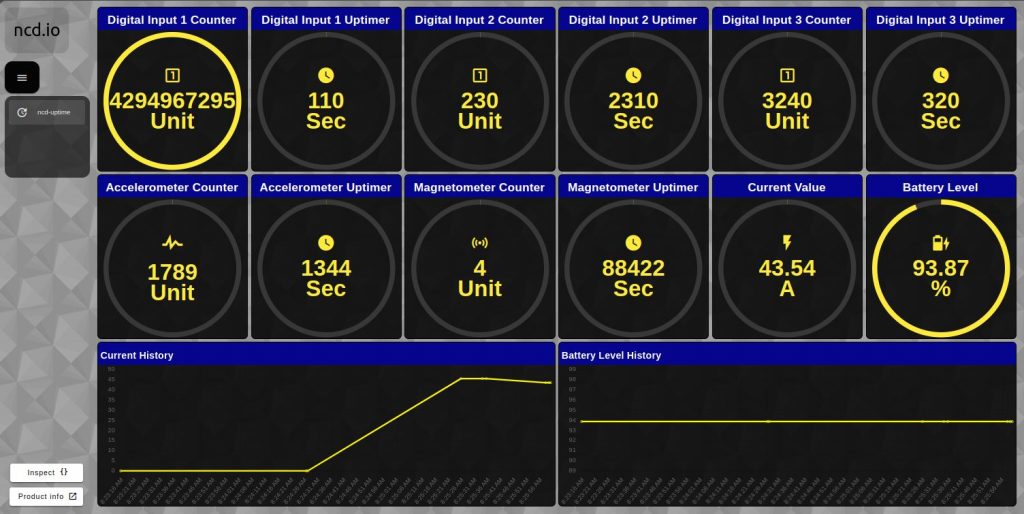
Sensor Radio Technology
NCD Long Range Wireless Sensors are available with many radio options, which should be carefully chosen based on the country of installation. NCD uses Digi radios exclusively because of their best-in-class range, reliability, wide operating temperature, and low power operation. Please note that not all options are legal for use in all areas, so it’s important to make the right selection during purchase. NCD manufactures sensors based on the radio options chosen, we do not typically restrict radios to certain countries so please check local laws BEFORE purchase. Here, we will explain the radio options in greater detail to help guide users into the correct radio based on installation country.
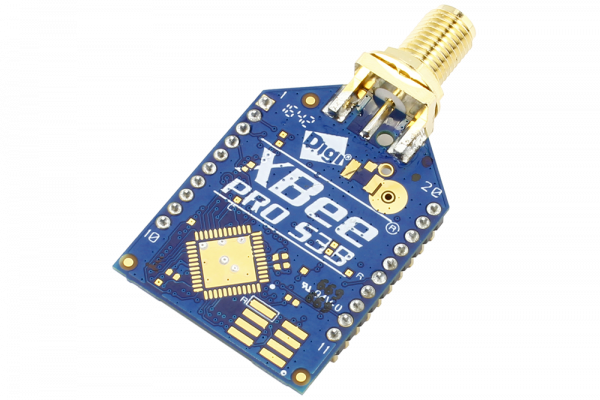
900MHz for Use in the United States
If NCD sensors will be installed within the United States, the 900MHz (North America) option is the best choice, offering the longest possible range of up to 2 Miles Line of Sight and up to 28 Miles using High-Gain Antennas. This option can typically work up to 1,000 feet indoors (depending on building materials, concrete and steel building typically reduce the operational range significantly). This option is typically not legal for use outside North America.
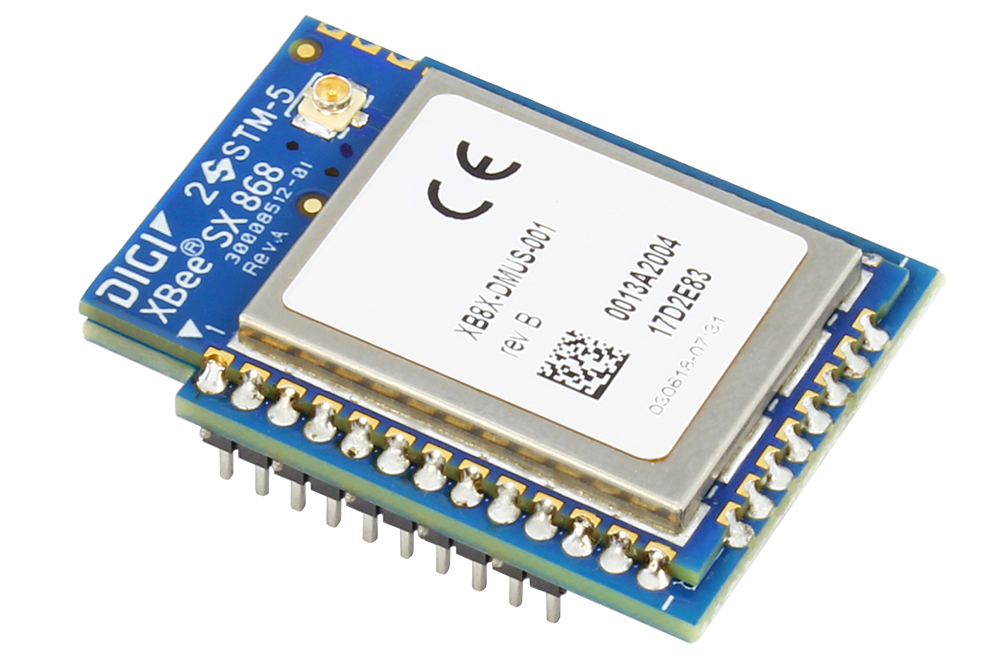
868MHz for Use in Europe
If NCD sensors will be installed in Europe, the 868MHz (Europe Only) option is the best choice, offering the longest possible range of up to 14.5km Line of Sight. This option is typically not legal for use outside of Europe.
