Explore the Machine Monitor Sensor Capabilities
Device Overview
The Machine Uptime Monitor is a device specifically designed to track machine and production uptime in industrial settings. It is a flexible device that can be configure to observe one or more events via different input types – accelerometer, magnetometer, current sensor, break beam sensor, photo eye sensor, reflector sensor, current sensor.
It has long range wireless capabilities utilizing robust Mesh networking protocols with high level of security and network reliability. It is compact, durable and powered by long lasting batteries. Its main feature include:
- Industrial Grade Machine Uptime Monitoring
- Measure Production Uptime
- Measure Number of Cycles
- Dry Contact Closure Input
- Wet Contact Closure Input
- Acceleration Motion Detection based Uptime calculator
- Magnetic Field Detection based Uptime calculator
- Current-based Uptime calculator
- Encrypted Communication with 2 Mile Wireless Range
- Operating Temperature Range -40 to +60 °C
- Humidity Range 0-90%
- Wall-Mounted or Magnet Mounted IP65 Rated Enclosure
- For Indoor and Outdoor Use
- Many Gateway and Modem Options Available
Status LED
The Status LED is used to indicate errors or other sensor diagnostics.
LED blinks once – Message was sent successfully and no error in last sensor read as well in data transmission.
LED blinks twice and then one more time – Message was sent successfully but there was an error in last sensor read.
LED blinks thrice – MCU is having issue communicating with the radio module.
Sensor Specifications
Specifications | Minimum | Nominal | Maximum | Notes |
---|---|---|---|---|
Width | 3.54" | |||
Length | 4.52" | |||
Height | 2.16" | |||
Enclosure Rating | IP65, NEMA 1,2,4,4X,12,13, UL-508 | |||
Temperature Rating | -40° C | 23° C | 85° C | Component Rating |
Tested Temperature | 0° C | 23° C | 40° C | As Tested by NCD Staff |
Probe Operating Temperature | -40° C | 23° C | 85° C | As Tested by NCD Staff |
Inputs | Digital, Acceleration, Magnetic, Current | |||
Opto-input Voltage | 3.3 V | 24V | ||
Reporting interval | 5 seconds | 600 seconds | 16777215 seconds | How often data is transmitted wirelessly |
Range of counter values | 1 | 4294967295 | The maximum number of events the sensor can count to | |
CT Current | 1.5% FS | FS | Minimum current read by the CT. CT range 100 to 1000Amp |
Printed Circuit Board Specifications
Parameter | Minimum | Nominal | Maximum | Notes |
---|---|---|---|---|
Trace Width | 0.007 inch | 0.012 inch | 0.25 inch | Trace Width depends on the Trace Type |
Layer Count | 2L - Rigid | Top and Bottom Layer | ||
Material Type | FR-4 TG170 | FR-4 TG170 | FR-4 TG180 | |
Surface Finish | ENIG 2u" | |||
IPC Standard | IPC CLASS 2 | |||
Finished Copper Foil | 1.0/1.0 OZ | |||
Finished Thickness | 0.062 inc | |||
Fine line <4.0/4.0mil | No | |||
Blind & Burried Vias | No | |||
Non-Conductive Resin | No | |||
Conductive Resin | No |
Mechanical Drawing
RF Module Specifications
Parameter | 868MHz | 900MHz | 2.4GHz |
---|---|---|---|
Frequency Band | 863 MHz to 870 MHz | 902 to 928 MHz | ISM 2.4 GHz |
Transmitter Power | Up to 13 dBm ERP | Up to 24 dBm | Up to 8 dBm |
Receiver Sensitivity | -106 dBm at 80 Kbps | -101 dBm at 200 Kbps | -103 dBm at 250 Kbps |
Range (dense urban) | ~1000ft | ~1000ft | ~300ft |
Range (line of sight) | ~2 miles | ~2 miles | ~1 mile |
Data Rate | 80 Kbps | 200 Kbps | 250 Kbps |
Networking Protocol | Digi XBee® DigiMesh® | Digi XBee® DigiMesh® | Digi XBee® DigiMesh® |
Encryption | 128-bit AES | 128-bit AES | 128-bit |
Reliable Packet Delivery | Retries/acknowledgements | Retries/acknowledgements | Retries/acknowledgements |
IDs | PAN ID and addresses, cluster IDs and endpoints (optional) | PAN ID and addresses, cluster IDs and endpoints (optional) | PAN ID and addresses, cluster IDs and endpoints (optional) |
Certification | CE/RED, ROHS Compliant | FCC (America), IC (Canada), C-Tick (Australia), Anatel (Brazil), IDA (Singapore) | FCC (America), IC (Canada), RCM (Australia), Anatel (Brazil), Teleck MIC (Japan), KCC (South Korea) |
Probes Specifications
There are 4 types of probes: Bare wire for digital inputs, Current sensor, Accelerometer, and Magnetometer.
