Device Overview
Introducing NCD’s IoT Industrial Wireless Absolute & Gauge Pressure and Temperature Sensor is the OEM piezo resistive pressure sensor with 316L stainless steel corrugated diaphragm and isolated oil-filling construction, boasting up to a 2 Mile range using a wireless mesh networking architecture. Incorporating a highly accurate Absolute & Gauge pressure sensor, transmits data at user-defined intervals. It measures Absolute & Gauge pressure and temperature with user configurable resolution at user defined intervals while sleeping during the time when it is not measuring or sending data.
Industrial Wireless Absolute & Gauge Pressure and Temperature Sensor is widely used for various liquid pressure measurement which is compatible with stainless steel and Viton®. The included sensor is rated for 0-100psi absolute pressure, 0-500psi gauge pressure sensor, 0-1000psi sealed gauge sensor with an accuracy of ±0.5%FS (pressure), and 0-5000psi sealed gauge sensor with an accuracy of ±0.5%FS (pressure) ±1.5℃ (Temperature). Easily interfaces using a standard 1/4″ NPT Male connection.
Features
- Industrial Grade Sensor Long Range Wireless Pressure Temperature Sensor
- Operating Range 0 to 10,000psi, -40°C to +85°C (-40°F to 185°F)
- Industry Standard 1/4 inch NPT Male Connector
- Accuracy ±0.5%FS (pressure) ±1.5℃ (Temperature)
- Sampling Frequency 1.5ms
- Long Term Stability: ±0.3%FS/year
- Compatible Media – Gas, Liquid or Vapor
- 2 Mile Range with On-Board Antenna
- Superior LOS Range of up to 28 miles with High-Gain Antennas
- Wireless Mesh Networking using DigiMesh®
- Open Communication Protocol for custom interfacing applications
- Node-RED compatible – for configuration and displaying of data (NCD provided libraries)
- IP65 Rated Enclosure
- Improved reliability incorporating Retry feature in case of packet loss
- Real Time Battery Status
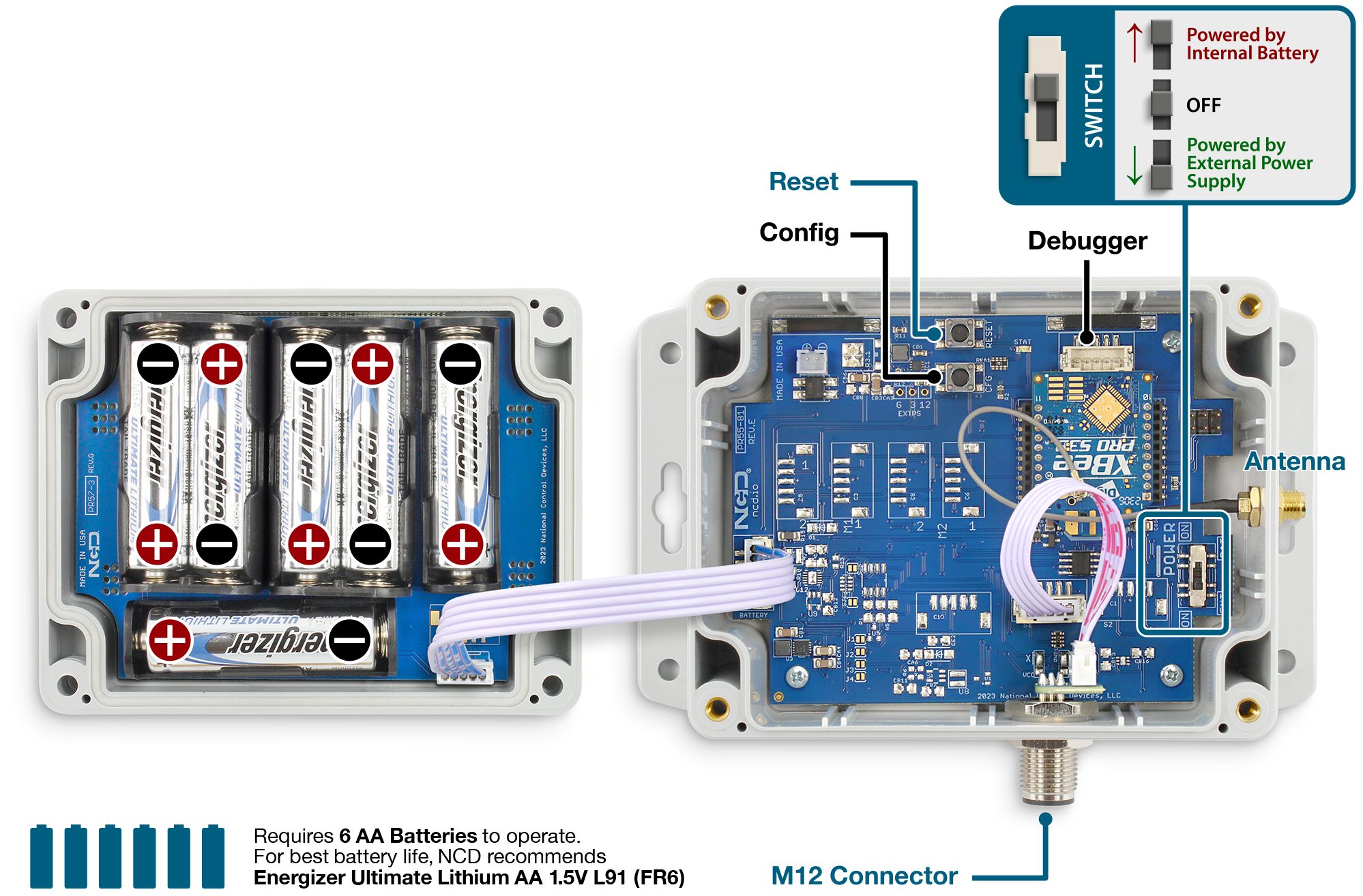
Wireless Technology
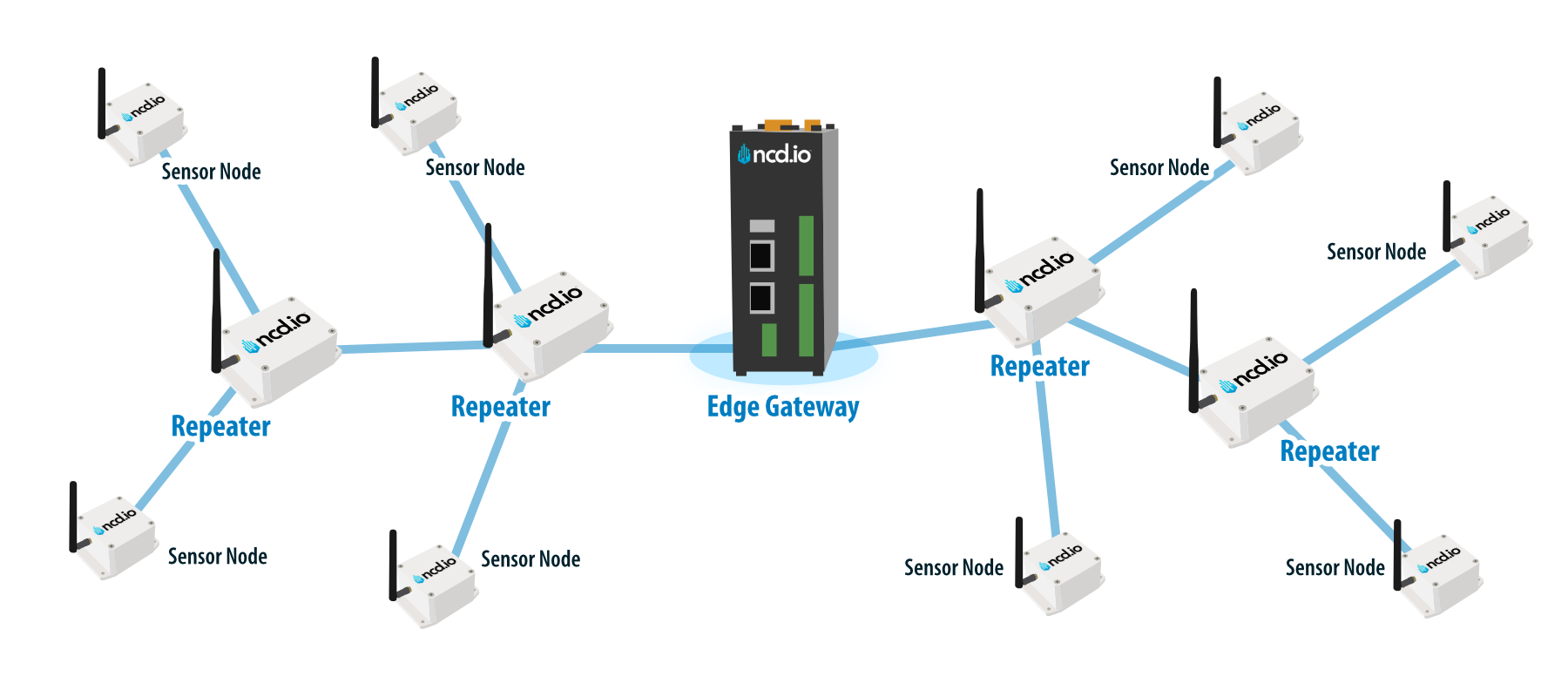
The NCD Industrial range of sensors utilizes DigiMesh, a proprietary networking technology designed by Digi® International. It is especially suitable for IIoT applications as it provides a number of benefits over conventional wireless stacks:
- Long range – up to 1200 feet in urban environments and 2 miles+ in open areas with the included antennas
- Mesh networking topology – no single point of failure, self healing network with high redundancy.