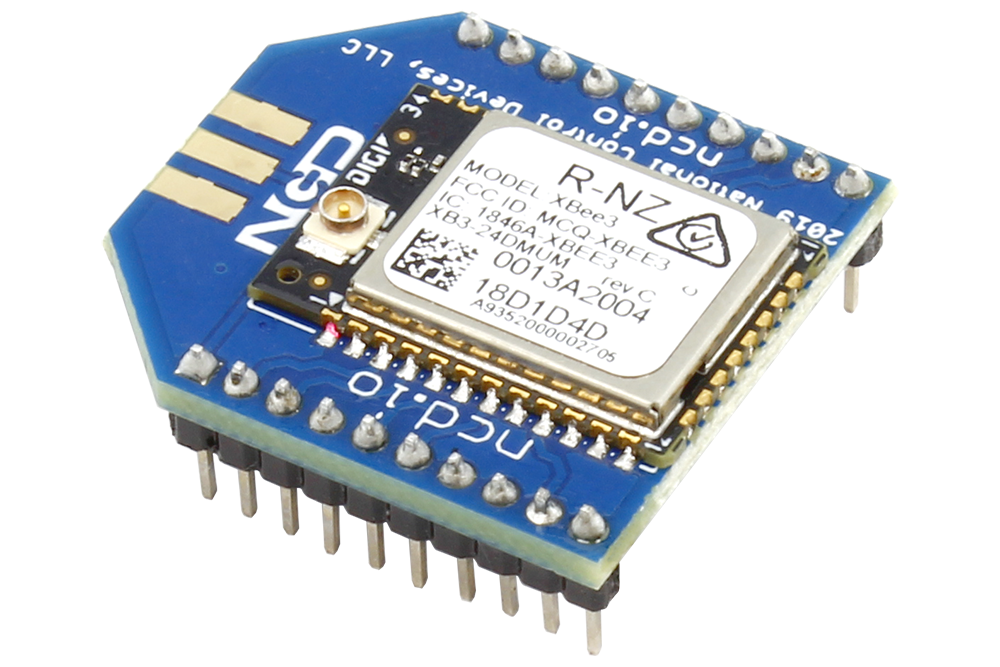
2.4GHz for Worldwide Use
The 2.4GHz Option is generally legal for use in most countries, including Europe and the United States and offers a range of up to 2 Miles (3200 Meters) Line of Sight or up to 300 feet (about 90 Meters) indoors. Because of the widespread use of 2.4GHz, the rated ranges are rarely achieved. The 900MHz and 868MHz communication modules are a far better choice for users in the United States and Europe respectively. Users who may require worldwide compliance should use the 2.4GHz option, but this option should be considered if the above options are not legal for use.
Sensor Internal Overview
Status LED – The status led is used to indicate errors or other sensor diagnostics.