Digital Inputs
The Industrial Digital Input and Sensor Reader is a compact and robust device tailored to interpret signals from various digital inputs and sensors prevalent in industrial settings, including brake beam sensors, photo reflectors, photo eye sensors, and on/off signals. It can also work with counter with a digital pulse outputs to easily integrate with existing equipment in production lines or plants for example.
With high accuracy and reliability, it offers real-time data acquisition and monitoring, seamlessly integrating into existing industrial automation systems. Its user-friendly interface and flexible configuration options ensure easy setup and compatibility with diverse applications, enhancing operational efficiency, equipment reliability, and production optimization. Ideal for conveyor systems, packaging machinery, and robotic systems, it empowers industrial operators with streamlined data interpretation and control capabilities, minimizing downtime and maximizing productivity.
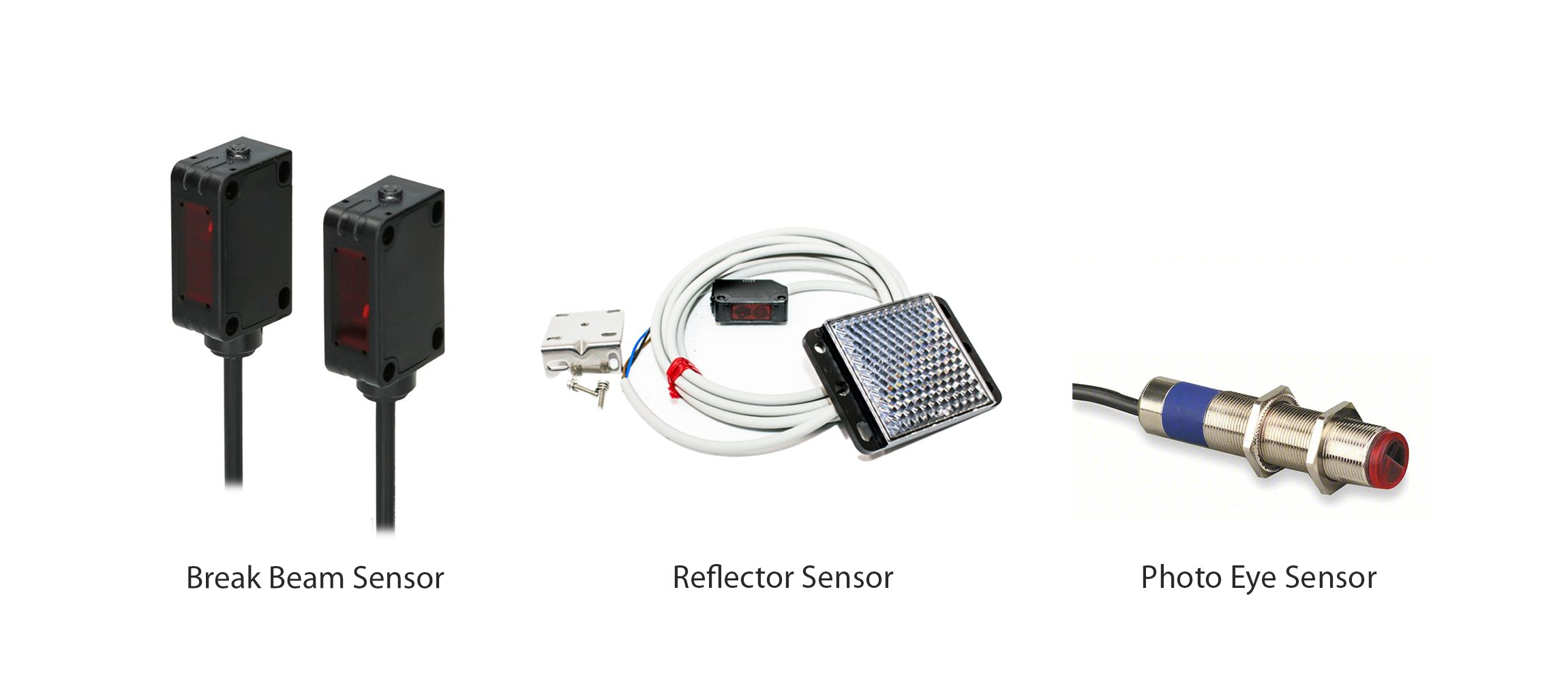
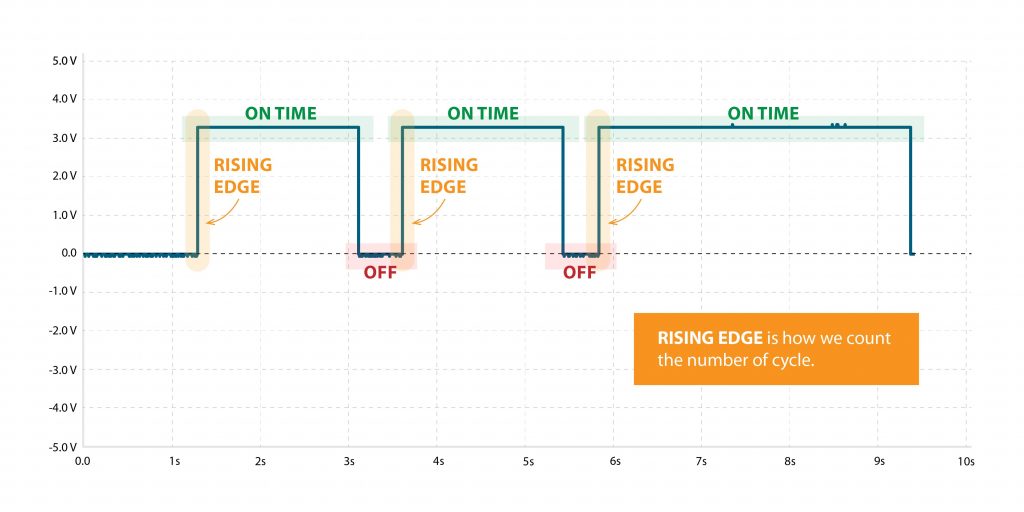
Accelerometer Sensor
The Cycle and Uptime Tracker is an innovative device engineered to monitor and record the number of cycles and total uptime of machinery or equipment in industrial environments. Leveraging advanced acceleration sensing technology, users can set customizable acceleration thresholds to precisely detect cycle initiations. This allows for accurate tracking of machine activity while minimizing false readings. The device captures and stores data, providing insights into equipment usage patterns and overall uptime. With its user-friendly interface and customizable settings, operators can easily configure acceleration thresholds to suit specific machinery requirements. Ideal for diverse industrial applications, the Cycle and Uptime Tracker enhances maintenance planning, optimizes production scheduling, and improves operational efficiency.