- Long battery life due to low power consumption – up to 10 years
- Simplified provisioning – extending the mesh network via repeater at no additional configuration complexity
- Works in the 868MHz, 900MHz and 2.4GHz bands – worldwide region interoperability.
Battery Life
Specifications | Minimum | Nominal | Maximum | Notes |
---|---|---|---|---|
Batteries | 2 | 6 | 6 | May be Powered by 2 or 4 AA Batteries |
Battery Life 6 TPD | 10 Years | TPD Transmissions per Day | ||
Battery Life 12 TPD | 8 Years | TPD Transmissions per Day | ||
Battery Life 24 TPD | 6 Year | TPD Transmissions per Day | ||
Battery Life 96 TPD | 4 Year | TPD Transmissions per Day |
Battery | |
Transmissions Per Hour | |
Expected Battery Life |
The Truth About Battery Life
Under the best of circumstances, the best non-rechargeable batteries commonly available today are limited to a 10 year non-working shelf life in a room temperature environment. Factors such as actual usage, temperature, and humidity will impact the working life. Be wary of any battery claims in excess of 10 years, as this would only apply to the most exotic and expensive batteries that are not commonly available. Also note that most battery chemistries are not rated for use in extreme temperatures. NCD only uses the best Non-Rechargeable Lithium batteries available today, which are also rated for use in extreme temperatures and have been tested by our customers in light radioactive environments. Lithium batteries offer a 10 year maximum expected shelf life due to limitations of battery technology. NCD will never rate sensor life beyond the rated shelf life of the best batteries available today, which is currently 10 years.
Applications & Use-cases
This sensor is a versatile device that brings a new level of precision and reliability across a wide range of industrial applications. Its unique combination of sensor capabilities, coupled with robust wireless communication and a durable enclosure, makes it an ideal choice for diverse environments and challenging operational conditions.
Absolute & Gauge Pressure Sensor Applications
Remote Monitoring of Industrial Fluid Systems
This sensor can be deployed in fluid systems such as water, oil, or gas pipelines to monitor pressure levels remotely. By integrating this wireless pressure sensor into pipelines, facility operators can ensure that the pressure remains within safe operating limits, preventing leaks, bursts, or other failures. Continuous pressure monitoring is essential in industries like oil and gas, water treatment, and chemical processing, where maintaining optimal pressure levels is critical to system integrity and safety.
HVAC and Refrigeration System Pressure Control
The sensor can be used to monitor the pressure in HVAC and refrigeration systems, where maintaining the right pressure is essential for system performance and energy efficiency. It can measure pressure in refrigerant lines, compressors, and cooling circuits to detect any fluctuations that might indicate issues such as refrigerant leaks or compressor malfunctions. By wirelessly transmitting pressure data, the sensor enables real-time monitoring and early detection of potential problems, reducing the risk of system failures and improving overall energy efficiency.
Tank Level Monitoring in Industrial Storage Systems
In large industrial tanks used for storing liquids or gases, the sensor can be installed to measure pressure at the bottom of the tank, which directly correlates with the fluid level inside. By monitoring the pressure, facility operators can accurately determine the fill levels of storage tanks in real-time. This is especially useful in industries such as chemical manufacturing, food processing, or fuel storage, where precise control over inventory levels is crucial for operational efficiency, safety, and avoiding costly overflows or shortages.
Boiler and Steam System Pressure Regulation
The sensor can be integrated into steam systems and industrial boilers to monitor and control pressure levels. Maintaining the correct pressure in steam systems is vital for ensuring efficient operation and safety. The wireless capability allows for real-time pressure monitoring in environments where wired solutions may be impractical or unsafe. This application is particularly relevant in industries like power generation, food processing, and pharmaceutical manufacturing, where steam is used extensively, and precise pressure control is necessary to maintain operational safety and efficiency.