LED Blink Once – Message was sent successfully and no error in last sensor read as well in data transmission
LED Blink Twice and then One more time — Message was sent successfully but there was an error in last sensor read
LED blink Thrice — MCU is having issue communicating with Radio Module
Software API Structure
6
Machine Uptime Monitoring Sensor Payload Structure
Field | Description | Comment |
---|---|---|
Header | 7F | API Data Header ( its not the API Header) |
Node ID | 00 | User Defined ID |
Firmware Version | 01 | Device Firmware Version |
Battery Level | 03,FE | Battery Voltage = 0.00322*(03*FF+FE) |
Packet Counter | DE | Wireless Transmission Counter |
Sensor Type | 00,0x51 | Sensor Type 80 |
Error/Reserve Byte | 00 | |
Current Value in A (x100) | D0,D1 | Current = (D0<< 8 | D1)/100 |
Digital Input 1 Counter | D2,D3,D4,D5 | Counter 1 = D2 << 24 | D3 << 16 | << D4 << 8 | D5 |
Digital Input 1 Uptimer | D6,D7,D8,D9 | Uptimer 1 = D6 << 24 | D7 << 16 | << D8 << 8 | D9 |
Digital Input 2 Counter | D10,D11,D12,D13 | Counter 2 = D10 << 24 | D11 << 16 | << D12 << 8 | D13 |
Digital Input 2 Uptimer | D14,D15,D16,D17 | Uptimer 2 = D14 << 24 | D15 << 16 | << D16 << 8 | D17 |
Digital Input 3 Counter | D18,D19,D20,D21 | Counter 3 = D18 << 24 | D19 << 16 | << D20 << 8 | D21 |
Digital Input 3 Uptimer | D22,D23,D24,D25 | Uptimer 3 = D22 << 24 | D23 << 16 | << D24 << 8 | D25 |
Accelerometer Counter | D26,D27,D28,D29 | Accelero Counter = D26 << 24 | D27<< 16 | << D28 << 8 | D29 |
Accelerometer Uptimer | D30,D31,D32,D33 | Accelero Uptimer = D30 << 24 | D31 << 16 | << D32 << 8 | D33 |
Magnetometer Counter | D34,D35,D36,D37 | Magneto Counter = D34 << 24 | D35<< 16 | << D36 << 8 | D37 |
Magnetometer Uptimer | D38,D39,D40,D41 | Magneto Uptimer = D38<< 24 | D39 << 16 | << D40 << 8 | D41 |
Sensor Configuration Structure
The following guide demonstrates the fundamental configuration commands required to configure NCD Enterprise Low-Power Long Range Wireless Sensors. A Wireless USB Modem will be required to configure NCD wireless sensors over a wireless connection. The examples shown below assume prior knowledge of DigiMesh® API Packet Structure, including MAC addresses and checksum calculations.
Please note the MAC address MUST be changed (shown in the API frames below as 00 13 A2 00 41 91 1B 83) to match the MAC address of a remote sensor. The checksum must also be re-calculated (the last byte of the API frame) to include the new MAC address. Additionally, the PAN ID must be set to 0x7BCD. This PAN ID is reserved for configuration ONLY, and may not be used for daily operation.
The commands shown below are explained in greater detail within product manuals, this guide is a summary overview of all configuration command samples. Also note that configuration commands cannot be sent to NCD wireless sensors while in run mode. Each sensor must be placed in configuration mode, which will drain the battery very quickly. Be SURE to execute these commands quickly and return each sensor to RUN mode to preserve battery life. Optionally, select NCD wireless sensors may be powered from a external power supply during configuration.
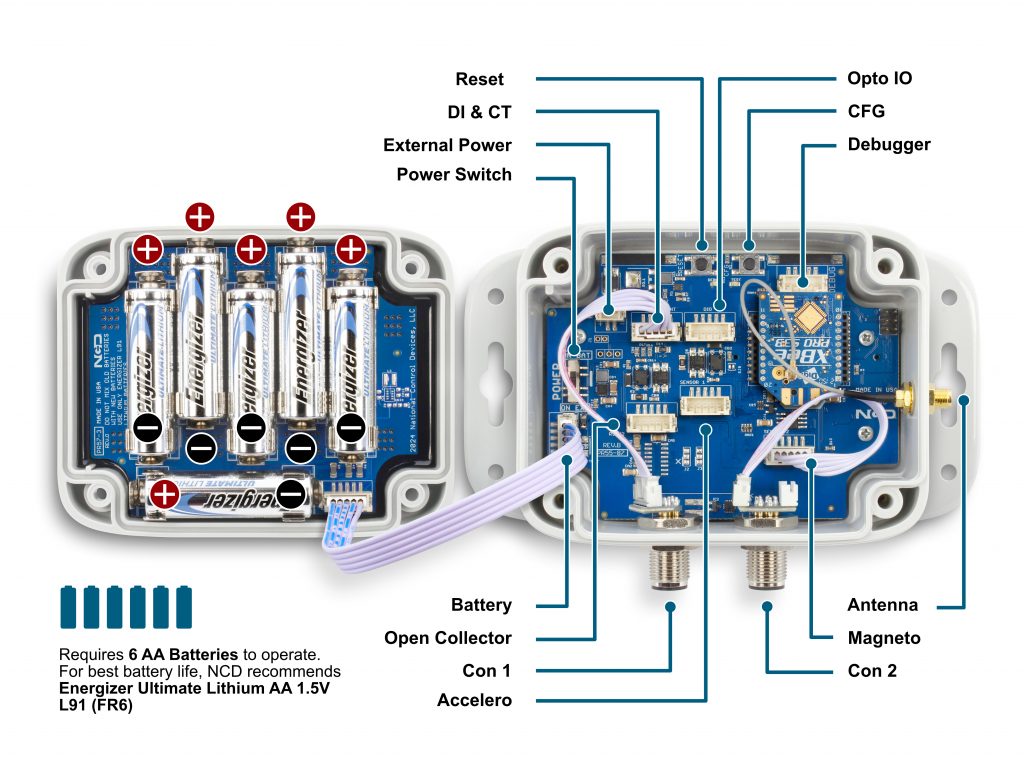
Enter Configuration Mode
To configure Gen 2 sensors, two distinct approaches are available:
Method 1: Manual Configuration In this method, we employ both the config and reset buttons to initiate configure mode. To start, press and release the reset button, wait for 1 second, then press and hold the config button for 6 to 10 seconds before releasing it. This action puts the device into configure mode. Once in this mode, Node-RED can be used to adjust the sensor’s settings.