Magnetometer Sensor
Magnetic Field-Based Machine On/Off Detection System is meticulously engineered to precisely discern the operational status of machinery that emits magnetic fields during operation. Employing cutting-edge magnetic field sensors, this system offers unparalleled accuracy in identifying whether the machine is active or inactive. With its robust design and reliable performance, there’s no need for user adjustments, ensuring hassle-free operation. Real-time monitoring capabilities enable proactive maintenance planning and energy conservation, enhancing operational efficiency. Seamlessly integrating into various industrial setups, this system represents a pinnacle of reliability and professionalism in machine monitoring solutions.
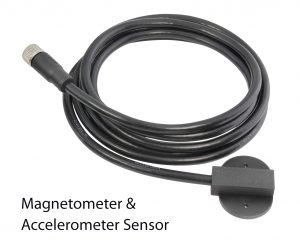
Current Sensor
Industrial Machine Uptime and Cycle Counter, a cutting-edge solution that accurately measures total machine uptime and cycle counts using advanced current sensor technology. With real-time monitoring and seamless integration, our device enables proactive maintenance planning, enhances operational efficiency, and provides valuable insights for informed decision-making. Upgrade your industrial operations with precise tracking and analysis capabilities for optimized performance and cost savings.
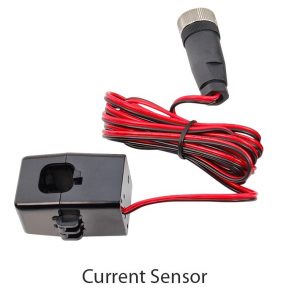
Probe Configuration and Wiring
Pin Definition
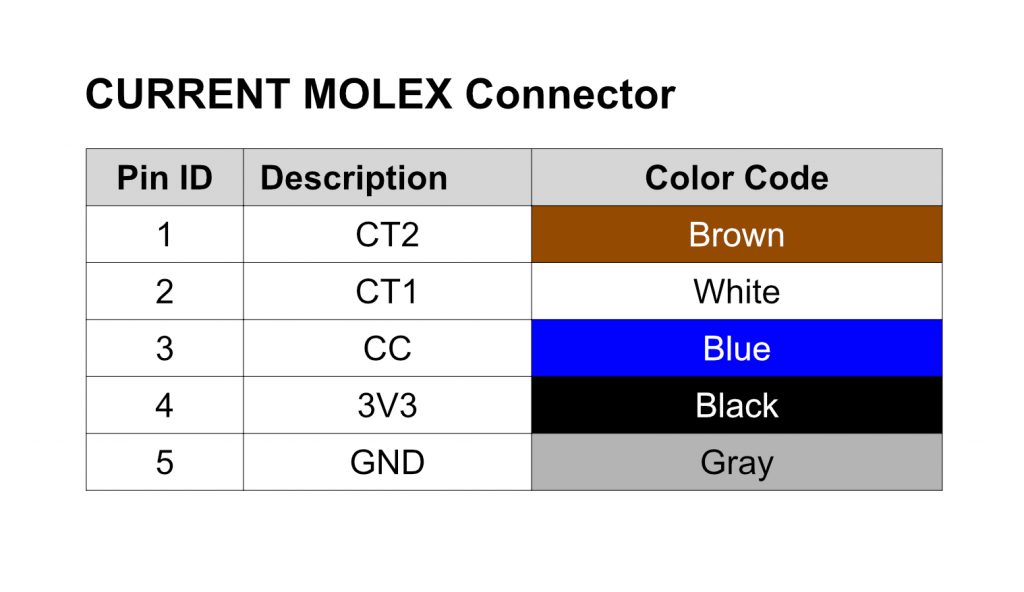
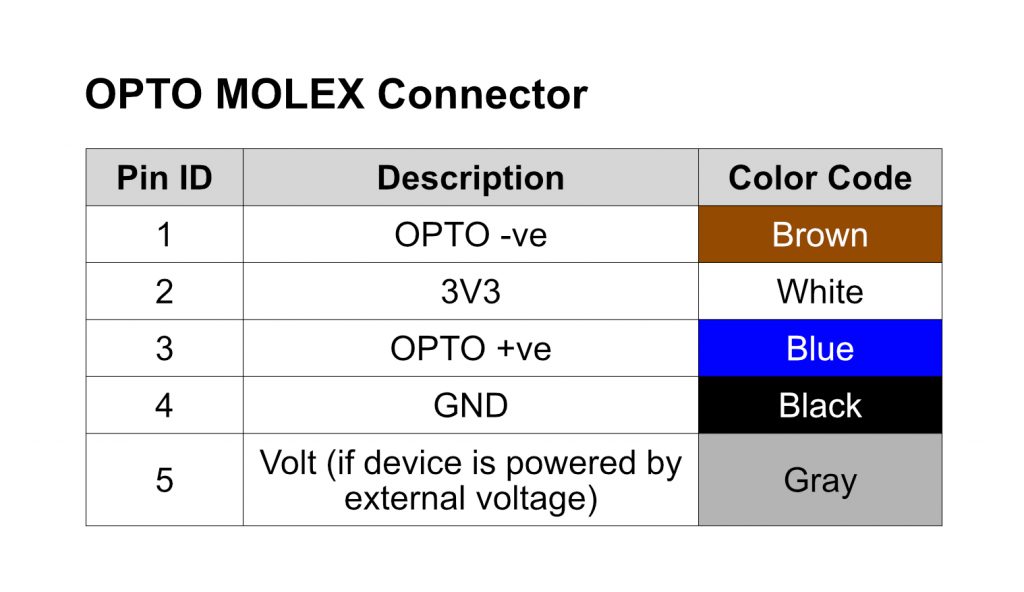
Example Probe Wiring