Absolute & Gauge Pressure Sensor Use-cases
Oil and Gas Pipeline Pressure Monitoring in Remote Areas
In an oil and gas operation, pipelines often run through remote or hazardous environments, making it challenging to manually inspect and maintain them. This wireless pressure sensor can be installed at critical points along the pipeline to monitor pressure levels in real-time. By wirelessly transmitting the data to a central control center, operators can quickly detect pressure drops that could indicate leaks or blockages. This allows for immediate action to prevent environmental disasters and costly pipeline repairs, ensuring the safety and efficiency of the entire system without the need for constant on-site personnel.
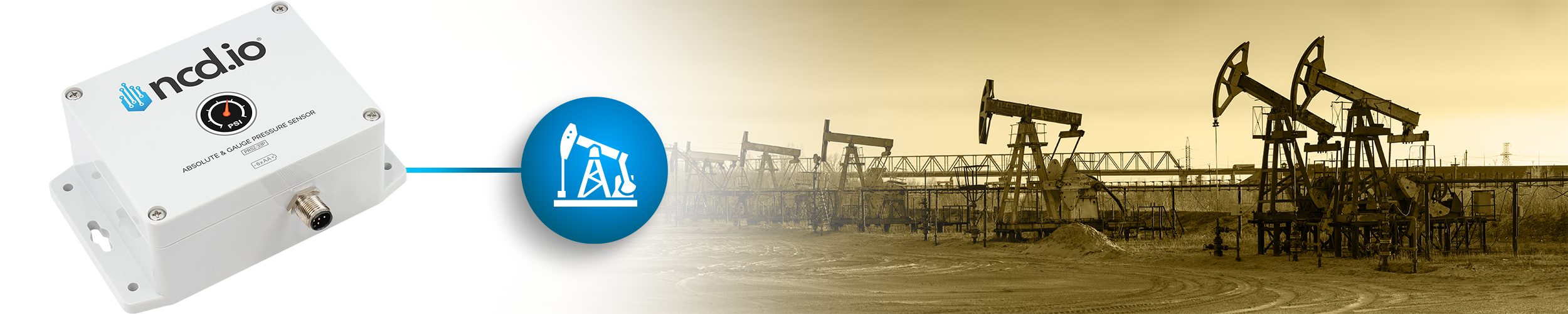
Refrigerant Leak Detection in Commercial HVAC Systems
In large commercial HVAC systems, maintaining proper refrigerant pressure is essential for optimal cooling performance. The sensor is installed in refrigerant lines to monitor pressure levels in real-time. If the pressure drops below a certain threshold, it could indicate a refrigerant leak, which would reduce system efficiency and potentially lead to costly repairs. The wireless sensor alerts maintenance teams immediately, allowing them to fix the issue before it affects the overall performance of the system or results in equipment failure, helping extend the life of HVAC units and reducing energy costs.
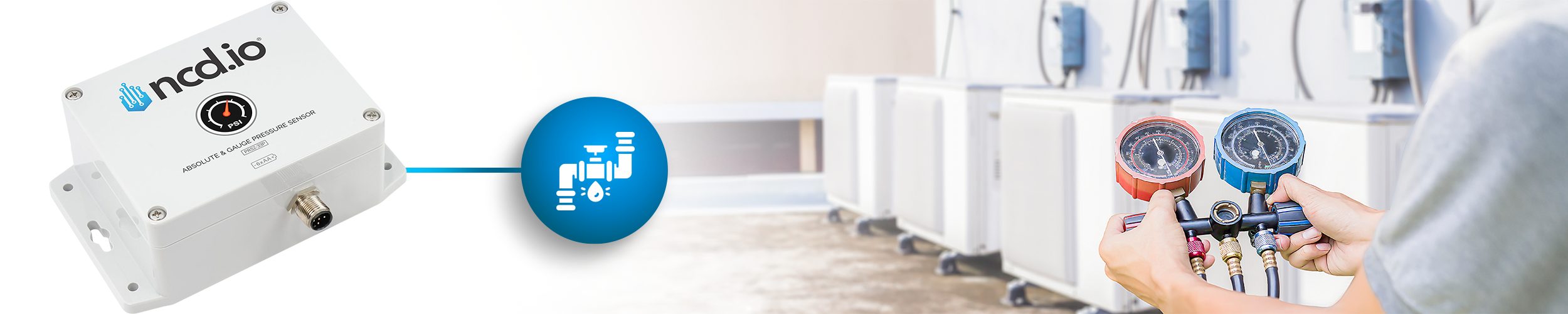
Chemical Tank Level Monitoring in Manufacturing Plants
In a chemical processing plant, tanks are used to store a variety of liquids, and keeping track of the volume of each substance is crucial to avoid shortages or spills. By placing the pressure sensor at the bottom of the tank, the facility can continuously monitor the liquid level based on pressure readings. The sensor wirelessly transmits this data to the plant’s monitoring system, allowing operators to view tank levels in real-time and schedule refills or transfers as needed. This prevents costly downtime caused by running out of essential chemicals or overfilling tanks, while also improving worker safety by reducing the need for manual inspections in hazardous areas.