Method 2: Over The Air (OTA) Configuration Gen 2 devices are capable of OTA configuration, which allows for remote adjustments. In this mode, the device broadcasts a “FLY” message approximately every hour, signaling its readiness to receive new configurations. The “FLY” message essentially indicates, “I am awake; send me commands or configuration settings.” Node-RED can capture this message and transmit the desired settings to the sensor. This approach enables users to configure the sensors without physical interaction. Additionally, activating the reset button prompts the device to emit the “FLY” message immediately, facilitating quicker configuration.
Factory Resetting the Device To perform a factory reset, press and release the reset button, wait for 1 second, and then press and hold the config button for 20 seconds. After releasing the config button, wait for 2 seconds, then press and release the reset button again. This sequence will effectively factory reset the device.
Step 1 : Power up the sensor.
Step 2: Every sensor has 2 buttons: Reset and Configuration (RST and CFG). Enter configuration mode by holding both buttons down. Next, release the reset button. Wait 6 seconds and release the CFG button. The sensor will send a Configuration API frame, indicating configuration mode is active. The API frame will look similar to this:
7E 00 1C 90 00 13 A2 00 41 91 1B 83 FF FE C2 7A 00 00 00 23 00 00 50 47 4D 00 00 00 00 00 00 0A
Above command contains the sensor MAC address. This MAC address may be used to send future targeted commands to this particular sensor.
In the above case, the MAC address is:
00 13 A2 00 41 91 1B 83
Note: Throughout this guide we will be sending data in broadcast mode and sensors ID and node ID will be set to 0. This is done to make these commands work with all the sensors and all the nodes. These commands may be used with all the sensors without any change.
For optimal performance keep only one sensor in config mode at a time.
Reminder: During configuration mode, the sensor PAN id needs to be set as 0x7BCD.
Warning: Batteries will drain quickly in configuration mode. Be sure to exit configuration mode as soon as possible by pressing and releasing the Reset (RST) Button on the sensor once configuration changes have been completed.
Read Sleep Duration
This command may be used to read the sensor sleep duration. The sleep duration determines how frequently the sensor wakes up and send sensor data. The interval is set in seconds. Short intervals will drain the battery faster while longer intervals will provide a very long battery life.
Read Sleep Duration Command
7E 00 13 10 00 00 00 00 00 00 00 FF FF FF FE 00 00 F7 15 00 00 00 E8
In the above command the remote device address is set as broadcast. The address is:
00 00 00 00 00 00 FF FF
When sending this command to a particular sensor, replace the MAC address of the sensor. Again, the sensor MUST be in configuration mode.
The Wireless Sensor will respond with the stored delay value:
7E 00 1C 90 00 13 A2 00 41 91 1B 83 FF FE C1 7C 00 02 00 0E 00 00 00 02 58 00 00 00 00 00 00 A6
From the above command, the following data may be extracted:
A. Sensor MAC address
00 13 A2 00 41 91 1B 83
B. Sensor Over-all Payload
7C 00 02 00 0E 00 00 00 02 58 00 00 00 00 00 00
C. Delay Value
0x00 0x02 0x58 (data bytes 23, 24, and 25)
Delay in Seconds = (0x00 x 65536) + (0x02 x 256) + 0x58 = 600 Seconds = 10 Minutes
Set Sensor Node ID and Sleep Duration
This Command may be used to set the sensor node and sleep duration, note that both values are stored together using the same command. The Node ID is a user-defined value from 00 to FF that may be used to help easily identify a sensor. The Sleep Duration indicates the amount of time (in seconds) the sensor will sleep before waking up, taking a sample, sending a transmission, and going back to sleep.
Set Node ID and Sleep Duration Command Example:
7E 00 17 10 00 00 00 00 00 00 00 FF FF FF FE 00 00 F7 02 00 00 00 01 00 01 2C CD
In the above command, the remote device address is set to broadcast mode. The broadcast address is 00 00 00 00 00 00 FF FF, which will target all sensors in configuration mode. Change the broadcast address to the MAC address of a individual sensor to target a particular sensor with this command (this is usually not required). The Command Contains a Sensor payload which contains a Sensor Node ID and Delay value.
Payload
F7 02 00 00 00 01 00 01 2C
Note that F7 is the command header byte and 02 is the sub command for storing the Node ID and Sleep Duration.