Depending on which probe configuration you chose you would gave to reroute the internal cabling between the M12 connector and the respective connector on the PCB. The images below show 4 example configurations.
Optical Sensor/Digital Input + Accelerometer + Magnetometer
Contact Closure + Accelerometer + Magnetometer
Contact Closure + Current Transducer
Accelerometer + Magnetometer Sensor
Current Sensor + Contact Closure Input + Optical Sensor/Digital Input

Power Requirements and Expected Battery Life
Power Requirements
This Sensor has two power options:
- Powered by AA batteries (NCD recommends Energizer L91 batteries)
- External power supply (5-12 V DC) Current Requirement 250 mA
While changing the batteries:
- Turn off the sensor
- Only use new L91 batteries
- Checkout the polarity marking on the battery holder and batteries
- Replace all six batteries with new L91 batteries. Do not mix old and new batteries
- Batteries should not be replaced in fire-risky areas
- Do NOT install rechargeable batteries
Expected Battery Life
Specifications | Minimum | Nominal | Maximum | Notes |
---|---|---|---|---|
Batteries | 2 | 6 | 6 | May be Powered by 2 or 4 AA Batteries |
Battery Life 1 TPD (Transmissions per Day) | 10 Years | Estimation is based on a 30 minute interval | ||
Battery Life 12 TPD (Transmissions per Day) | 8 Years | Estimation is based on a 30 minute interval | ||
Battery Life 24 TPD (Transmissions per Day) | 5 Year | Estimation is based on a 30 minute interval | ||
Battery Life 96 TPD (Transmissions per Day) | 3 Year | Estimation is based on a 30 minute interval |
Head to the NCD store if you want to purchase the Machine Uptime Monitoring Sensor.
If you already have the device and would like more information into its basic and advanced operations check out the Quick Start Guide and User Manual.