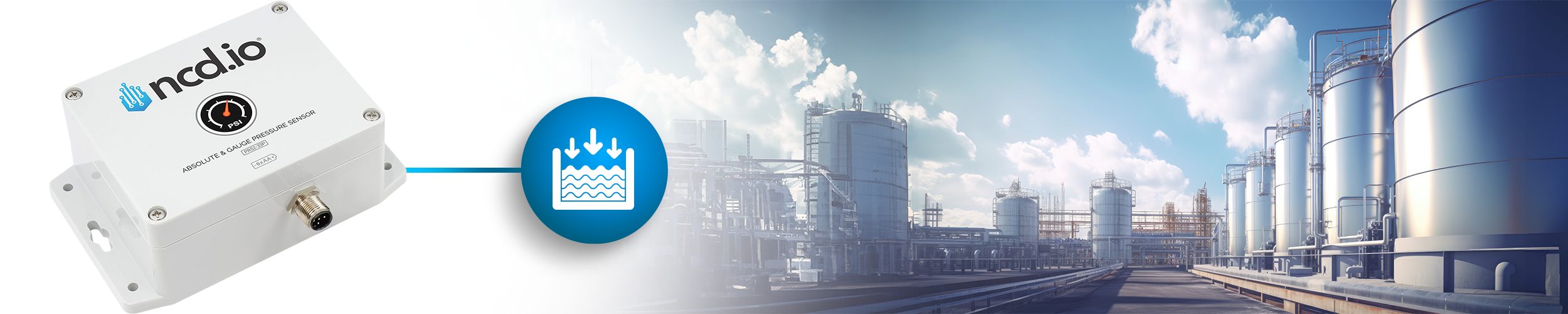
Steam Boiler Safety in Power Generation
In a power plant, steam boilers are critical for generating electricity, but maintaining proper pressure is vital to prevent explosions or operational inefficiencies. The sensor can be installed on the steam lines leading from the boiler to continuously monitor pressure. Wireless transmission of this data allows for real-time monitoring from the control room, ensuring that pressure stays within safe operating limits. If the pressure rises unexpectedly, operators can quickly shut down the system or take corrective actions before a failure occurs. This ensures the safe and reliable operation of the boiler, protecting both personnel and equipment from potentially catastrophic incidents.
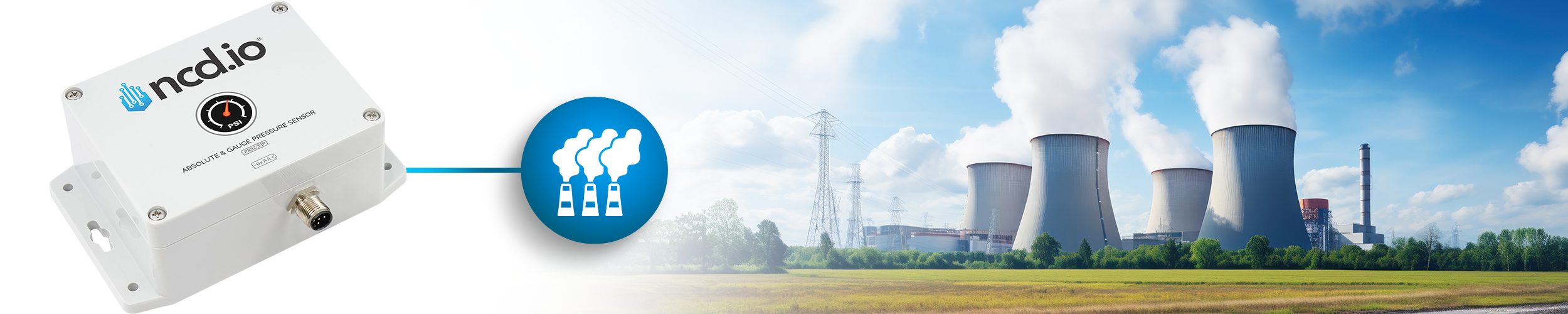