A. Node ID
0x01 (Byte 23)
B. New Delay Value
00 01 2C (data bytes 24, 25, and 26)
Delay in seconds = (0x00 x 65536) + (0x01 x 256) + 0x2C = 300 Seconds = 5 Minutes
In the Above command we set the new node to 1 and sleep duration value to 300 seconds (5 Minutes).
Once the sensor receives this command, it will send a response back. This response will indicate success or failure of the command.
In his case, the response will look something like this:
7E 00 1C 90 00 13 A2 00 41 91 1B 83 FF FE C1 7C 01 05 00 0E 00 00 FF 00 00 00 00 00 00 00 00 FD
Read Sensor Network ID
The Network ID is also known as PAN ID (Personal Area Network ID). This feature may be used to build a private Wireless Sensor Network. All sensors with the same Network ID will be able to talk to modems and gateway with the same Network ID. This is useful when deploying hundreds of sensors in one area or applications which require division of sensors, modems, and gateways into different zones with independent monitoring of each zone. Each sensor, gateway, and modem in a specific zone should share identical Network IDs, allowing the separation of sensors into smaller, more manageable groups.
Large factory floors or high-rise building may consist of several groups of sensors working under different Network IDs that help characterize the different areas of the installation. Network IDs make it easy to group sensors, modems, and gateways. When broadcasting data using separate Network IDs, multiple modems and gateways may be used in each zone, allowing sensor data to be collected by several different computers or servers. This kind of redundancy is essential in large installations.
Read Sensor Network ID Command
7E 00 13 10 00 00 00 00 00 00 00 FF FF FF FE 00 00 F7 19 00 00 00 E4
Sensor will respond with the Network ID
7E 00 1C 90 00 13 A2 00 41 91 1B 83 FF FE C1 7C 00 05 00 0E 00 00 7F FF 00 00 00 00 00 00 00 7F
From the above response, following data may be extracted:
A. Sensor MAC Address
00 13 A2 00 41 91 1B 83
B. Complete Sensor Payload
7C 00 05 00 0E 00 00 7F FF 00 00 00 00 00 00 00
C. Network ID
0x07FF (data bytes 23 and 24)
Set Wireless Sensor Network ID
This command may be used to set the sensor Network ID. Please note, Network ID 0x7BCD is reserved for configuration and should NEVER be used as a network ID for general use. Please note the Modem/Gateway must also use a matching Network ID to communicate with the sensor.
Set Wireless Sensor Network ID Command:
7E 00 15 10 00 00 00 00 00 00 00 FF FF FF FE 00 00 F7 05 00 00 00 7C DE 9E
Above Command Contains the following payload:
F7 05 00 00 00 7C DE
Note that F7 is the command header byte and 05 is the sub command for setting the Sensor Network ID.
In the Above command, a new network ID of 0x7CDE is configured.
Once the sensor receives this command, it will send a response back. This response will contain information regarding command success or failure.
In his case the response was successful, responding with the following frame:
7E 00 1C 90 00 13 A2 00 41 91 1B 83 FF FE C1 7C 00 09 00 0E 00 00 FF 00 00 00 00 00 00 00 00 FA
Read Sensor Destination Address
This Command may be used to read the sensor destination address. When the Sensor is in broadcast mode, the destination address will show up as:
0x0000FFFF
This Command may be used to read the sensor destination address.
Read Sensor destination address Command:
7E 00 13 10 00 00 00 00 00 00 00 FF FF FF FE 00 00 F7 18 00 00 00 E5
Sensor will respond with the Stored destination address:
7E 00 1C 90 00 13 A2 00 41 91 1B 83 FF FE C1 7C 00 13 00 0E 00 00 00 00 FF FF 00 00 00 00 00 F1
From the above command, the following data may be extracted:
A. Complete Sensor Payload
7C 00 13 00 0E 00 00 00 00 FF FF 00 00 00 00 00
B. Sensor MAC address
00 13 A2 00 41 91 1B 83
C. Destination Address
0000FFFF (data bytes 23, 24, 25, and 26)
The sensor response 0000FFFF indicates that the sensor is in broadcast mode. Any other value will indicate the sensor is directing its data to a specific address (a specific modem or gateway). We DO NOT ADVISE sending sensor data to a specific address, we advise broadcasting data using different Network IDs (PAN IDs) to put data into clustered zones. Should a specific gateway or modem fail while in service, it will be much easier to deploy a new gateway or setup redundant gateways and modems. Otherwise, reconfiguration of each sensor for a new gateway or modem will be required.
Set Sensor Destination Address
Every sensor is designed to send sensor data either in broadcast mode or to a particular destination address (modem or gateway). By default, NCD sensors broadcast data to all available modems and gateways. Data may be restricted to a single destination address (modem or gateway), though this configuration does not provide any form of redundancy in the event of a Modem or Gateway outage. For this reason, we strongly advise against using this command. Please consider setting the Network ID (PAN ID) to Setup Zones which will allow for redundancy in the event of a service outage. The following command is provided for reference ONLY and should be used with caution as a modem or gateway failure will necessitate reconfiguration of each sensor (which would not be required if the Pan ID/Network ID were used).
What is a Destination Address? Every sensor, gateway, and modem have a unique MAC address which cannot be changed. This MAC address is also known as the destination address (printed on the side of the enclosure). By default, all sensors send data in broadcast mode. This allows all the gateways and modems in the area to receive sensors data provided they are all on the same PAN ID (Network ID) and use the same encryption key.
When a specific destination address is stored in the sensor, the sensor will send data to that specific destination address only. The sensor CANNOT communicate with any other modem or gateway in the area. The following command may be used to specify a specific destination address (modem or gateway) for all sensor data:
Set Destination address Command
This command we will send only the lower 4 bytes of the destination address (the upper 4 bytes do not change).
7E 00 17 10 00 00 00 00 00 00 00 FF FF FF FE 00 00 F7 03 00 00 00 12 34 56 78 E6
The above Command Contains the payload, including a New Sensor destination address:
Complete Payload
F7 03 00 00 00 12 34 56 78
F7 is the command header byte and 03 is the sub command for setting a specific destination address. In this example, the new Destination Address is 12345678.
Once sensor receives this command it will send a response back. This response will indicate the command success or failure.
In his example, the response will look something like this (if successful):
7E 00 1C 90 00 13 A2 00 41 91 1B 83 FF FE C1 7C 00 0E 00 0E 00 00 FF 00 00 00 00 00 00 00 00 F5
Set Sensor Destination to Broadcast
This Command may be used to set the sensor destination address to broadcast mode, which is the default operation of NCD long range wireless sensors. After setting to broadcast mode, all modems and gateways with the same PAN ID and Encryption key will receive the same sensor data. This is the preferred configuration for all NCD sensors. Segmenting sensors into groups requires a unique PAN ID (also known as Network ID) for each group. All sensors, modems, and gateways must share the same PAN ID for each group.
Set Sensor Destination address to broadcast:
7E 00 13 10 00 00 00 00 00 00 00 FF FF FF FE 00 00 F7 01 00 00 00 FC
Complete Payload
F7 01 00 00 00
F7 is the command header byte and 01 is the sub-command for setting the Destination Address to Broadcast Mode.
Read Wireless Sensor Transmission Power Level
This Command may be used to read the wireless radio transmission power. This value will indicate how much RF power the radio is emitting. The higher the value, the higher the radiated wireless power, resulting in a longer range and decreased battery life (please note that all battery ratings are shown at maximum wireless transmission power). Lower values are desirable in application that may benefit from greatly improve battery life, especially when high power data transmissions are not required.
Read Sensor Power Command:
7E 00 13 10 00 00 00 00 00 00 00 FF FF FF FE 00 00 F7 16 00 00 00 E7
Sensor will respond with the Power Level value:
7E 00 1C 90 00 13 A2 00 41 91 1B 83 FF FE C1 7C 00 09 00 0E 00 00 04 00 00 00 00 00 00 00 00 F5
From the above command, the following data may be extracted:
A. Sensor MAC Address
00 13 A2 00 41 91 1B 83
B. Sensor Payload
7C 00 09 00 0E 00 00 04 00 00 00 00 00 00 00 00
C. Power Level
0x04 (data byte 23)
The sensor will respond with a value from 0x00 to 0x04. The default value is 0x04, allowing for the greatest possible transmission range and the shortest battery life.
Read Wireless Sensor Retries
The following command may be used to read the number of retires. The number of retries is one of the most useful settings for NCD wireless sensors.
Lets say the number of retires is set to 5. In a normal case, the sensor will wake up, gather data, send data to the modem, and go back to sleep. But due to some environmental issues (lets say a few trucks were driving by and they came in between the sensor and the modem) the modem didn’t receive the data. In that case, the sensor will try 4 more times to send the data. If the modem still doesn’t get the data after all 5 tries, the sensor will quite trying and will go back to sleep. The sensor will wake up after the predefined sleep time and will try again.
The highest number of retries allowed is 10.
Read The number of Sensor Retries:
7E 00 13 10 00 00 00 00 00 00 00 FF FF FF FE 00 00 F7 17 00 00 00 E6
Sensor will respond with the Retries value:
7E 00 1C 90 00 13 A2 00 41 91 1B 83 FF FE C1 7C 00 1B 00 0E 00 00 0A 00 00 00 00 00 00 00 00 DD
From the above command, the following data may be extracted:
A. Sensor MAC Address
00 13 A2 00 41 91 1B 83
B. Complete Sensor Payload
7C 00 1B 00 0E 00 00 0A 00 00 00 00 00 00 00 00
C. Retries Number
0x0A (data byte 23)
Set Wireless Sensor number of Retries
This Command may be used to change the number of retries. The highest number of retries allowed is 10:
7E 00 14 10 00 00 00 00 00 00 00 FF FF FF FE 00 00 F7 06 00 00 00 05 F2
The above Command Contains a Sensor payload which contains a new number of retries value:
Complete Payload
F7 06 00 00 00 05
F7 is the command header byte and 06 is the sub command for setting the Retries value.
In the Above command we set the retries value to 5 (byte 23).
Once the sensor receives this command, it will send a response back. This response will contain the info regarding command success or failure.
In his case the response was successful:
7E 00 1C 90 00 13 A2 00 41 91 1B 83 FF FE C1 7C 00 1D 00 0E 00 00 FF 00 00 00 00 00 00 00 00 E6
Set Wireless Sensor Encryption Key
This Command may be used to set the encryption key.
All ncd.io wireless sensors comes with 128bit AES encryption. The default encryption key secures a wireless sensor network of sensors, modems, and gateways. Users have the option to change the default encryption key. Please note this is a Write ONLY operation, it is not possible to read the encryption key from Sensors, Modems, or Gateways. Be Sure to keep records accordingly.
Once the sensor encryption key is set in the sensor, be sure to set the same key in all modems and gateways. If the modem or gateway doesn’t have the same key and PAN id as the sensor, there will be no way for sensors to communicate with modems or gateways. In this event, only a factory reset may be used to recover communications.
The following Command may be used to change the encryption key:
7E 00 24 10 00 00 00 00 00 00 00 FF FF FF FE 00 00 F2 03 00 00 00 00 55 AA 55 AA 55 AA 55 AA 55 AA 55 AA 55 AA 55 AA 07
Complete Payload
F2 03 00 00 00 00 55 AA 55 AA 55 AA 55 AA 55 AA 55 AA 55 AA 55 AA
F2 is the command header byte and 03 is the sub command for setting the ENY Key value.
Note — There is an Extra 0x00 Right before the ENY key value. Its a reserve byte and it should be there all the time.
In the Above command, the default ENY Key value is programmed into the NCD sensor.
55 AA 55 AA 55 AA 55 AA 55 AA 55 AA 55 AA 55 AA
Once the sensor receives this command, it will change the Key immediately.
In the event a key value is lost, factory reset the device. The default key value will always be used after factory reset:
55 AA 55 AA 55 AA 55 AA 55 AA 55 AA 55 AA 55 AA
Configuration Commands Table
No. | Command | Header | Sub Command | Parameter Field | Default Value | Description |
---|---|---|---|---|---|---|
1 | Set Broadcast Transmission | 0XF7 | 0x01 | – | 0000FFFF | This will set the address to Broadcast mode. All the receiver with same ENY key and PAN ID will get the data packets |
2 | Set ID and Sleep Interval | 0XF7 | 0x02 | NODE ID, D0 MSB,D1, D2 LSB | 0x00,0x00,0x02,0x58 | Sets the Device node ID and Data Transmission Interval. The node id value can go from 0-255 and The Data transmission value can go from 3-0xFFFFFF Seconds |
3 | Set Destination Address | 0XF7 | 0x03 | A0 MSB, A1, A2, A3 | 00,00,FF,FF | Sets the Destination Address of the sensor. The sensor will send Run mode Data packets to this Address |
4 | Set Power | 0XF7 | 0x04 | Power ( range 1-4) | 0x04 | Sets the RF power of the Sensor Radio |
5 | Set PAN ID aka Network ID | 0XF7 | 0x05 | ID0 MSB, ID1 LSB | 0x7FFF | Sets the PAN ID aka Network ID in the sensor. Only sensors, Gateway, and Modes with Same ID can communicate with each other |
6 | Set Retries | 0XF7 | 0x06 | Retries | 0x0A | Sets the number of Retries after unsuccessful transmission for the Sensor Radio |
7 | Read Sleep Interval | 0XF7 | 0x15 | – | 0x00,0x02,0x58 | Reads the stored Sleep Interval value from the sensor |
8 | Read Power | 0XF7 | 0x16 | – | 0x04 | Reads the stored RF Power value from the sensor |
9 | Read Retries | 0XF7 | 0x17 | – | 0x0A | Reads the stored Retries value from the sensor |
10 | Read Destination Address | 0XF7 | 0x18 | – | 00,00,FF,FF | Reads the stored Destination value from the sensor |
11 | Read PAN ID aka Network ID | 0XF7 | 0x19 | – | 0x7FFF | Reads the PAN ID aka Network ID |
12 | Enable Encryption | 0XF2 | 0x01 | – | 0x01 | Enables the Encryption of the Frame Transmitted from the Sensor |
13 | Disable Encryption | 0XF2 | 0x02 | – | – | Disables the Encryption of the Frame Transmitted from the Sensor |
14 | Set Encryption Key | 0XF2 | 0x03 | 00,K0 MSB, K1,K2,K3,K4,K5,K6,K7,K8,K9,K10,K11,K12,K13,K14,K15 | 55AA55AA55AA55AA55AA55AA55AA55AA | Sets the 128 bit AES Encryption Key |
Sensor App Specific Configuration Commands Table
COMMAND | COMMAND | SUB COMMAND | COMMAND CODE | ARGUMENT |
---|---|---|---|---|
SET Acceleration Threshold | 0xF4 | 0x20 | 0x14 | This example command will set the acceleration threshold to 20*32mg = 640mg |
GET Acceleration Threshold | 0xF4 | 0x21 | ||
Clear all counters | 0xF4 | 0x24 | 0x1F | Reset all counter values to 0 |
Clear Accelerometer Counter | 0xF4 | 0x24 | 0x08 | Reset Acc counter values to 0 |
Clear Magneto Counter | 0xF4 | 0x24 | 0x10 | Reset AMag counter values to 0 |
Activate Accelerometer | 0xF4 | 0x25 | 0x01 | Activate Accelerometer |
De-Activate Accelerometer | 0xF4 | 0x25 | 0x00 | De-Activate Accelerometer |
Set Debounce Time | 0xF4 | 0x27 | 0x64 | This will set debounce value to 100msec |
Get Debounce Time | 0xF4 | 0x28 | read stored debounce time Value |
Device Inputs and Working Principle
7
NPN and PNP Sensor Basics: These sensors operate within a voltage range of 9 to 24 volts. The output voltage can either match the input voltage or typically be around 5 volts, depending on the sensor type. For instance, a beam break sensor, when its beam is interrupted, outputs 5 volts, and when the beam is intact, it outputs 0 volts.
Connection via the M1 Connector: This involves ensuring the internal cable connects from M1 to the opto-coupler (opto). The M1 connector has specific pins for various connections: Pin 1 for input positive, Pin 2 for 3.3 volts, Pin 3 for input negative, Pin 4 for ground, and Pin 5 for VIN (Voltage Input).
Beam Break Sensor Connection: The positive lead of the beam break sensor (or power supply positive) connects to Pin 5, the ground to Pin 4, and the sensor’s signal output to Pin 3. This setup allows the system to detect beam interruptions, count their occurrences and durations, and send this data to a receiver or gateway based on predefined intervals.
24 Volt AC or DC Signal Reading: The same M1 connector setup can read 24V signals from machinery or devices like PLCs or SCADA systems. Connections for these signals are similar to the beam break sensor, with the primary difference being the connection of 24V positive and negative signals between Pin 1 and Pin 3.
Current Sensor Connection: The current sensor also connects to the M1 connector. Users must ensure the Molex cable runs from M1 to the current sensor. The sensor, designated as 100 MCT, allows for threshold setting via an onboard potentiometer. This setup is designed to monitor current flow, triggering the system when current exceeds a predetermined threshold (e.g., 5 amps).
Digital Input Pin Connection: Alongside the current sensor, a digital input pin for contact closure inputs (e.g., from relay boards or read switches) can be connected. This allows the device to count cycles and monitor on-time based on the state of these inputs.
Open Collector Inputs: Some sensors provide open collector outputs when active. To use these, the sensor’s output needs to be pulled high or low using onboard switches. The system counts on-time and cycles based on the sensor’s state, with connections similar to those for the opto-coupler.
Uptime Calculation via Acceleration and Magnetic Field Detection: Beyond electrical signals, the system can calculate uptime through vibration (acceleration) and magnetic field detection. Users set thresholds for these parameters, enabling the device to start or stop counting based on the presence of vibrations or a magnetic field, respectively.
This comprehensive approach ensures versatile and accurate monitoring of machine uptime, accommodating a wide range of sensor types and signals.
Installation Guidelines
8
Vibration Sensor installation is an extremely critical step; in order to ensure the best results, sensor mounting guidelines should be followed.
A. Sensor Main Body Mount — The sensor main body has four magnets. These magnets make it easy to mount. During mounting, make sure
- The sensor is Powered on ( the switch should be positioned towards the wall of the enclosure if using battery and on the other side if using with external power)
- The antenna is installed and pointed vertically to the ground
- Install the main sensor box as high as possible to avoid any object that might come in between the sensor and modem/gateway
- Antenna should not be installed inside any metal box
B. Sensor Probe — Mounting will depend on the probe type.
Troubleshooting Guide
9
ncd vibration sensor V3 can be used with any ncd modems and gateway and from there data can be pushed to any cloud or local server.
If there is no data on the gateway side, here are few things users can check
- Sensor is powered on
- Batteries are in good condition ( Leaving the sensor in cfg mode for a long time will drain batteries)
- Antenna is connected and pig tail is secured
- Press the reset button and sensor will send a welcome message followed by a sensor data packet.
- Check the LED status. if the LED is blinking as expected, means sensor is working
On the Receiver side —
- If you are using a modem make sure correct port settings are selected
- Sensor radio module and Modem/gateway radio module are of same frequency
- Gateway is connected to WiFi
- Gateway and Sensor are atleast 3 feet apart